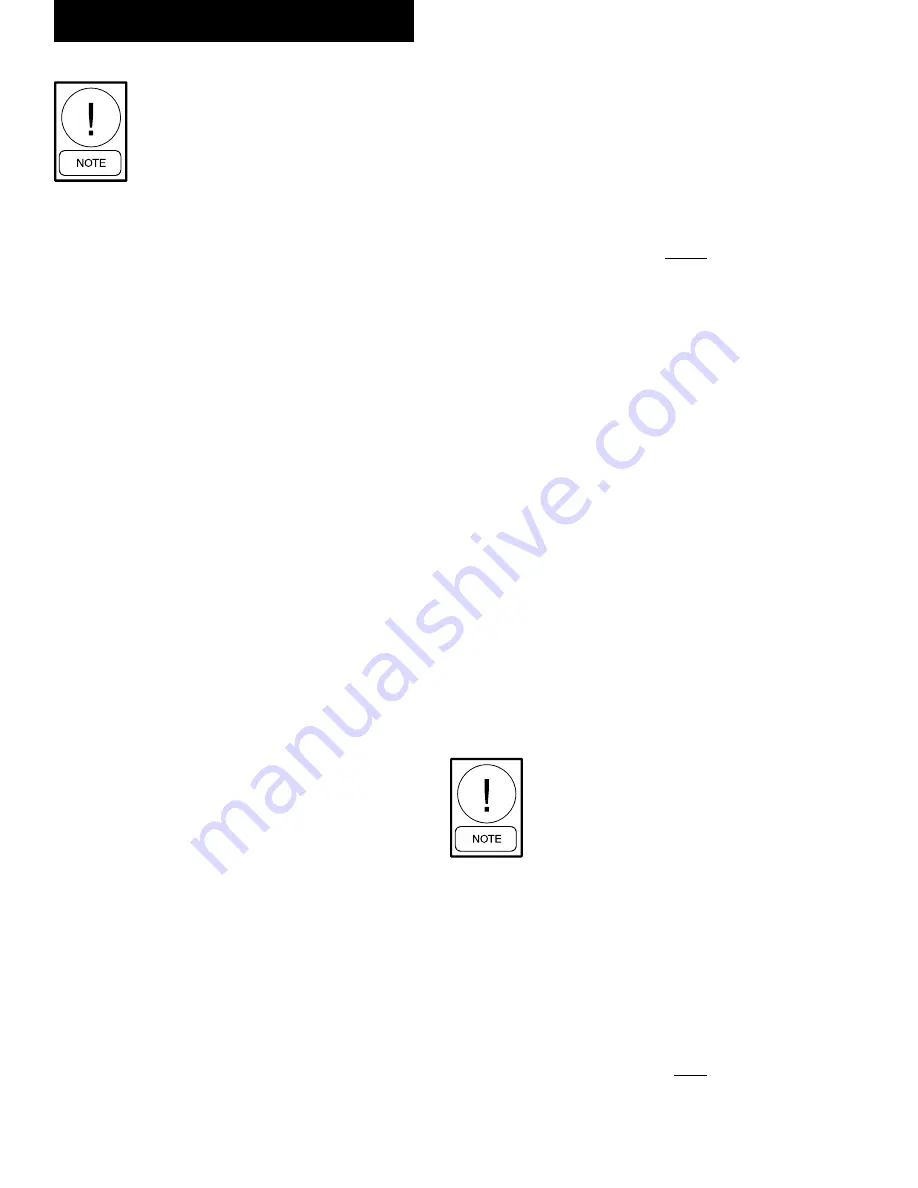
JOHNSON CONTROLS
78
FORM 150.62-NM8 (1020)
INSTALLATION
The subcooling temperature of each system can be
calculated by recording the temperature of the liquid line
at the outlet of the condenser and subtracting it from the
liquid line saturation temperature at the liquid stop valve
(liquid line saturation temperature is converted from a
temperature/pressure chart).
Example:
Liquid line pressure = 102°F
202
psig converted to - 87°F
minus liquid line temp.
Subcooling = 15°F
The subcooling should be adjusted to 15°F (-9.4°C) at
design conditions.
1. Record the liquid line pressure and its
corresponding temperature, liquid line temperature
and subcooling below:
SYS 1 SYS 2
Liq Line Press = _______ _______ psig
Saturated Temp = _______ _______ °F
Liq Line Temp = _______ _______ °F
Subcooling = _______ _______ °F
After the subcooling is verified, the suction superheat
should be checked. The superheat should be checked
only after steady state operation of the chiller has been
established, the leaving water temperature has been pulled
down to the required leaving water temperature, and the
unit is running in a fully loaded condition. Correct superheat
setting for a system is 10°F minus 15°F (5.56°C minus
8.33°C) 18" (46 cm) from the cooler.
Superheat should typically be set for
no less than 10°F (-12.2°C) with only
a single compressor running on a
circuit.
The superheat is calculated as the difference between the
actual temperature of the returned refrigerant gas in the
suction line entering the compressor and the temperature
corresponding to the suction pressure as shown in a
standard pressure/temperature chart.
