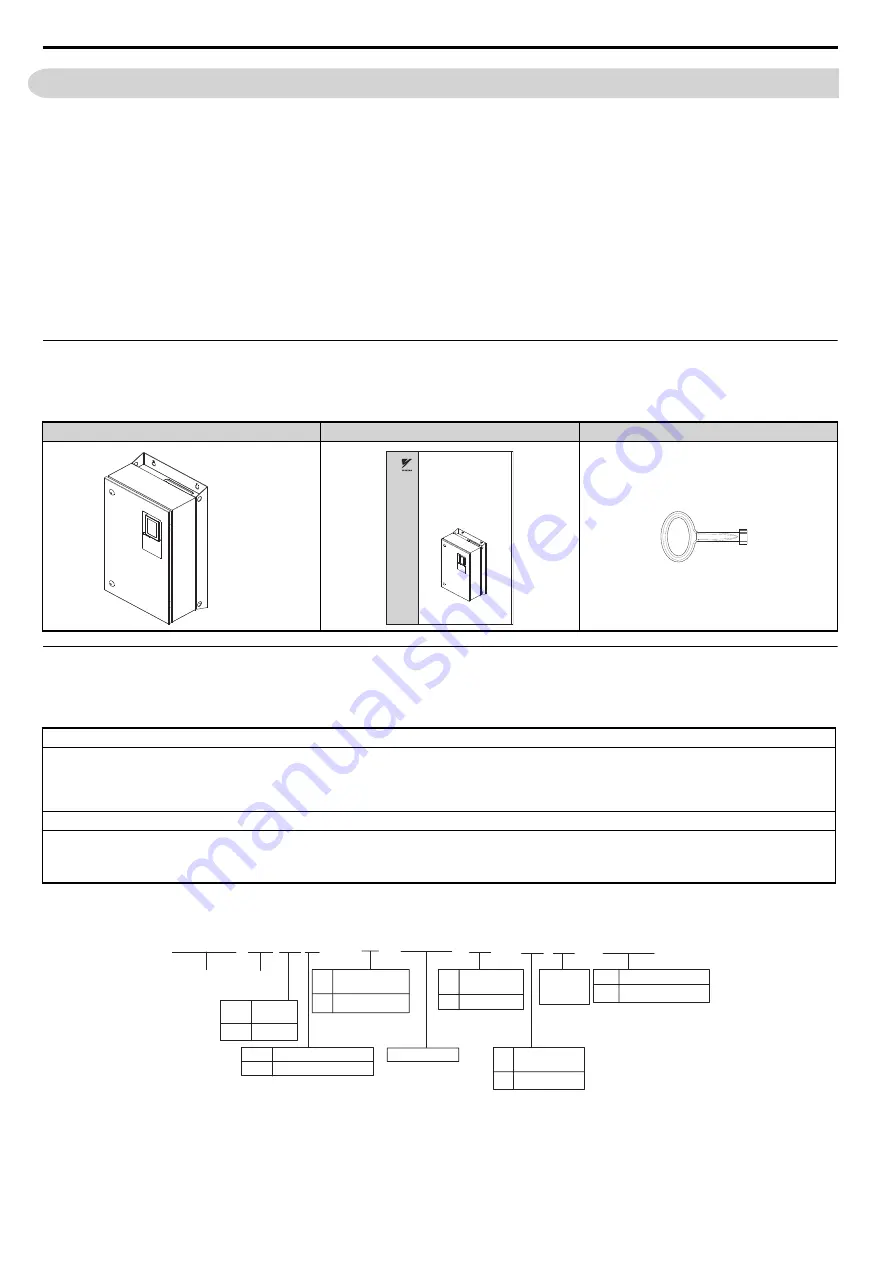
EN 4
YASKAWA Europe TOEP C710606 96A - AC Drive A1000 IP54 Wallmount - Quick Start Guide
1 Safety Instructions and General Warnings
1
Safety Instructions and General Warnings
YASKAWA Europe supplies component parts for use in a wide variety of industrial applications. The selection and
application of YASKAWA products remain the responsibility of the equipment designer or end user. YASKAWA
accepts no responsibility for the way its products are incorporated into the final system design. Under no circumstances
should any YASKAWA product be incorporated into any product or design as the exclusive or sole safety control.
Without exception, all controls should be designed to detect faults dynamically and fail safely under all circumstances.
All products designed to incorporate a component part manufactured by YASKAWA must be supplied to the end user
with appropriate warnings and instructions as to the safe use and operation of that part. Any warnings provided by
YASKAWA must be promptly provided to the end user. YASKAWA offers an express warranty only as to the quality of
its products in conforming to standards and specifications published in the manual. NO OTHER WARRANTY,
EXPRESS OR IMPLIED, IS OFFERED. YASKAWA assumes no liability for any personal injury, property damage,
losses, or claims arising from misapplication of its products.
Scope of Delivery
A1000 IP54 drives are prepared for wall-mounting indoors. Exposure to corrosive atmosphere is not allowed.
Applicable Documentation
The following manuals are available for A1000 series drives:
Drive Model Identification
A1000 Drive
Quick Start Guide
Panel Key
A1000 Series AC Drive Technical Manual
This manual provides detailed information on parameter settings, drive functions, and MEMOBUS/Modbus specifications. Use this manual to
expand drive functionality and to take advantage of higher performance features.
A1000 Series AC Drive Quick Start Guide (this book)
Read this manual first. This guide is packaged together with the product. It contains basic information required to install and wire the drive, in
addition to an overview of fault diagnostics, maintenance, and parameter settings. Use the information in this book to prepare the drive for a trial
run with the application and for basic operation.
YASKAWA AC Drive A1000
IP54
Quick Start Guide
MANUAL NO. TOEP C710616 27D
Type: CIMR-AC4A
Models: 400 V Class: 18.5 to 90 kW
To properly use the product, read this manual thoroughly and retain for
easy reference, inspection, and maintenance. Ensure the end user receives
this manual.
TAA
C I M R -
Drive
A1000
Series
No.
Region
Code
No.
Voltage Class
Environmental
Specification
Design
Revision
Order
No.
Customized
Specifications
A
Standard
4
A C 4
A
0 0 5 8
T
A
A
C
Europe
No.
Enclosure
Type
T
IP54
No.
A
Standard
3-phase, 380-480 Vac
Model Number
- 0 0 9 5
no mains switch
blank
0095 built-in mains switch