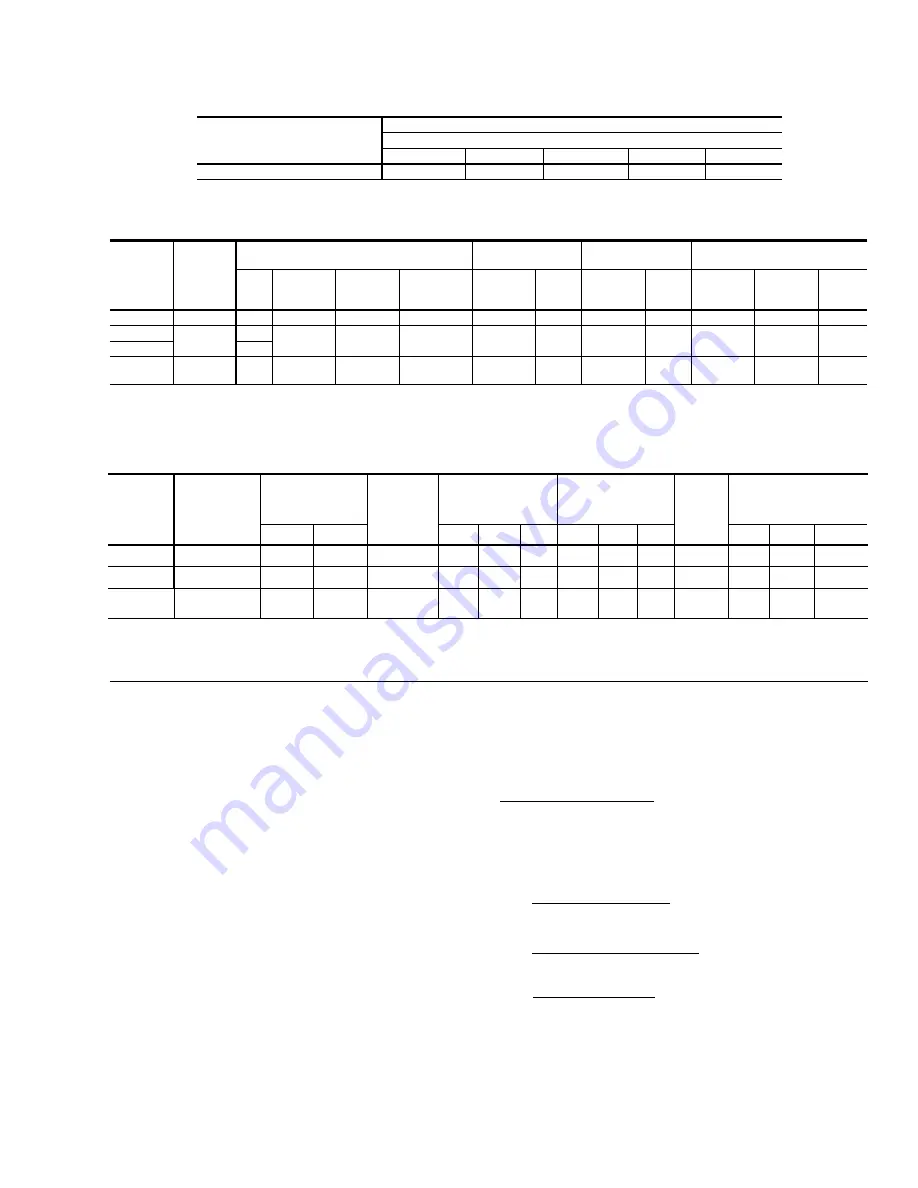
COOLING SYSTEM
The cooling section is a complete factory package utilizing an
air-cooled condenser. The system is factory-charged with
Refrigerant-22. The compressors are hermetically sealed and
internally sprung and base mounted on spring isolators.
The compressors also have inherent (internal) protection. If
there is an abnormal temperature rise in a compressor, the
protector will open to shut down the compressor.
PRELIMINARY OPERATION COOLING
After installation has been completed, energize the crankcase
heaters for at least four hours before operating unit. After this
initial warm-up, the compressors should be given three false
starts (energized just long enough to make a few revolutions)
with 5-7 minutes delay between each start before being put into
full time service. (Not applicable on 10 ton units.)
NOTE: Prior to each cooling season, the crankcase heaters
must be energized at least 10 hours before system is
put into operation.