Example:
Suction Temp =
46°F
minus Suction Press
60
psig converted to Temp - 34°F
Superheat = 12°F
The chilled liquid setpoint may need
to be temporarily lowered to ensure all
compressors cycle ON.
7. After verifying compressor rotation, return the
Unit Switch to the OFF position and ensure that
both systems are programmed for
ON
(refer to
Option 2 under Unit Key in Section 2 of this IOM
for more information on system switches).
Initial Startup
After the preceding checks have been completed and the
control panel has been programmed as required in the
Equipment Pre-startup and, the chiller may be placed
into operation.
1. Place the Unit Switch in the control panel to the
ON position.
2. The first compressor will start and a flow of
refrigerant will be noted in the sight glass. After
several minutes of operation, the vapor in the
sight glass will clear and there should be a solid
column of liquid when the TXV stabilizes.
3. Allow the compressor to run a short time, being
ready to stop it immediately if any unusual noise
or adverse conditions develop.
4. Check the system operating parameters. Do this
by selecting various displays such as pressures
and temperatures and comparing these readings to
pressures and temperatures taken with manifold
gauges and temperature sensors.
5. With an ammeter, verify that each phase of the
condenser fans and compressors are within the
RLA as listed under Electrical Data.
Checking Superheat and Subcooling
The subcooling and superheat should always be checked
when charging the system with refrigerant.
When the refrigerant charge is correct, there will be no
vapor in the liquid sight glass with the system operating
under full load conditions, and there will be 15°F
(8.34°C) subcooled liquid leaving the condenser.
An overcharged system should be guarded against. The
temperature of the liquid refrigerant out of the condenser
should be no more than 18°F (10°C) subcooled at design
conditions.
Summary of Contents for YCAL0014E Series
Page 4: ...JOHNSON CONTROLS 4 FORM 150 62 NM8 1020 THIS PAGE INTENTIONALLY LEFT BLANK ...
Page 10: ...JOHNSON CONTROLS 10 FORM 150 62 NM8 1020 THIS PAGE INTENTIONALLY LEFT BLANK ...
Page 18: ...JOHNSON CONTROLS 18 FORM 150 62 NM8 1020 THIS PAGE INTENTIONALLY LEFT BLANK ...
Page 31: ...JOHNSON CONTROLS 31 FORM 150 62 NM8 1020 THIS PAGE INTENTIONALLY LEFT BLANK ...
Page 126: ...JOHNSON CONTROLS 126 FORM 150 62 NM8 1020 THIS PAGE INTENTIONALLY LEFT BLANK ...
Page 140: ...JOHNSON CONTROLS 140 FORM 150 62 NM8 1020 THIS PAGE INTENTIONALLY LEFT BLANK ...
Page 155: ...JOHNSON CONTROLS 155 FORM 150 62 NM8 1020 5 6 ...
Page 157: ...JOHNSON CONTROLS 157 FORM 150 62 NM8 1020 5 6 LD08855 ...
Page 161: ...JOHNSON CONTROLS 161 FORM 150 62 NM8 1020 161 5 6 ...
Page 163: ...JOHNSON CONTROLS 163 FORM 150 62 NM8 1020 5 6 ...
Page 167: ...JOHNSON CONTROLS 167 FORM 150 62 NM8 1020 5 6 ...
Page 169: ...JOHNSON CONTROLS 169 FORM 150 62 NM8 1020 5 6 ...
Page 171: ...JOHNSON CONTROLS 171 FORM 150 62 NM8 1020 5 6 ...
Page 173: ...JOHNSON CONTROLS 173 FORM 150 62 NM8 1020 5 6 ...
Page 175: ...JOHNSON CONTROLS 175 FORM 150 62 NM8 1020 5 6 ...
Page 177: ...JOHNSON CONTROLS 177 FORM 150 62 NM8 1020 5 6 ...
Page 181: ...JOHNSON CONTROLS 181 FORM 150 62 NM8 1020 5 6 ...
Page 183: ...JOHNSON CONTROLS 183 FORM 150 62 NM8 1020 5 6 LD08833 ...
Page 185: ...JOHNSON CONTROLS 185 FORM 150 62 NM8 1020 5 6 ...
Page 187: ...JOHNSON CONTROLS 187 FORM 150 62 NM8 1020 5 6 ...
Page 189: ...JOHNSON CONTROLS 189 FORM 150 62 NM8 1020 5 6 ...
Page 191: ...JOHNSON CONTROLS 191 FORM 150 62 NM8 1020 5 6 ...
Page 195: ...JOHNSON CONTROLS 195 FORM 150 62 NM8 1020 5 6 ...
Page 197: ...JOHNSON CONTROLS 197 FORM 150 62 NM8 1020 5 6 ...
Page 199: ...JOHNSON CONTROLS 199 FORM 150 62 NM8 1020 5 6 ...
Page 200: ...JOHNSON CONTROLS 200 FORM 150 62 NM8 1020 THIS PAGE INTENTIONALLY LEFT BLANK ...
Page 211: ...JOHNSON CONTROLS 211 FORM 150 62 NM8 1020 THIS PAGE INTENTIONALLY LEFT BLANK ...