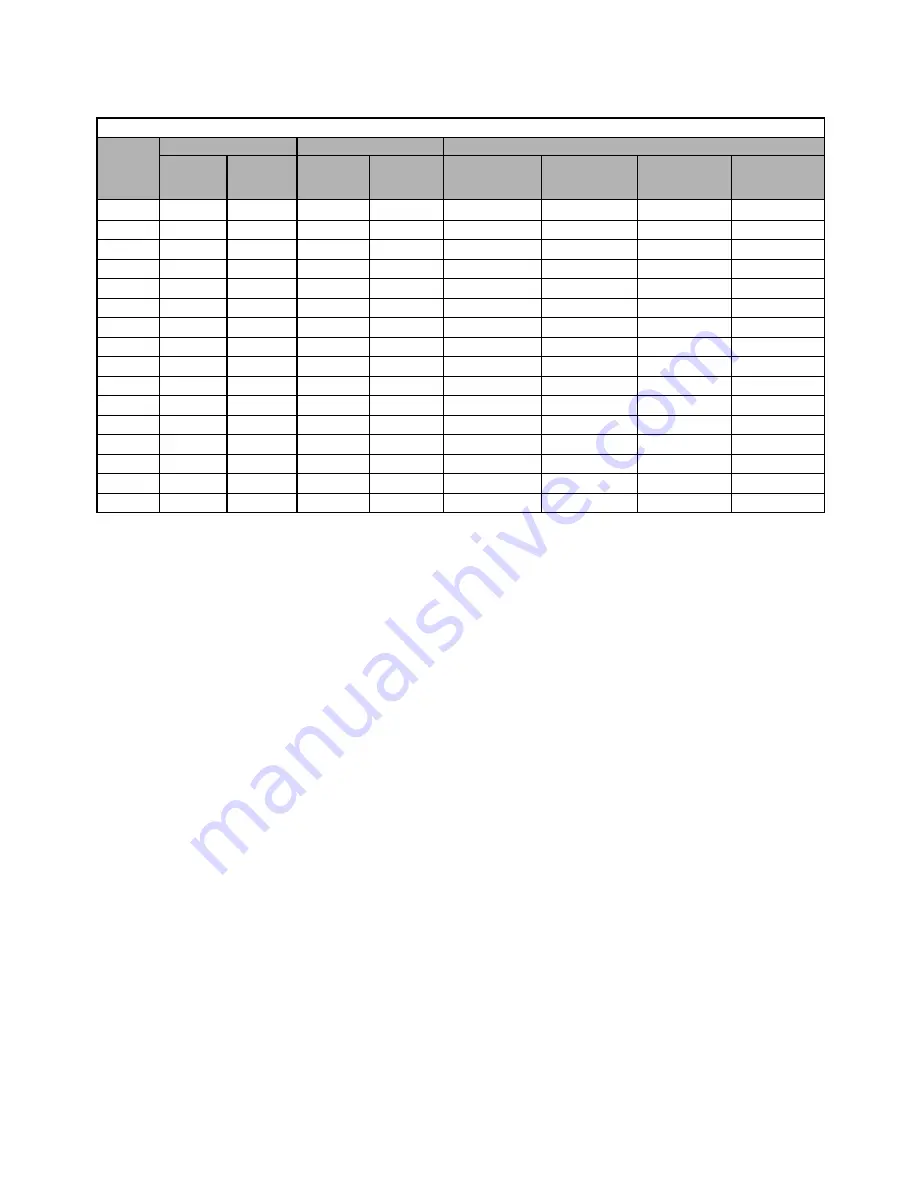
Programming 81
The following table shows the programming choices.
Function: PID Integral Reset
Setting: 30
By configuring one of the digital inputs as an Integral Reset Input, (H1-0x= 30), the value of the integral component of PID
control can be reset to zero whenever the configured input is CLOSED. The integral component of PID control will be held at
zero as long as the configured digital input is held CLOSED.
Resetting the Integral component of PID control can be useful in cases where an excessively large Integral value prevents the PID
control from responding quickly to changes in the system being regulated by the Drive (e.g. duct pressure, water temperature).
Function: PID Integral Hold
Setting: 31
By configuring a digital input as an Integral Hold input (H1-0X= 31), the value of the Integral component of the PID control
can be forced to clamp at the value it was at when the input is CLOSED. The Integral component of the PID control returns to
accumulating the error when the digital input is OPEN again.
Holding the Integral Value can be useful during periods when the error can build up naturally, such as during long
accelerations. Not allowing Integral wind-up produces a more stable PID control.
Function: Multi-step Reference 4
Setting: 32
See setting 3, 4, and 5 for description.
Table 16 Programming Choices
Set
Value
Input Contact Type
Detection Mode
stopping Method
N.O.
contact
N.C.
contact
Always
Detected
Detected
while
Running
Decel to stop
(major fault)
Coast to stop
(major fault)
Fast stop
(major fault)
Continue
operation
(minor fault)
20
X
X
X
21
X
X
X
22
X
X
X
23
X
X
X
24
X
X
X
25
X
X
X
26
X
X
X
27
X
X
X
28
X
X
X
29
X
X
X
2A
X
X
X
2B
X
X
X
2C
X
X
X
2D
X
X
X
2E
X
X
X
2F
X
X
X
Summary of Contents for Varispeed f7
Page 1: ...F7 Drive Programming Manual Model CIMR F7U Document Number TM F7 02...
Page 2: ......
Page 8: ...vi Notes...
Page 158: ...Programming 150 Notes...