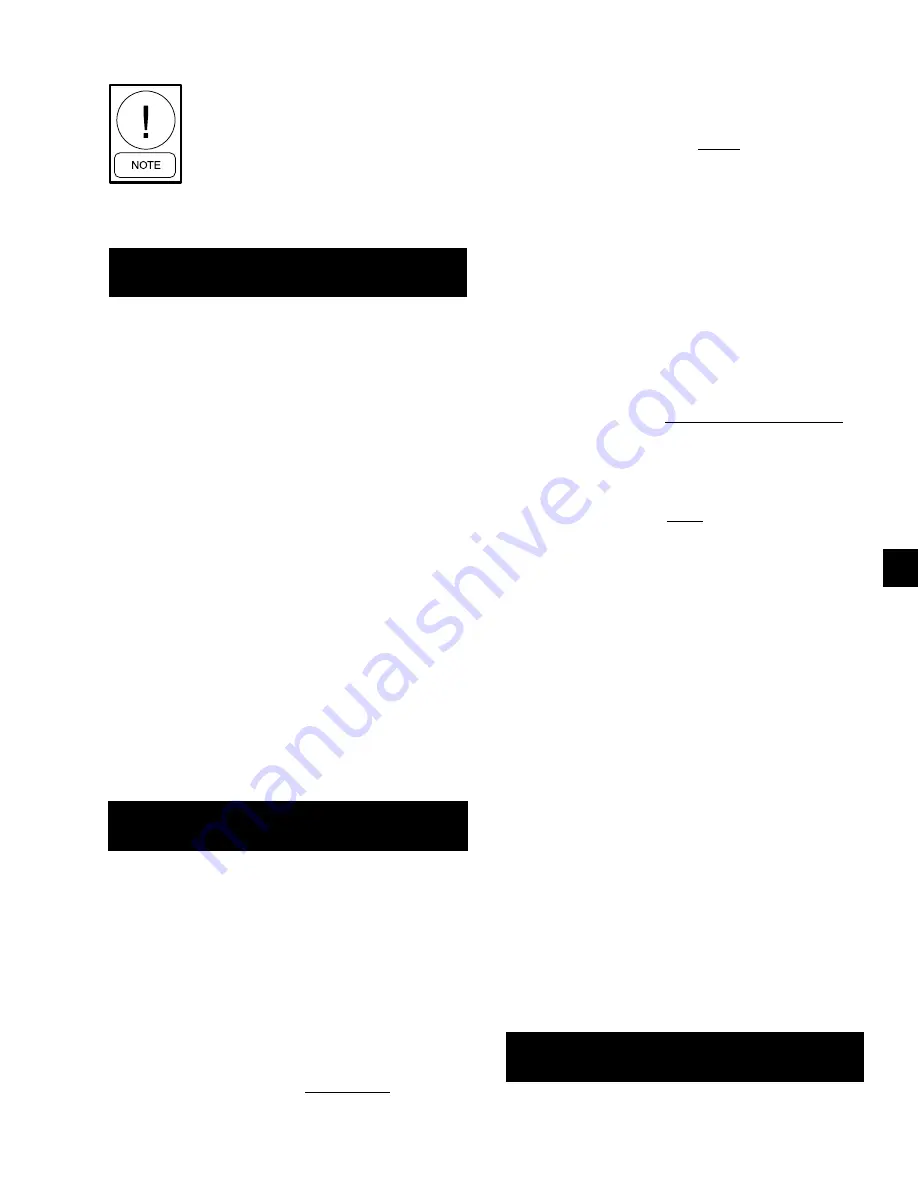
FORM 201.24-NM2
75
YORK INTERNATIONAL
The microprocessor discharge pres-
sure cutout is backed-up by the me-
chanical high pressure cutout located
in each refrigerant circuit.
High Discharge Pressure Unload Point:
The discharge pressure unload point is used to avoid a
high pressure cutout shutdown by unloading a com-
pressor, if its discharge pressure approaches the cutout
value. The chiller can then continue to run automati-
cally at reduced capacity until the cause of the exces-
sive pressure is resolved (e.g. dirty condenser coils) or
cleared (e.g. high ambient temperature).
