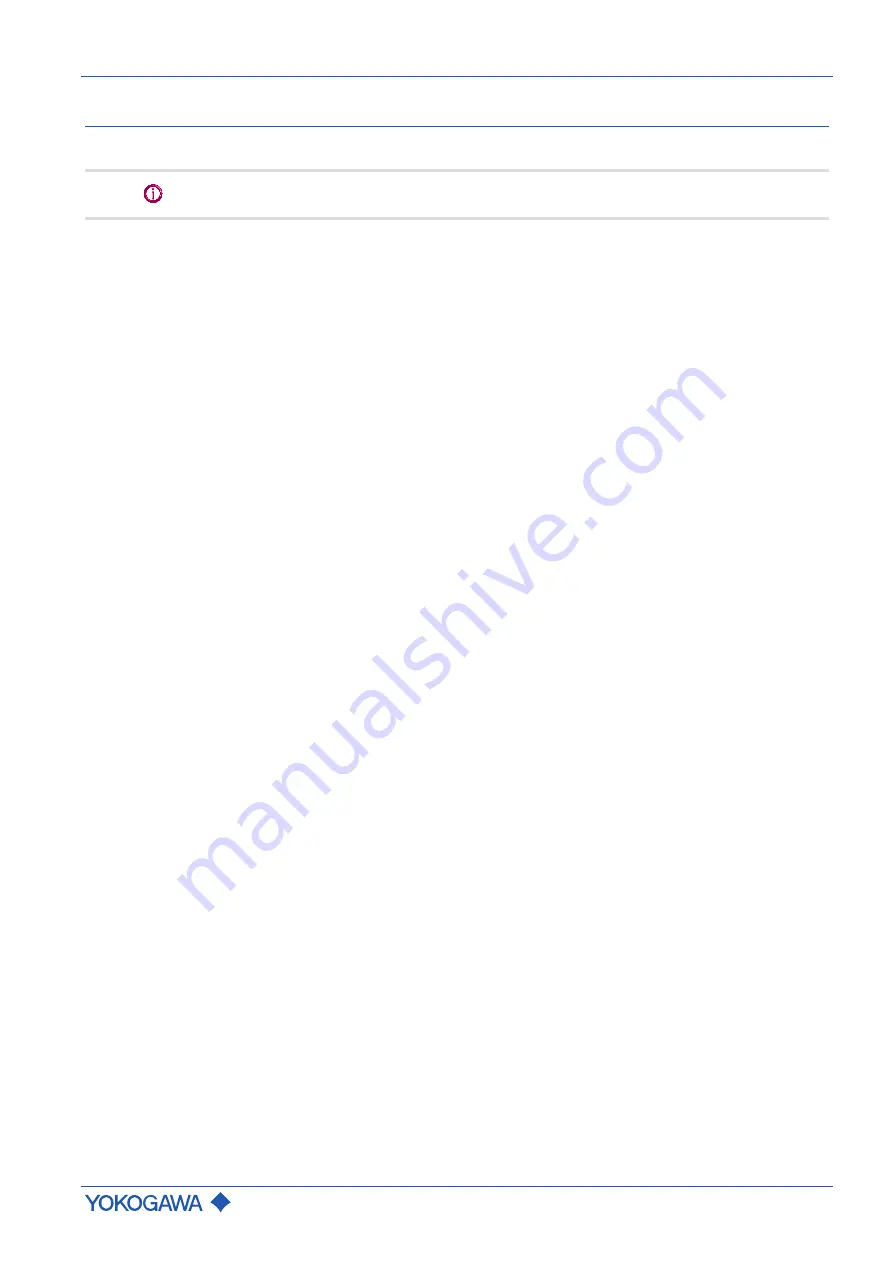
Quick Reference Instruction Manual for Spare
Warranty
IM01U10A01-00EN-R, 1
st
edition, 2019-12-09
9 / 76
3 Warranty
Please contact the Yokogawa sales organization if the device needs to be repaired.
The warranty terms for this device are described in the quotation.
If a defect for which Yokogawa is responsible occurs in the device during the warranty
period, Yokogawa will repair that defect at its own cost.
If you believe that the device is defective, please contact us and provide a detailed de-
scription of the problem. Please also tell us how long the defect has already occurred and
list the model code and serial number. Additional information, such as drawings, simpli-
fies the identification of the cause and repair of the defect.
Based on our test results, we determine whether the device can be repaired at
Yokogawa’s expense or at the expense of the customer. If, for example, the Yokogawa
calibration device for the water flow rate confirms a deviation of the output signal from the
stated flow rate accuracy of the device, the device is deemed defective.
The warranty does not apply in the following cases:
▪ If the adhesion, blockage, deposit, abrasion or corrosion is the result of the device’s
actual use.
▪ If the device is mechanically damaged through solids in the fluid, hydraulic shock, or
similar influences.
▪ If the instructions in the corresponding General Specifications or User's Manual that
must be met have not been followed.
▪ In case of problems, errors or damage that result from unprofessional installation by
the customer, for example due to insufficient tightness of the pipe fittings.
▪ In case of problems, errors or damage that result from operation, handling or storage
in rough ambient conditions that are beyond the specifications of the device.
▪ In case of problems, errors or damage that result from unprofessional or insufficient
maintenance by the customer, for example, if water or foreign particles enter the de-
vice due to opening the device cover.
▪ In case of problems, errors or damage that result from use or from performing mainte-
nance work on the device in a location other than the installation location specified by
Yokogawa.
▪ In case of problems, errors or damage that result from modification or repair work that
was not performed by Yokogawa or by a person authorized by Yokogawa.
▪ In case of problems, errors or damage that result from unprofessional installation, if
the location of the device has been changed.
▪ In case of problems, errors or damage that result from external factors, such as other
devices that are connected to this device.
▪ In case of problems, errors or damage that result from catastrophic external influ-
ences, such as fire, earthquake, storm, flooding or lightning.