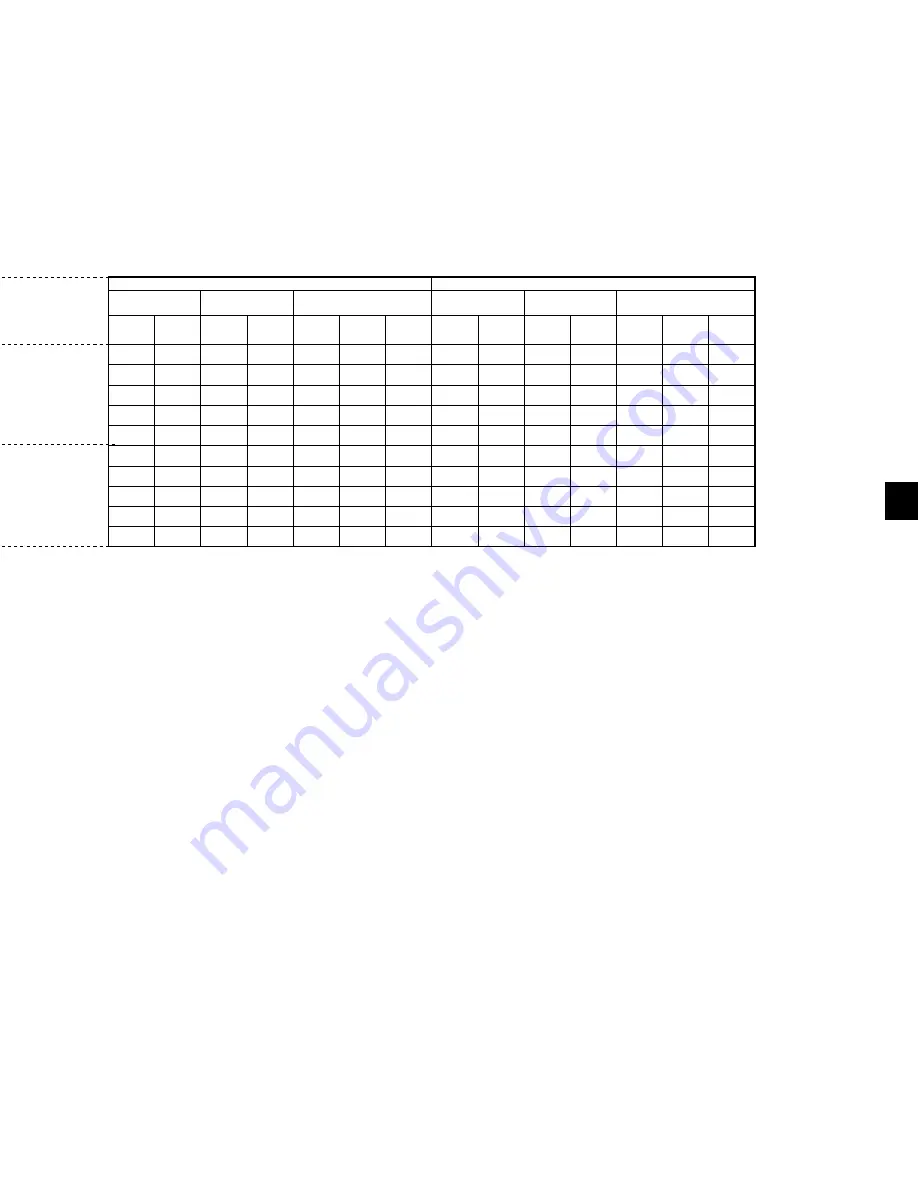
57
JOHNSON CONTROLS
SECTION 5 – TECHNICAL DATA
FORM 150.67-NM1
ISSUE DATE: 4/28/2017
55
SYSTEM #1 COMPRESSOR & FAN
SYSTEM #2 COMPRESSOR & FAN
COMPR. #1
COMPR. #2
FANS
COMPR. #1
COMPR. #2
FANS
RLA
LRA
RLA
LRA
QTY
FLA
RLA
RLA
LRA
RLA
LRA
QTY
FLA
RLA
55.8
425
55.8
425
2
7.6
44.0
55.8
425
55.8
425
2
7.6
44.0
55.8
425
55.8
425
2
7.4
19.1
55.8
425
55.8
425
2
7.4
19.1
36.0
239
36.0
239
2
4.5
23.1
36.0
239
36.0
239
2
4.5
23.1
26.9
187
26.9
187
2
4.0
19.0
26.9
187
26.9
187
2
4.0
19.0
23.7
148
23.7
148
2
2.9
15.3
23.7
148
23.7
148
2
2.9
15.3
76.9
505
76.9
505
2
7.6
30.9
59.9
425
59.9
425
2
7.6
30.9
71.2
505
71.2
505
2
7.4
37.0
55.5
425
55.5
425
2
7.4
37.0
41.1
280
41.1
280
2
4.5
22.3
32.0
239
32.0
239
2
4.5
22.3
33.9
225
33.9
225
2
3.4
17.2
26.4
187
26.4
187
2
3.4
17.2
27.1
180
27.1
180
2
2.9
14.6
21.1
148
21.1
148
2
2.9
14.6
Single-Point Field Supplied Power Wiring (See Figure 12)
(One Field Provided Power Supply to the chiller. Field connections to Factory Provided Power Terminal Block (standard), Non-Fused
Disconnect Switch (optional) or Circuit Breaker (optional)).
ELECTRICAL DATA (ENGLISH) (CONT’D)
YCAL0019_ – YCAL0066_
Summary of Contents for YCAL0019
Page 4: ...JOHNSON CONTROLS 4 FORM 150 67 NM1 ISSUE DATE 4 28 2017 THIS PAGE INTENTIONALLY LEFT BLANK...
Page 14: ...JOHNSON CONTROLS 14 FORM 150 67 NM1 ISSUE DATE 4 28 2017 THIS PAGE INTENTIONALLY LEFT BLANK...
Page 69: ...69 JOHNSON CONTROLS SECTION 5 TECHNICAL DATA FORM 150 67 NM1 ISSUE DATE 4 28 2017 5 5...
Page 71: ...71 JOHNSON CONTROLS SECTION 5 TECHNICAL DATA FORM 150 67 NM1 ISSUE DATE 4 28 2017 5 5...
Page 229: ...229 JOHNSON CONTROLS SECTION 10 MAINTENANCE FORM 150 67 NM1 ISSUE DATE 4 28 2017 NOTES...