For the first 60 seconds of operation, discharge pres-
sure limiting is disabled. After this time, if discharge
pressure exceeds the programmed limit, a 1 second
unload pulse will be sent to the slide valve of the af-
fected compressor every 5 seconds until the discharge
pressure drops below the programmed limit.
Reloading will take place when discharge pressure has
dropped 4 bar below the programmed threshold.
Typically the unload point should be set 1.2 to 2 bar
below the discharge pressure cutout setting. The mi-
croprocessor will accept a range of programmable val-
ues between 13.8 and 27.52 bar.
Low Suction Pressure Cutout:
The low suction pressure cutout protects the evapora-
tor from damage due to ice build up caused by opera-
tion at low refrigerant suction pressure.
After the compressor starts, and the pump down cycle
is completed (pump down to cutout or 30 seconds,
whichever comes first), suction pressure is monitored
as long as the compressor runs. For the first 270 sec-
onds of running, suction pressure can be lower than
the programmed cutout, but must be greater than:
PROGRAMMED
X
RUN TIME / 3 +10
CUTOUT
100
For example, if the programmed cutout = 3 bar and
the run time = 60 seconds
This cutout value increases with time, until after 270
seconds, it equals the programmed cutout value. If suc-
tion pressure falls below the calculated cutout value
before 270 seconds, the system will be shutdown.
After 270 seconds, a transient timer system prevents
short term fluctuations in suction pressure from caus-
ing shutdown as follows: If suction pressure drops be-
low the cutout point, a 90 second transient timer starts.
During the 90 second time period, the suction pressure
must be greater than:
This cutout value increases with time, until after 90
seconds, it equals the programmed cutout value. If the
suction pressure rises to more than 0.3 bar above the
programmed cutout value during the 90 second time
period, the timer will be reset.
If the suction pressure does not rise to more than 0.3
bar above the cutout, the timer will remain at zero and
if the pressure then falls below the cutout again, the
system will shutdown on a low pressure fault.
If the Dip Switch (S1) on the AMB board is set for
‘WATER’ cooling mode, the cutout is programmable
between 3.03 and 4.83 bar. In this mode, a setting of
3.03 bar is recommended.
If the Dip Switch (S1) on the AMB board is set for
‘GLYCOL’ (Brine) cooling mode, the cutout is pro-
grammable between 0.34 and 4.83 bar. In this mode,
the cutout should be set to the saturated refrigerant pres-
sure equivalent to 10°C below the temperature of the
chilled liquid.
High Ambient Temperature Cutout:
The high ambient temperature cutout is used to select
the ambient temperature above which the chiller may
D I S C H A R G E
P R E S S U R E
U N L O A D
=
3 6 0 . 0
P S I G
S U C T I O N
P R E S S U R E
C U T O U T
=
3 . 0
B A R G
NEW CUTOUT = 3 x
100 - 60
=
1.2 bar
100
For example, if the programmed cutout = 3 bar and
the timer has run 30 seconds
PROGRAMMED
X
100 - TRANSIENT TIME REMAINING
CUTOUT
100
H I G H
A M B I E N T
T E M P
C U T O U T
=
5 4 . 0 ° C
NEW CUTOUT = 3 x
60/3 + 10
=
0.9 bar
100
7
Summary of Contents for YCWS0313SC
Page 12: ...YORK INTERNATIONAL 12 THIS PAGE INTENTIONALLY LEFT BLANK TO MAINTAIN PAGE FORMAT...
Page 36: ...YORK INTERNATIONAL 36 THIS PAGE INTENTIONALLY LEFT BLANK TO MAINTAIN PAGE FORMAT Commissioning...
Page 86: ...YORK INTERNATIONAL 86 TYPICAL CONTROL PANEL WIRING Maintenance...
Page 87: ...FORM 201 24 NM2 87 YORK INTERNATIONAL TYPICAL CONTROL PANEL WIRING LD06957 8...
Page 103: ...FORM 201 24 NM2 103 YORK INTERNATIONAL NOTES 11...