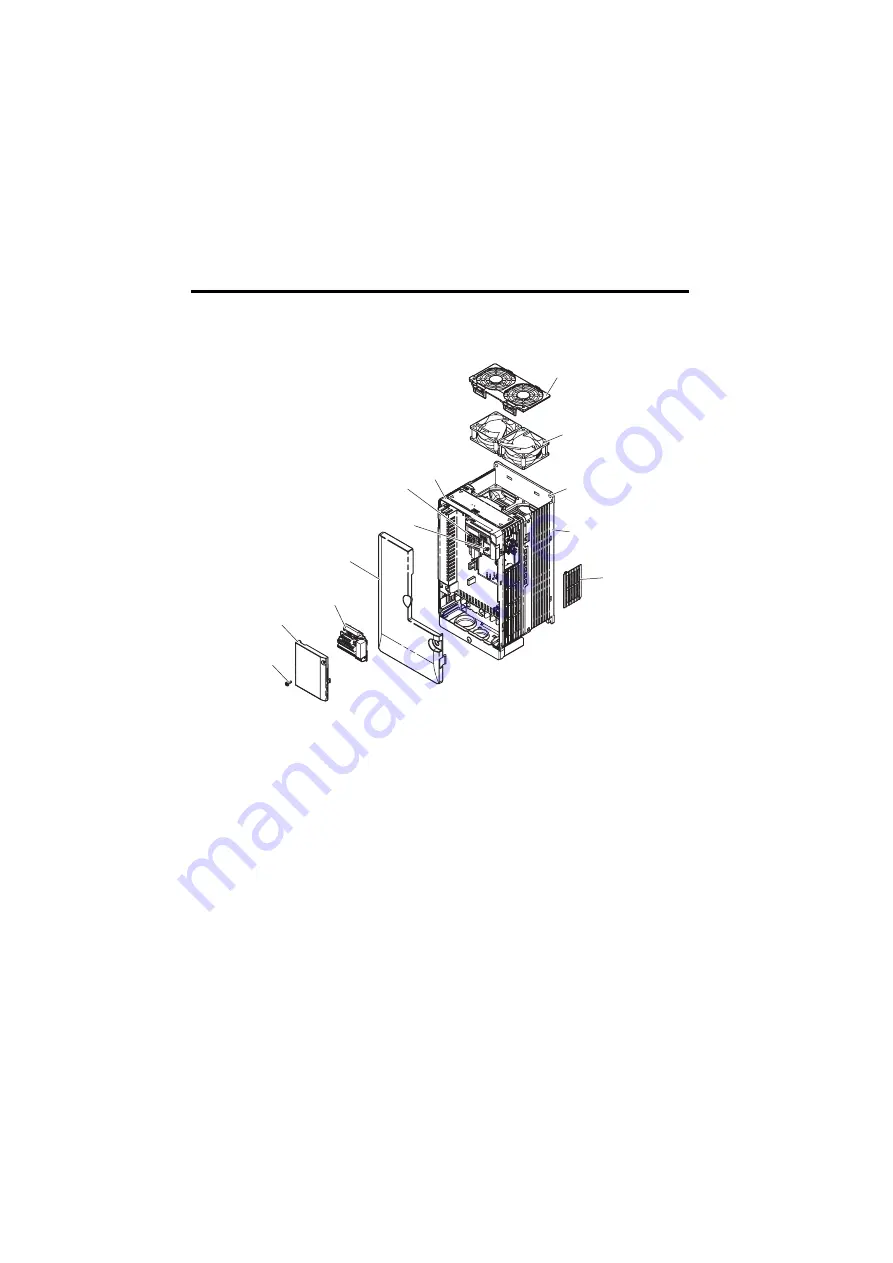
1.4 Component Names
34
YASKAWA ELECTRIC
TOEP C710606 09B YASKAWA AC Drive V1000 Installation & Start-Up Manual
■
Three-phase AC200 V CIMR-V
2A0030F ~ 0069F
Three-phase AC400 V CIMR-V
4A00018F ~ 0038F
Figure 1.6
Figure 1.6 Exploded view of IP20/NEMA Type 1 Components
Three-phase AC400 V CIMR-V
4A0018F
A – Fan cover
G – Front cover
B – Cooling fan
Refer to Drive Cooling Fans on
page 254
H – Terminal board
Refer to Control Circuit Terminal
Block Functions on page 72
C – Mounting Hole
I – Terminal cover
D – Heatsink
J – Comm port
Refer to Network Communications
on page 401
E – Cable cover
K – LED operator
Refer to Using the Digital LED
Operator on page 91
F – Front cover screws
L – Case
C
B
A
D
E
F
G
L
H
J
K
I
Summary of Contents for V1000 Series
Page 2: ...2 YASKAWA ELECTRIC TOEP C710606 09B YASKAWA AC Drive V1000 Installation Start Up Manual...
Page 464: ...464 YASKAWA ELECTRIC TOEP C710606 09B YASKAWA AC Drive V1000 Installation Start Up Manual...
Page 465: ...YASKAWA ELECTRIC TOEP C710606 09B YASKAWA AC Drive V1000 Installation Start Up Manual 465...