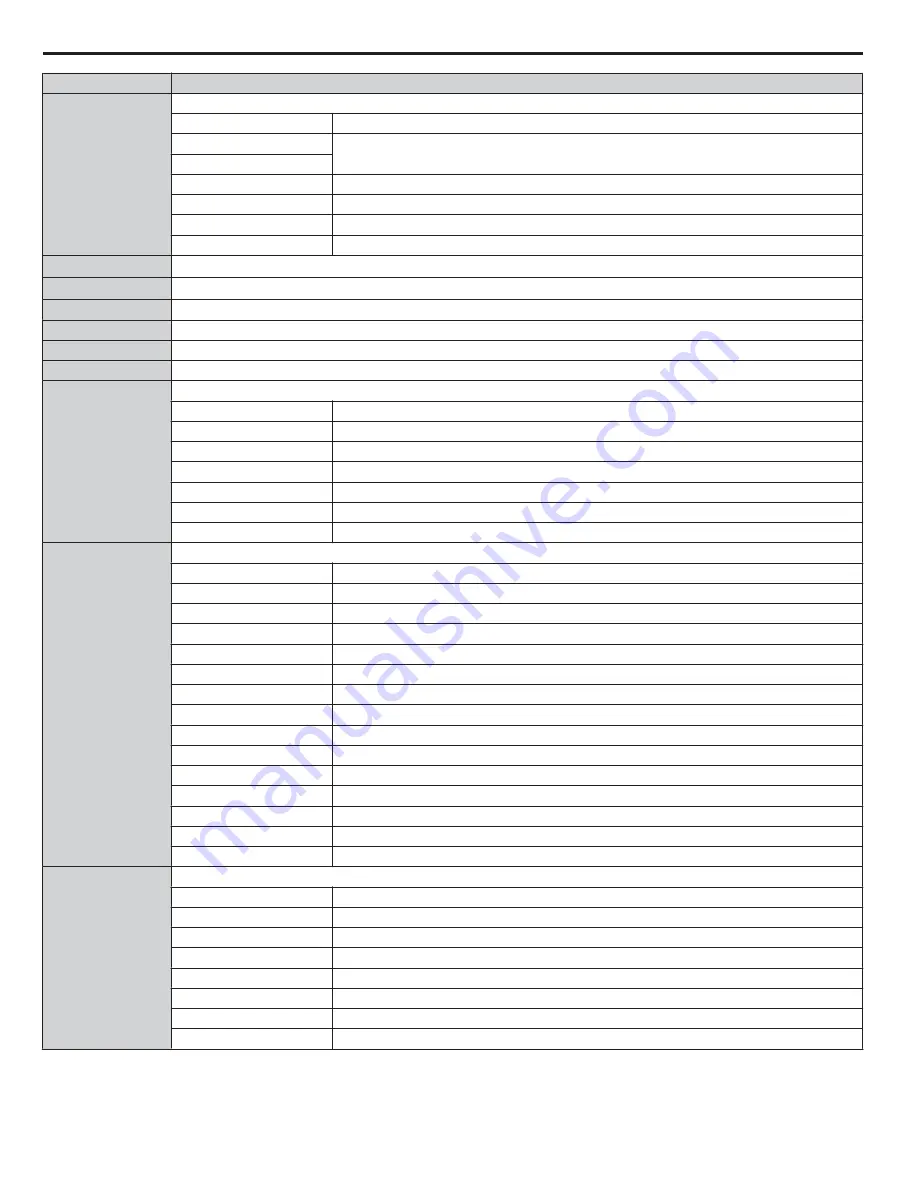
5
e
J
ister No
Contents
0022H
Data Link Status
bit 0
Writing data or switching motors
bit 1
Reserved
bit 2
bit 3
Upper or lower limit error
bit 4
Data conformity error
bit 5
Writing to EEPROM
bit 6 to F
Reserved
0023H
Frequency Reference
<1>
0024H
Output Frequency
<1>
0025H
Output Voltage Reference, 0.1 V units (units are determined by parameter H5-10)
0026H
Output Current, 0.1 A units
0027H
Output Power
0028H
Reserved
0029H
Fault Contents 2
bit 0
Reserved
bit 1
Ground Fault (GF)
bit 2
Input Phase Loss (PF)
bit 3
Output Phase Loss (LF)
bit 4, bit 5
Reserved
bit 6
Motor Overheat 2 (PTC input) (oH4)
bit 7 to F
Reserved
002AH
Alarm Contents 1
bit 0, 1
Reserved
bit 2
Run Command Input Error (EF)
bit 3
Drive Baseblock (bb)
bit 4
Overtorque Detection 1 (oL3)
bit 5
Heatsink Overheat (oH)
bit 6
Overvoltage (ov)
bit 7
Undervoltage (Uv)
bit 8
Cooling Fan Error (FAn)
bit 9
MEMOBUS/Modbus Communication Error (CE)
bit A
Option Communication Error (bUS)
bit B
Undertorque Detection 1 (UL3)
bit C
Motor Overheat (oH3)
bit D
PI Feedback Loss (FbL, FbH)
bit E
Reserved
bit F
Serial Communication Transmission Error (CALL)
002BH
Input Terminal Status
bit 0
Terminal S1 Closed
bit 1
Terminal S2 Closed
bit 2
Terminal S3 Closed
bit 3
Terminal S4 Closed
bit 4
Terminal S5 Closed
bit 5
Terminal S6 Closed
bit 6
Terminal S7 Closed
bit 7 to F
Reserved
E
MEMOBUS/Modbus Data
7
able
<$6.$:$(/(&75,&
6,(3&(<$6.$:$$&'ULYH±=3URJUDPPLQJ0DQXDO
Summary of Contents for CIMR-ZU A Series
Page 10: ...7able oI Contents 7Kis PaJe Intentionally BlanN 1 6 75 6 3 6 ULYH 3URJUDPPLQJ 0DQXDO...
Page 210: ...2 DriYe CoolinJ Fans 7Kis PaJe Intentionally BlanN 21 6 75 6 3 6 ULYH 3URJUDPPLQJ 0DQXDO...
Page 320: ...C 8 7roublesKootinJ 7Kis PaJe Intentionally BlanN 2 6 75 6 3 6 ULYH 3URJUDPPLQJ 0DQXDO...
Page 377: ......