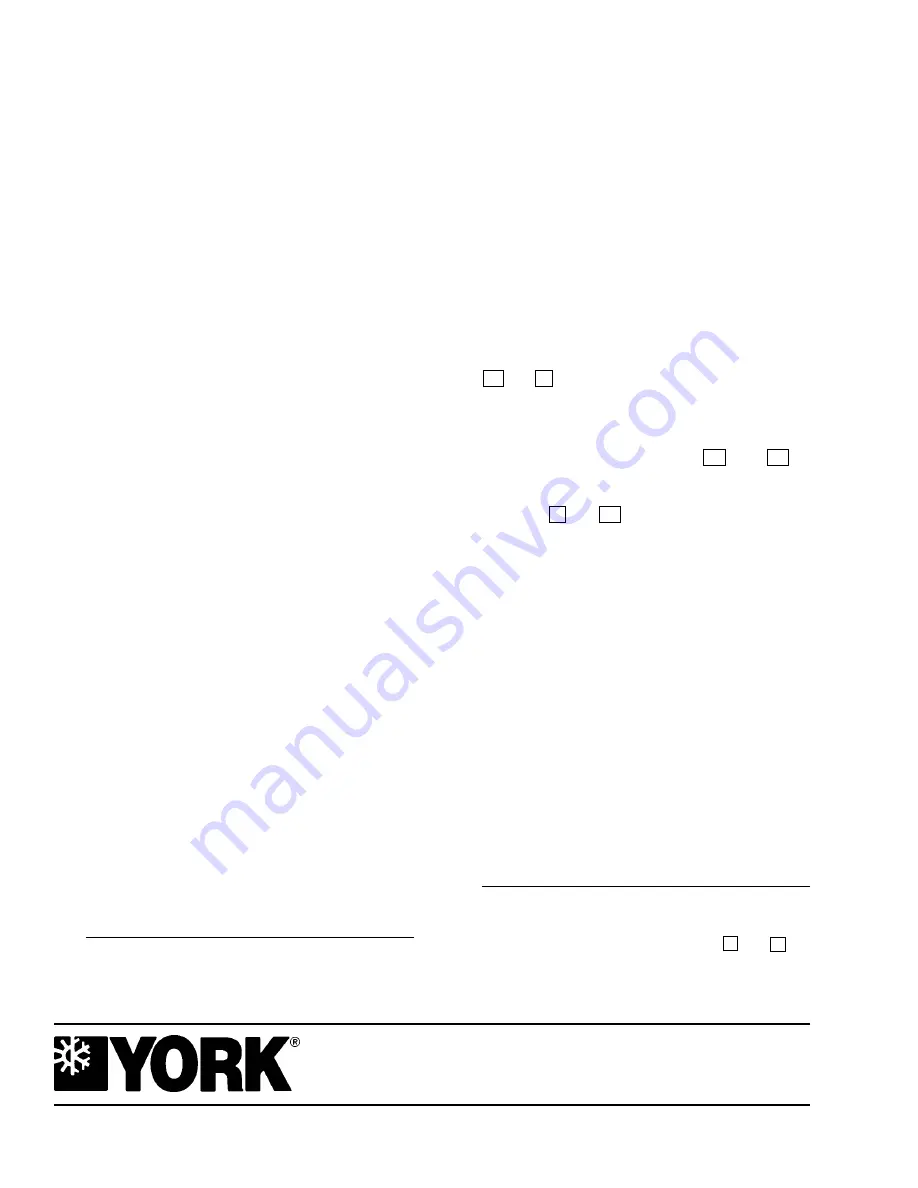
P.O. Box 1592, York, Pennsylvania USA 17405-1592
Subject to change without notice. Printed in USA
Copyright © by York International Corporation 2001
ALL RIGHTS RESERVED
Form 160.54-PW7 (401)
Supersedes: 160.54-PW7 (799)
Tele. 800-861-1001
www.york.com
10. Lead selector and cycling control to provide similar
lead selection and cycling of lag units for three (3)
units is available: Kit No. 366-44684D (see Product
Drawing Form 160.00-PA1.1) in NEMA I enclosure.
