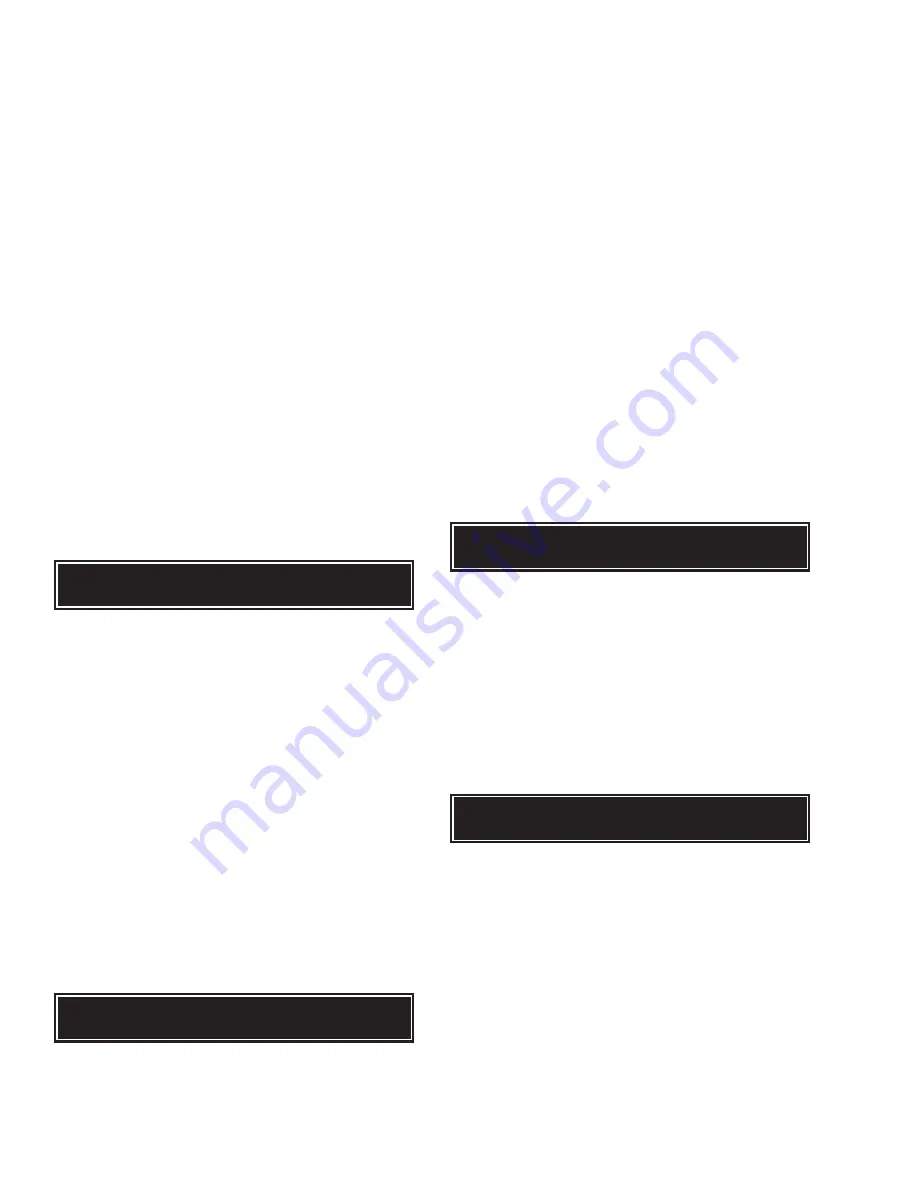
YORK INTERNATIONAL
106
In order to display compressor current draw in amps
the micro needs to be programmed with the compres-
sor motor FLA at 100% load at design conditions for
each compressor on the chiller. This also allows the
micro to calculate approximate compressor slide valve
position which is important when controlling load shar-
ing between compressors based on % Slide Valve in-
stead of % FLA. The System # Motor Current at 100%
FLA value is password protected.
The FLA value at the specified conditions varies with
compressor model and supply voltage. These values
are given for each system on each chiller model for
each supply voltage in the tables in Section 8.4.
To program the System # Motor Current at 100% FLA,
begin with System 1 (the # on the sample display will
read 1) and key in the value given in the table, then
press the Enter key to store the value into memory and
scroll the display on to the next system. Now key in the
value given in the table for System 2, then repeat for
System 3 and System 4 where appropriate. After all
systems have been programmed the display will scroll
to the next programmable control setting.
