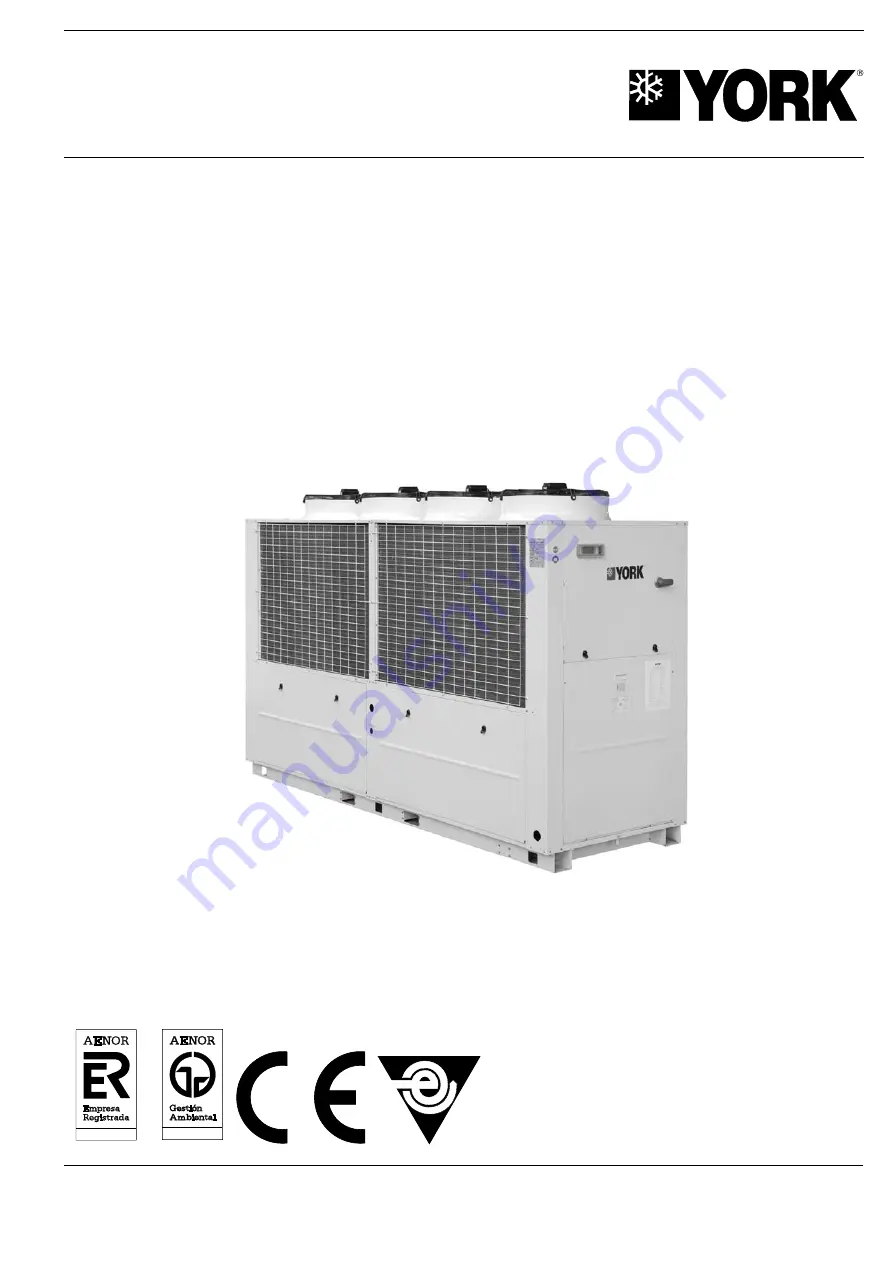
Technical Information
Air-condensed water chillers
and heat pumps
YCSA/YCSA-H 120 and 150 T and TP
(R-410A)
Ref.: Y-R70161 0707
������������
��
�
��
�
�
�
����������
��
�
��
�
�
�
�
E U R O V E N T
CERTIFIED PERFORMANCE
Johnson Controls Manufacturing España, S.L. is participating in the EUROVENT
Certification Program.
Products are as listed in the EUROVENT Directory of Certified Products, in the
program
AC
1, AC2, AC3, LCP and FC.
The LCP program covers air condensed water chillers and heat pumps of up
to 600 kW.
Summary of Contents for YCSA 120 T
Page 2: ......
Page 4: ......
Page 23: ...23 Minimum technical clearance ...
Page 24: ...24 Wiring diagram YCSA YCSA H 120 µC3 400 3 50 ...
Page 26: ...26 Wiring diagram YCSA YCSA H 120 µC3 400 3 50 ...
Page 27: ...27 Wiring diagram YCSA YCSA H 150 µC3 400 3 50 ...
Page 29: ...29 Wiring diagram YCSA YCSA H 150 µC3 400 3 50 ...
Page 30: ...30 Wiring YCSA YCSA H 120 and 150 T TP ...
Page 35: ...35 General wiring diagram ...
Page 48: ...www johnsoncontrols com ...