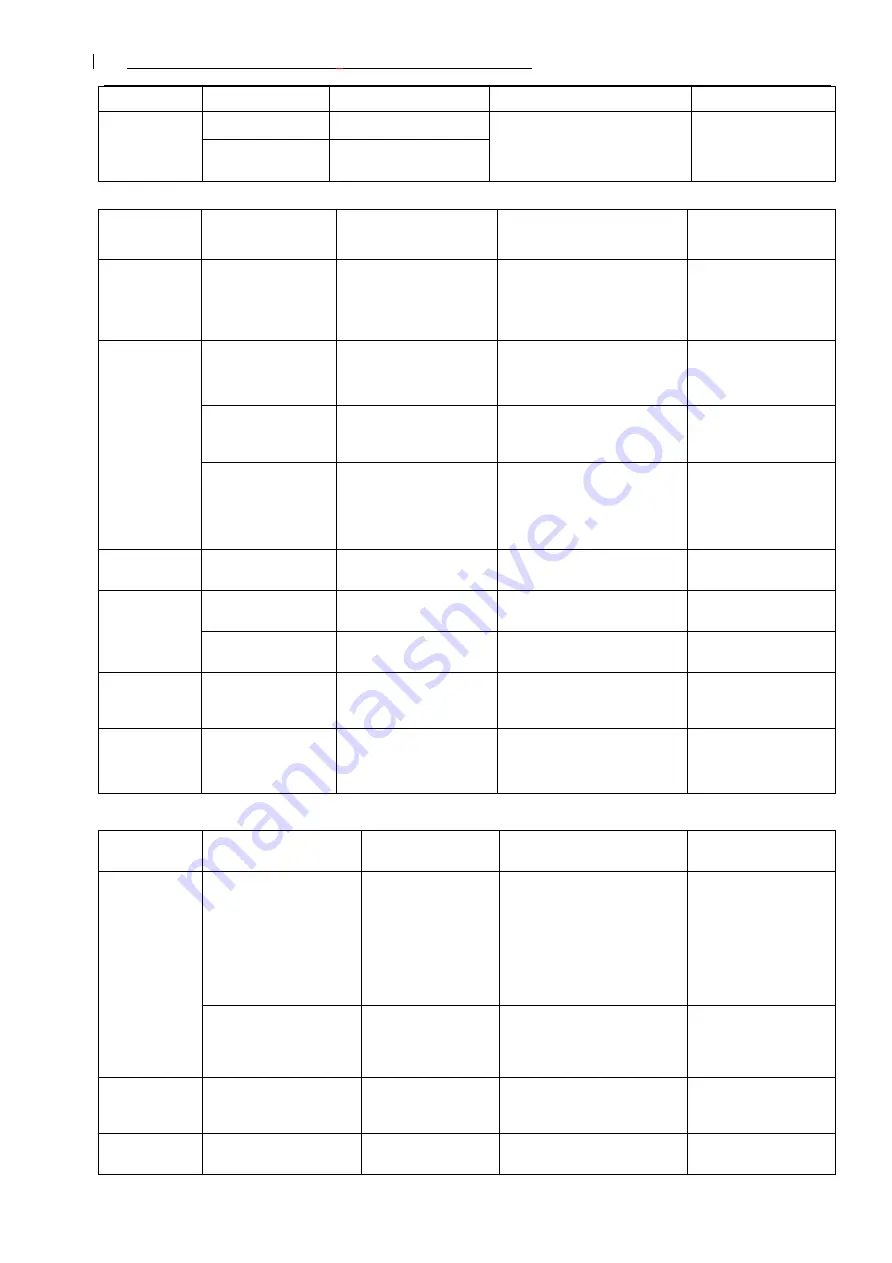
YG125-30A Maintenance Manual
Front wheel, front overhang and steering stem
113
2mm)
Speedometer
gear box
Gear is damaged
.
The indicator of the
speedometer fails to move
Replace
speedometer
gear
box
The gear drive
ring is damaged
.
Maintenance of Front Shock Absorber
Component
description
Damage form
Trouble symptom of
component
Trouble symptom of
motorcycle
Repair method
Front shock
absorber
spring
The elastic force is
Insufficient or
broken
The elastic force of
shock absorber is
Insufficient or broken
Front shock absorber is over
Soft, abnormal sound comes
out in case of front absorber
working
Replace front shock
absorber spring
Front shock
strut
Bending and
deformation
Front shock strut is bent
and deformed
Off-track in running
Correct or replace
front
shock strut
Working stroke
surface is damaged
or scratched
Leakage from oil seal
Leakage at front shock
cylinder
Replace front shock
strut
Working stroke
surface Cr coating
partial is worn out
to expose the
substrate
Leakage from oil seal
Leakage at front shock
cylinder
Replace front shock
strut
Front shock
cylinder
Broken deformed
and damaged
Leakage at front shock
cylinder
Leakage at front shock
cylinder
Replace front shock
cylinder
Piston rod
Over worn or
damaged
Over soft at front shock
cylinder
Replace piston rod
Piston ring is over
worn or damaged
Over soft at front shock
cylinder
Replace piston ring
Oil sealing
Cut edge is over
Worn or damaged
or aged
Leakage from oil seal
Leakage at front shock
absorber
Replace oil seal
Shock oil
Insufficient oil
amount or too little
Insufficient shock oil or
too
little
Over soft of front shock
absorber
Fill shock oil as per
the specified stipulate
Maintenance of Steering Post
Component
description
Damage form
Trouble symptom
of component
Trouble symptom of
motorcycle
Repair method
Steel ball
socket
Over tight of steering
stem screw
Too small gap
between steel ball
and steel ball
steering ring
Steering handle is
ineffective.
Adjust the steering
post screw by tighten
wrench till the
steering post moves
left and right flexibly
and no axial shifting
between steering post
and frame stand pipe
Over worn, pockmark,
indentation, crack and
damage of steel ball
steering ring ball track
Ineffective steering handle
or handle shakes or vibrates
during running
Replace complete
steel ball steering ring
Steel ball
The steel ball is worn,
deformed and
damaged.
Ineffective handle steering
or handle shakes or vibrates
during running
Replace all steel balls
Steering stem The steering stem is
deformed
The steering stem is
deformed.
The steering stem is
deformed.
Replace steering
stem
https://www.motomanuals.net/