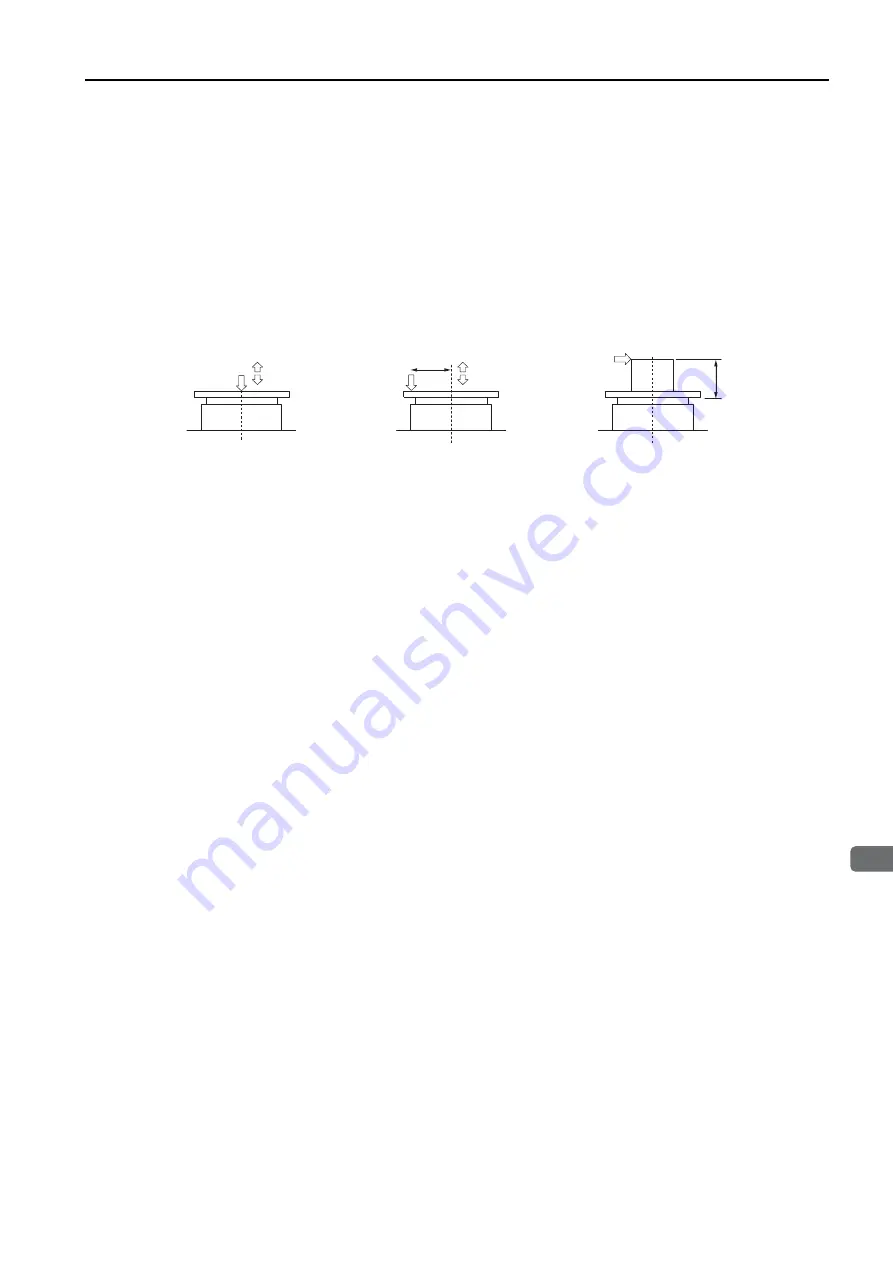
3.2 Specifications and Ratings
3.2.2 Ratings
3-7
3
S
pecification
s
, Rating
s
, and Exter
nal Dimen
s
ion
s
of
S
GM7D
S
ervomotor
s
*2.
The repetitive rated torque is the value for 60% ED.
*3.
To externally connect dynamic brake resistance, select hardware option specification 020 for the SERVOPACK.
However, you cannot externally connect dynamic brake resistance if you use the following SERVOPACKs (max-
imum applicable motor capacity: 400 W).
•
SGD7S-2R8
A020F82
•
SGD7S-2R8
00A020F83
*4.
If you use an SGD7S-120A008 SERVOPACK and SGM7D Servomotor together, use the ratios given on the bot-
tom line.
*5.
The thrust loads and moment loads that are applied while a Servomotor is operating are roughly classified into
the following patterns. Design the machine so that the thrust loads or moment loads will not exceed the values
given in the table.
The allowable load is for a static load in one direction.
When designing the system, multiply the allowable load by the following safety coefficient depending on the
type of load.
•
Smooth load with no shock: 1/3
•
Light repetitive load: 1/5
•
Shock load: 1/10
Note: 1. These values are for operation in combination with a SERVOPACK when the temperature of the armature
winding is 20°C. These are typical values.
2. For the bearings used in these Servomotors, the loss depends on the bearing temperature. The amount of
heat loss is higher at low temperatures.
F
Where F i
s
the external force,
Thru
s
t load = F + Load ma
ss
Moment load = F × L
Where F i
s
the external force,
Thru
s
t load = F + Load ma
ss
Moment load = 0
Where F i
s
the external force,
Thru
s
t load = Load ma
ss
Moment load = F × L
Rever
s
e
Forward
Thru
s
t load direction
Rever
s
e
Forward
Thru
s
t load direction
F
L
F
L