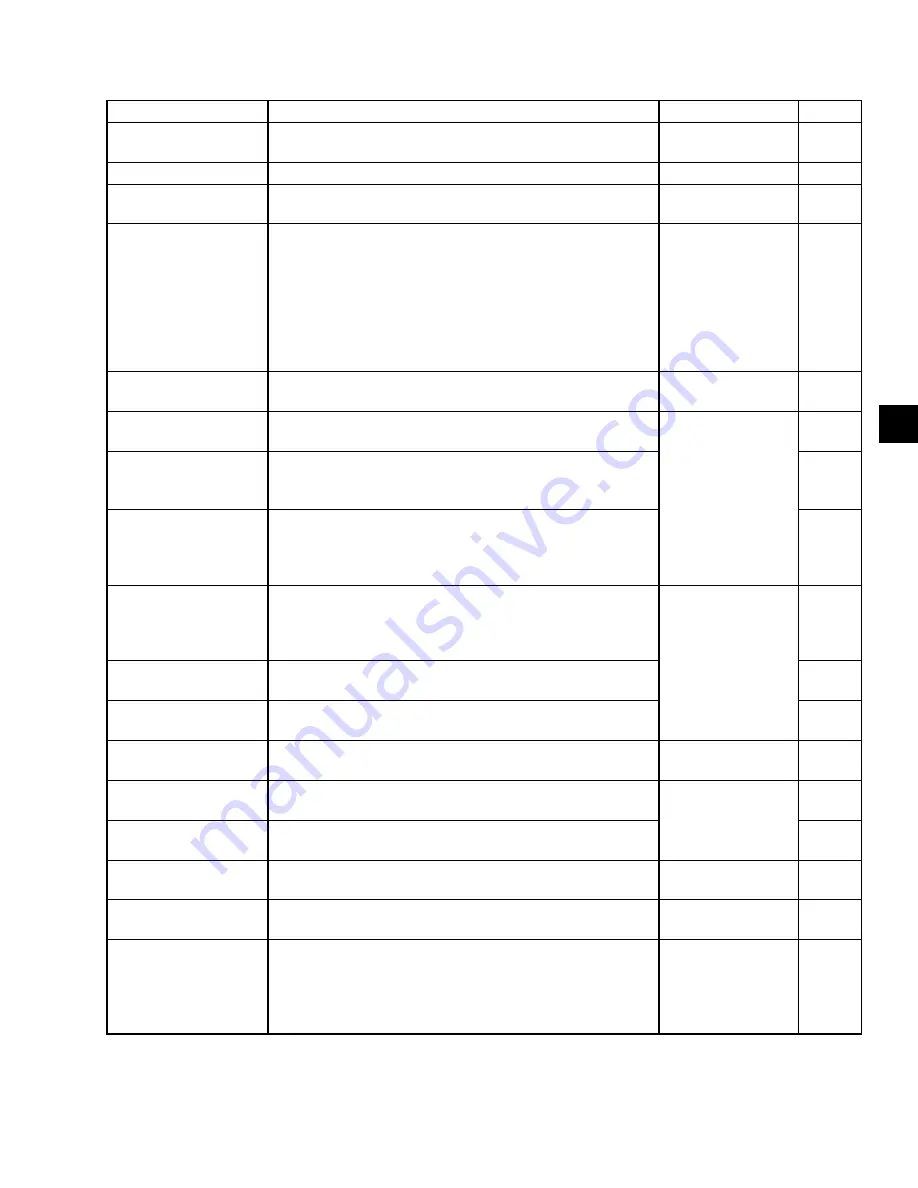
JOHNSON CONTROLS
145
SECTION 7 – MAINTENANCE
FORM 155.32-ICOM1.EN.GB
ISSUE DATE: 10/13/2017
7
TABLE 36 -
MAINTENANCE AND INSPECTION
TASK
CONTENTS
FREQUENCY
SCOPE
Recording of operation
data
Collect the operation data (Refer to
155.31-CL1
) and check the
data with the data collected during the factory test.
Weekly
C
Check of liquid level
. Check the liquid level at each part.
Daily
C
Refining of refrigerant
See
Refrigerant Refining Method
on
refrigerant.
every 2-3 weeks
S
Manual purging from
purging tank
See
Purging Procedure
on
. Manually purge non-
condensable gas from the purging tank.
Since, the machine
has an automatic
purge system,
perform it once at
beginning of the
seasons every year
and once per every
2-3 months.
S
Manual purging from
absorber
See
Purging Procedure
on
. Manually purge non-
condensable gas from the absorber.
every 2-3 months
S
Replacement of oil in
vacuum pump
Replace the oil in the vacuum pump periodically.
monthly
C
Check of Vacuum Pump
After the replacement of the lubricant oil for the vacuum pump,
be sure to pull the pulley belt and check the smooth motion of
the pulley.
C
Appearance check
Check the outside of the unit for damage (e.g., leakage for
chilled/hot water and cooling water, rusting, etc.). Check the
solution pump and refrigerant pump for abnormal sounds and
vibration.
C
Measurement of
insulation resistance of
electric devices
Measure the insulation resistance of the main circuit and motors
(solution pump, refrigerant pump) mainly to check for lowering
of insulation. When measuring the insulation resistance, be sure
to disconnect the wires of the temperature controller, etc.
yearly
S
Check of terminals for
looseness
Check each terminal in the control panel for looseness.
S
Check of operation of
control panel
Check the operation of the control panel to prevent troubles
caused by malfunction of the control panel.
S
Check of capacity of
purge unit
See
Purging Procedure
on
. Check the capacity of
the purge unit periodically.
monthly
S
Check of leakage through
purge solenoid valves
By measuring vacuum down speed, check for leakage through
purge solenoid valves.
yearly
S
Overhaul check of purge
solenoid valves
Perform overhaul of purge solenoid valves periodically.
S
Check of airtightness
Measure the quantity of non-condensable gas discharged from
the vacuum pump.
every 2-3 months
S
Check continuity of
protective bonding circuit
Check continuity of protective bonding circuit
yearly
S
Analysis of quality of
chilled/hot water, and
cooling water
Reliable water treatment companies are available in most
larger cities to supply a water treating process which will greatly
reduce the corrosive and scale forming properties of almost any
type of water. Be sure to request the first analysis within one
month after the test operation is started.
every 2-3 months
C
C = Customer, S = Johnson Controls Service