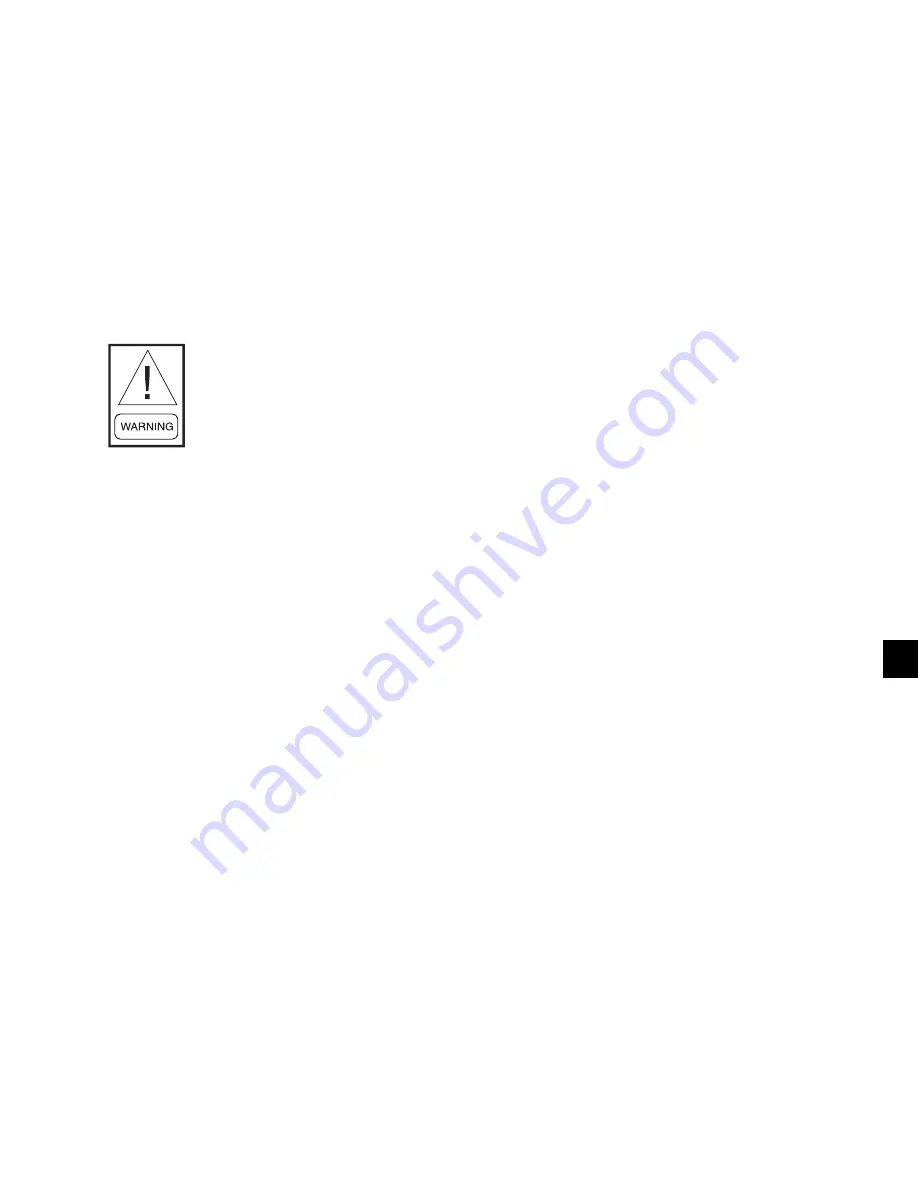
41
YORK INTERNATIONAL
FORM 201.19-NM7 (804)
5
Check that the tapping used conforms to the site sup ply
voltage. After the tapping is verifi ed, replace the lid.
Switch Settings
Ensure that the unit ON/OFF switch on the display door
and the micro board system switch es S2 through S5 are
set to “0” (OFF). Set the red han dled emergency stop
de vice on the options panel to “1” (ON). For units fi tted
with door interlocked circuit breakers the power panel
doors must be closed and the devices set to “1” (ON).
The customer’s power dis con nec tion devices can now
be set to ON.