Consult your YORK representative.
11. Sequence control kits (see Fig.9 and Note 10) as-
sume a constant chilled water flow and a constant
leaving chilled water temperature to sense the cool-
ing load. Sequence control kits are not designed for
variable chilled water flow or with reset of the leav-
ing chilled water temperature – see Figs. 18 to 20
and Note 2.
12. Maximum allowable current draw between circuits
24 and 2 for field installed devices is 2 amp hold-
ing and 10 amps inrush – see OptiView Control Cen-
ter Wiring Diagram Form No. in Note 1.
13. For required field wiring connections of the chilled
water pump contacts (terminals 44 and 45 on
OptiView Control Center field wiring terminal block
TB2) and chilled water flow switch
(terminals 1 and 12 on OptiView Control Center
field wiring terminal board TB2), see Wiring Dia-
gram – Field Connections: For those chillers that are
not equipped with “P” code compressors, refer to the
following Product Drawings: 160.54-PW4 (Electro-
Mechanical Starter), 160.54-PW5 (YORK Solid State
Starter), 160.54-PW6 (YORK Variable Speed Drive).
For those chillers equipped with “P” code compres-
sors, refer to the following Product Drawings; 160.54-
PW11 (Electro-Mechanical Starter), 160.54-PW12
(YORK Solid State Starter), 160.54-PW13 (YORK
Variable Speed Drive).
The chilled water flow switch is a safety control. It
must be connected to prevent operation of the chiller
whenever chilled water flow is stopped. The use of
the chilled water flow switch for purposes other than
protection of the chiller may be accomplished in sev-
eral ways. Two flow switches, a flow switch and a
relay or separate contacts on the same flow switch.
14.
15. Do not apply voltage on field wiring terminal blocks
TB4 and TB6 in YORK OptiView Control Center, as
115VAC source is fed from terminals 1 and 2 .
1. This drawing shows recommended field control wir-
ing modifications (by others) to the standard OptiView
Control Center Wiring Diagram. For those chillers that
are not equipped with “P” code compressors, refer to
the following Product Drawings: 160.54-PW4 (Electro-
Mechanical Starter), 160.54-PW5 (YORK Solid State
Starter), 160.54-PW6 (YORK Variable Speed Drive).
For those chillers equipped with “P” code compres-
sors, refer to the following Product Drawings; 160.54-
PW11 (Electro-Mechanical Starter), 160.54-PW12
(YORK Solid State Starter), 160.54-PW13 (YORK
Variable Speed Drive).
2. If more than one of these modifications is to be uti-
lized with a particular unit, additional consideration
must be given to the application to insure proper
functioning of the control system. Consult your
YORK representative.
3. The additional controls and wiring for these modifi-
cations are to be furnished and installed in the field
(by others). (See Warning on page 2.)
4. The controls specified are recommended for use, but
other controls of equal specifications are acceptable.
5. All wiring shall be in accordance with the National
Electrical Code, and applicable State and Local
Codes.
6. Each 115VAC field connected inductive load, i.e. re-
lay coil, motor starter coil, etc., shall have a tran-
sient suppressor wired (by others) in parallel with
its coil, physically located at the coil. Spare transient
suppressors are furnished in a bag in the OptiView
Control Center.
7. The OptiView Control Center is factory furnished
for Manual Restart After Power Failure as a stan-
dard function. The control center can be field changed
from Manual restart to Auto Restart after a power
failure by setting position 5 of Dip Switch SW1 to
the ON position - See Fig. 21.
8. Two (2) unit controls schemes are suitable for 8° –
12°F water range. Constant chilled water flow is
assumed at all loads. For other requirements contact
your YORK representative.
9.
NOTES