Liquid Injection Temperature Limit
The Liquid Injection Temperature Limit setting is the
compressor discharge gas temperature above which
the liquid injection solenoid is energized to allow liquid
injection into the compressor to limit discharge gas tem-
perature and hence oil system temperature. This is used
to maintain the oil within the correct temperature range
to provide proper lubrication and cooling of the com-
pressor mechanical parts.
Once liquid injection is activated, discharge tempera-
ture must fall 20°F below the temperature limit before
injection is deactivated. A setting of 180°F is recom-
mended for this control for most applications. This pro-
grammable value is password protected.
To program the Liquid Injection Temperature Limit, key
in the required setting and press the Enter key to store
the value into memory and scroll to the next display.
Condensing Temperature Full Load Setting
If load equalization utilizing % Slide Valve is selected
(See Load Sharing Basis later in this section), the mi-
cro must be programmed with the design condensing
temperature (discharge pressure converted to tempera-
ture or CTP) at 100% load at design conditions for each
system on the chiller. This also allows the micro to cal-
culate approximate compressor slide valve position
which is important when controlling load sharing be-
tween compressors. The System # Condensing Tem-
perature at 100% Load valve is password protected.
The allowable range of Condensing Temperature at
100% Load is 100 - 140°F with the default set for 125°F.
The value which must be programmed varies with chiller
and compressor model. Values for each system on each
chiller model are given in the tables in Section 8.5.
To program the System # Condensing Temperature at
100% Load, begin with system 1 (the # on the sample
display will read 1) and key in the value given in the
table, then press the Enter key to store the value into
memory and scroll the display on to the next system.
Now key in the value given in the table for System 2,
then repeat for System 3 and System 4 where appropri-
ate. After all systems have been programmed, the dis-
play will scroll to the next programmable control setting.
Communications Mode
If an ISN system or an optional Remote Control Center
(RCC) is connected to the chiller, the Communications
Mode value is used to select the correct type of com-
munication protocol required.
To program the Communications Mode, key in the num-
ber corresponding to the connected device (1=ISN,
2=RCC), then press the Enter key to store the value
into memory and scroll to the next display.
Load Sharing Basis
Equalized loading / unloading of compressors to give
the maximum chiller efficiency is based on the calcu-
lated loading of each running compressor. This calcu-
lation can in turn be based on either the estimated com-
pressor slide valve position, or the % of full load cur-
rent being drawn by the compressor motor. The Load
Share Based On ? value determines which basis is
used by the micro for its calculations.
The % FLA method is suitable for most applications
and is the default setting for this control. Where signifi-
cant running in low ambient temperature conditions is
expected, however, more accurate load equalization
will be achieved using the % Slide Valve method which
includes discharge pressure in the calculation.
L I Q U I D
I N J E C T I O N
T E M P
L I M I T
=
1 8 0 . 0 ° F
S Y S T E M
#
C O N D
T E M P
1 1 9 . 0
° F
=
1 0 0 %
L O A D
C O M M U N I C A T I O N S
M O D E
1
=
I S N ,
2
=
R C C ,
2
L O A D
S H A R E
B A S E D
O N ?
1
=
S V % ,
2
=
% F L A
2
Summary of Contents for Millennium YCAS 310
Page 11: ...FORM 201 10 NM3 11 YORK INTERNATIONAL YCAS 310 380 DIMENSIONS English Units LD01594 LD01593...
Page 13: ...FORM 201 10 NM3 13 YORK INTERNATIONAL YCAS 310 380 DIMENSIONS SI Units LD01598 LD01597...
Page 21: ...FORM 201 10 NM3 21 YORK INTERNATIONAL 28514A FILTER DRYER LIQUID STOP VALVE...
Page 36: ...YORK INTERNATIONAL 36 YCAS 310 380 SYSTEMS 1 AND 2 CONNECTION DIAGRAM WYE DELTA START LD02032...
Page 37: ...FORM 201 10 NM3 37 YORK INTERNATIONAL LD02033...
Page 42: ...YORK INTERNATIONAL 42 YCAS 310 380 SYSTEM 3 CONNECTION DIAGRAM WYE DELTA START LD02038...
Page 43: ...FORM 201 10 NM3 43 YORK INTERNATIONAL LD02039...
Page 48: ...YORK INTERNATIONAL 48 LD02021...
Page 54: ...YORK INTERNATIONAL 54 LD02027...