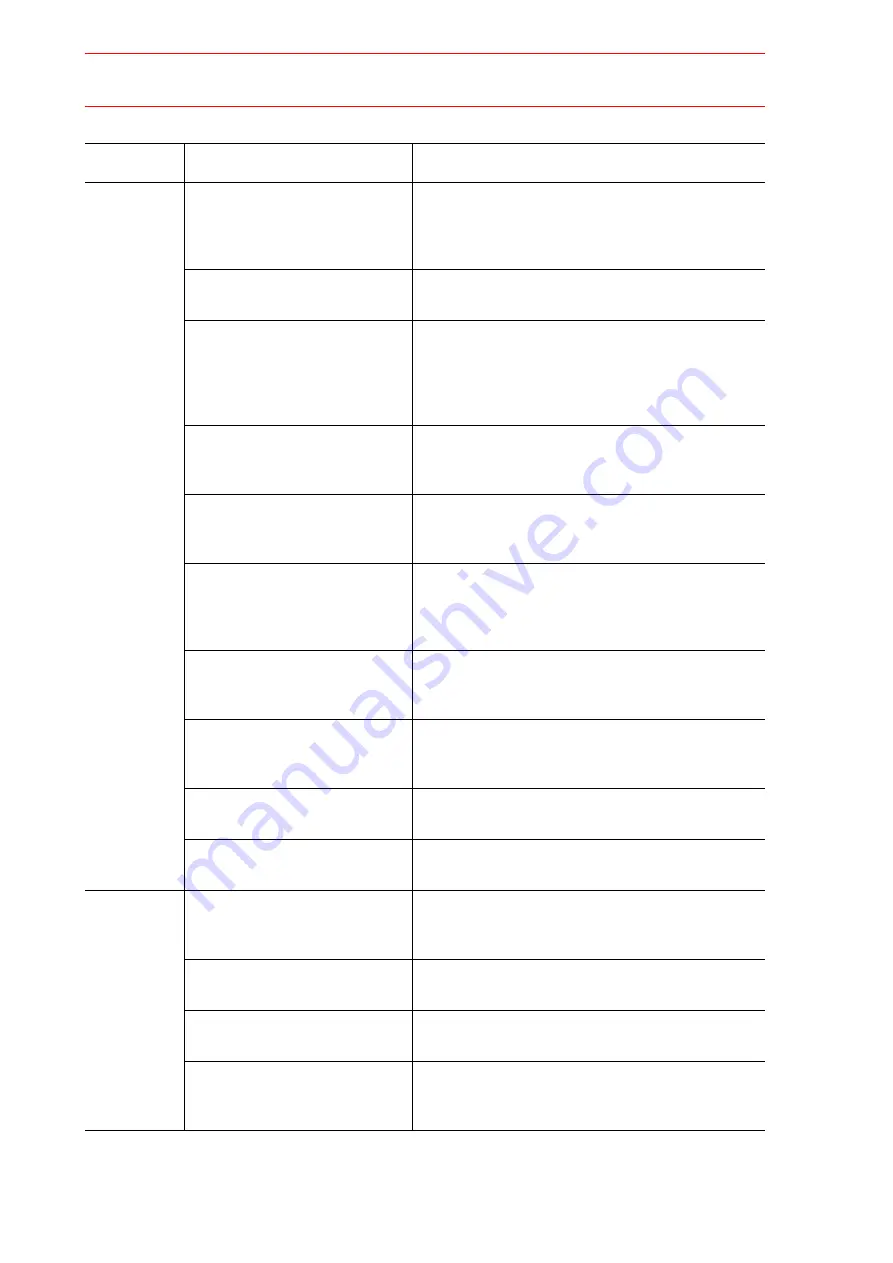
9.2 Cause and Remedy of Welding Section Failure
9-4
HW0480311
HW0480311
Arc is
unstable.
Power supply voltage exces-
sively fluctuates.
Use a different power supply from that of other
machines that cause power supply voltage fluctua-
tion. Or increase the power supply transformer
capacity.
Chip hole diameter becomes
larger and worn.
Replace the chip. (Use a genuine chip.)
Welding wire is not fed
smoothly.
Remove the dust or iron powder choking up the
feeding roller section or conduit.
Check that the conduit is not excessively bent and
that the liner, contact tip, and feeding roller match
the wire diameter.
Voltage between phases of the
3-phase power supply is not
balanced.
Use a different power supply from that of other
machines that cause the imbalance. Or increase
the power supply transformer capacity.
The welding conditions are not
correct.
Use the test arc to increase or decrease the set-
tings of the welding current value and voltage
value.
Unstable arc tends to occur
when thin-plate or small-current
welding is performed only with
carbon dioxide gas.
Use gas mixed with carbon dioxide gas and argon
gas to improve the arc behavior.
The connecting section is
loose.
Check each terminal connection and the connec-
tions with the base metal. Securely re-tighten if
necessary.
Voltage drop is excessive with
the extension cable.
Shorten the extension cable’s length.
Use a thicker cable. Use the extension cable with-
out bending it.
The polarities of the secondary
terminal are inverted.
Correct the connection of + and -.
Jig current conduction is poor.
Correct the contact between the jig and the base
metal.
Excessive
spatters
The welding conditions are not
correct.
Increase or decrease the settings of the welding
voltage and current values to adjust the welding
conditions.
Welding wire is not suitable for
the shielding gas.
Check if a welding wire suitable for the welding
type is used.
The status of the base metal is
poor.
Check the groove forms or dirt of the base metal.
Replace them with one of higher accuracy.
The welding section is dis-
torted.
Check each terminal connection and the connec-
tions with base metal. Polish the contacting face
and tighten them securely.
Table. 12 Failure Analyses for Welding Section
Fault
Cause
Remedy
76/129