COOLING SEQUENCE OF OPERATION
When the thermostat calls for “first-stage” cooling, the low
voltage control circuit from “R” to “G” and “Y1" (wiring
schematic) is completed to energize compressor #1,
condenser fan motor #1 and blower motor simultaneously.
When the thermostat calls for “2nd-stage” cooling, the low
voltage control circuit from “R” to “Y2" is completed to energize
compressor #2 and condenser fan motor #2.
After the thermostat is satisfied and opens, all components
likewise stop simultaneously.
CONTINUOUS BLOWER - Continuous blower operation is
possible by closing the R to G circuit on the thermostat.
SAFETY CONTROLS
Each refrigerant system is equipped with the following safety
controls:
1. A Suction Line Freezestat to protect against low evaporator
temperatures due to a low air flow or a low return air
temperature.
2. A High Pressure Cutout Switch to protect against excessive
discharge pressures due to a blocked condenser coil or a
condenser motor failure.
3. A Low Pressure Switch to protect against loss of refrigerant
charge.
If either one of the above safety controls opens, that individual
refrigerant system will be locked out. The other refrigerant
system will continue in operation unless it too is effected by the
same fault. The lock out of either system can be reset by
opening the 24V circuit either at the room thermostat or at the
unit disconnect.
OPERATION
TABLE 6 - ACCESSORY STATIC RESISTANCES*
DESCRIPTION
EXTERNAL STATIC PRESSURE DROP - RESISTANCE, IWG
CFM
2250
3000
4000
5000
6000
Economizer/Motorized Damper
0.02
0.02
0.03
0.05
0.07
*Deduct these resistance values from the available external static pressure shown in the respective Blower Performance Table.
MODELS
BLOWER
RANGE
(RPM)
MOTOR*
ADJUSTABLE
MOTOR PULLEY
FIXED
BLOWER PULLEY
BELTS
HP
SERVICE
FACTOR
FRAME
SIZE
EFFICIENCY
(%)
PITCH
DIA.
(IN.)
BORE
(IN.)
PITCH
DIA.
(IN.)
BORE
(IN.)
PITCH
LENGTH
(IN.)
DESIG-
NATION
QTY
DEG090
975-1220
2
1.20
56
82.0
3.4 - 4.4
7/8
6.2
1
50.3
A49
1
DEG120
860-1090
2, 3
1.20
56
82.0
3.4 - 4.4
7/8
7.0
1
57.3
A56
1
DEG150
3
DEG150
960-1140
5
1.15
184
82.0
4.9 - 5.9
1-1/8
8.9
1
62.8
BX61
(Notched)
1
*
All motors are 1750 RPM, have solid bases and are inherently protected. These motors can be selected to operate into their service factor because they are located in the moving air,
upstream of any heating device.
TABLE 7 - BLOWER MOTOR AND DRIVE DATA
MODEL
DEG
POWER
SUPPLY
COMPRESSOR
(#1 and #2)
OUTDOOR
FAN
MOTOR,
(#1 & #2)
FLA
EACH
SUPPLY
AIR
BLOWER
MOTOR,
FLA
TOTAL
UNIT
AMPACITY,
AMPS
MAX.
FUSE
SIZE,
1
AMPS
MIN.
WIRE
SIZE,2
AWG
RLA
EACH
LRA
EACH
2HP
3HP
5 HP
2HP
3HP
5 HP
2HP
3HP
5 HP
090
208/230-3-60
460-3-60
14.1
7.1
130
64
2.3
1.3
7.5
3.4
-
-
-
-
43.8
21.9
-
-
-
-
50
25
8
10
-
-
-
-
120
208/230-3-60
460-3-60
19.5
10.0
123
62
2.3
1.3
7.5
3.4
10.6
4.8
-
-
56.0
28.5
59.1
29.9
-
-
70
35
6
8
6
8
-
-
150
208/230-3-60
460-3-60
575-3-60
20.7
10.0
8.2
156
70
54
3.5
2.5
2.5
-
-
-
10.6
4.8
3.9
15.1
7.5
5.9
-
-
-
64.2
32.3
27.4
68.7
35.0
29.4
80
40/45
35
-
-
-
6
8
8
4
8
8
NOTES:
1. Dual element, time delay type. Amps shown as "40/45" indicates rating for
LO HP/HI HP, respectively. Maximum HACR breaker of the same AMP size is applicable.
2. Based on 75
°
C copper conductors.
TABLE 8 - ELECTRICAL DATA
530.22-N4Y
Unitary Products Group
11