The machine is now live!
The unit is fi tted with an under voltage circuit in each
pan el and it may take be tween 5 to 10 seconds for its
con tacts to close and energize the unit’s electronics,
in clud ing the dis play on the main panel.
Compressor Heaters
Verify the compressor heaters are en er gized. If
the ambient temperature is above 96°F (36°C) the
com pres sor heaters must be on for at least 8 hours before
start-up to ensure all refrigerant liquid is driven out of
the compressor. If the ambient tem per a ture is be low
86°F (30°C) then allow 24 hours.
Water System
Verify that the chilled liquid system has been installed
correctly, and has been commissioned with the correct
direction of water fl ow through the evaporator. The inlet
should be at the refrigerant pipework connection end of
the evaporator. Purge air from the top of the evaporator
using the plugged air vent mounted on the top of the
evaporator body. Flow rates and pressure drops must be
within the limits given in the Technical Data Section.
Op er a tion outside of these lim its is un de sir able and could
cause damage.
Flow Switch
Verify a chilled water fl ow switch is cor rect ly fi tted in
the customer’s pipework on the evaporator outlet, and
wired into the control panel correctly using shielded
cable. There should be a straight run of at least 5 pipe
di am e ters on either side of the fl ow switch. The fl ow
switch should be connected to terminals 13 and 14 in the
mi cro panel (Figs. 13 and 14, pages 38 and 39).
Temperature Sensor(s)
Ensure the leaving liquid tem per a ture sensor is coated
with heat conductive com pound (part no. 013-00890-
000) and is inserted in the water outlet sensor pocket
of the evaporator. This sensor also acts as the freeze
pro tec tion ther mo stat sensor and must always be in the
water OUTLET sen sor pocket.
Control Supply
Verify the control panel display is illuminated.
Programmed Options
Verify that the options factory programmed into the
Mi cro com put er Control Center are in accordance with
the cus tom er’s order re quire ments by pressing the ‘Op-
tions’ key on the keypad and read ing the settings from
the display.
Programmed Settings
Ensure the system cut-out and operational settings
are in accordance with the in struc tions provided in
Sec tion 8 (page 160) and with the general chiller op-
er a tion al re quire ments by press ing the ‘Pro gram’ key.
The chilled liquid tem per a ture con trol set tings need to
be set ac cord ing to the unit model and required op er -
at ing con di tions.
Date and Time
Program the date and time by fi rst en sur ing that the CLK
jumper J18 on the mi cro pro ces sor board is in the ON
position (top two pins). Then press the ‘Clock Set Time’
key and set the date and time. (See Section 7.)
Start/Stop Schedule
Program the daily and hol i day start/stop by pressing the
‘Set Schedule/Holiday’ key. (See Section 7.)
Setpoint and Remote Offset
Set the required leav ing chilled liquid temperature
set point and control range. If remote temperature reset
(off set) is to be used, the maximum reset must be pro-
grammed by pressing the ‘Remote Reset Temp’ key.
(See Section 6.)
Summary of Contents for YCAS0295EB
Page 43: ...43 YORK INTERNATIONAL FORM 201 19 NM7 804 5 This page intentionally left blank...
Page 45: ...45 YORK INTERNATIONAL FORM 201 19 NM7 804 6 This page intentionally left blank...
Page 59: ...59 YORK INTERNATIONAL FORM 201 19 NM7 804 This page intentionally left blank 7...
Page 71: ...71 YORK INTERNATIONAL FORM 201 19 NM7 804 7 LEGEND LD09241 YCAS0295 YCAS0605...
Page 73: ...73 YORK INTERNATIONAL FORM 201 19 NM7 804 7 CONNECTION DIAGRAM SYSTEM WIRING LD010030...
Page 74: ...74 YORK INTERNATIONAL FORM 201 19 NM7 804 Technical Data COMPRESSOR TERMINAL BOX LD10029...
Page 77: ...77 YORK INTERNATIONAL FORM 201 19 NM7 804 7 This page intentionally left blank...
Page 115: ...115 YORK INTERNATIONAL FORM 201 19 NM7 804 7 This page intentionally left blank...