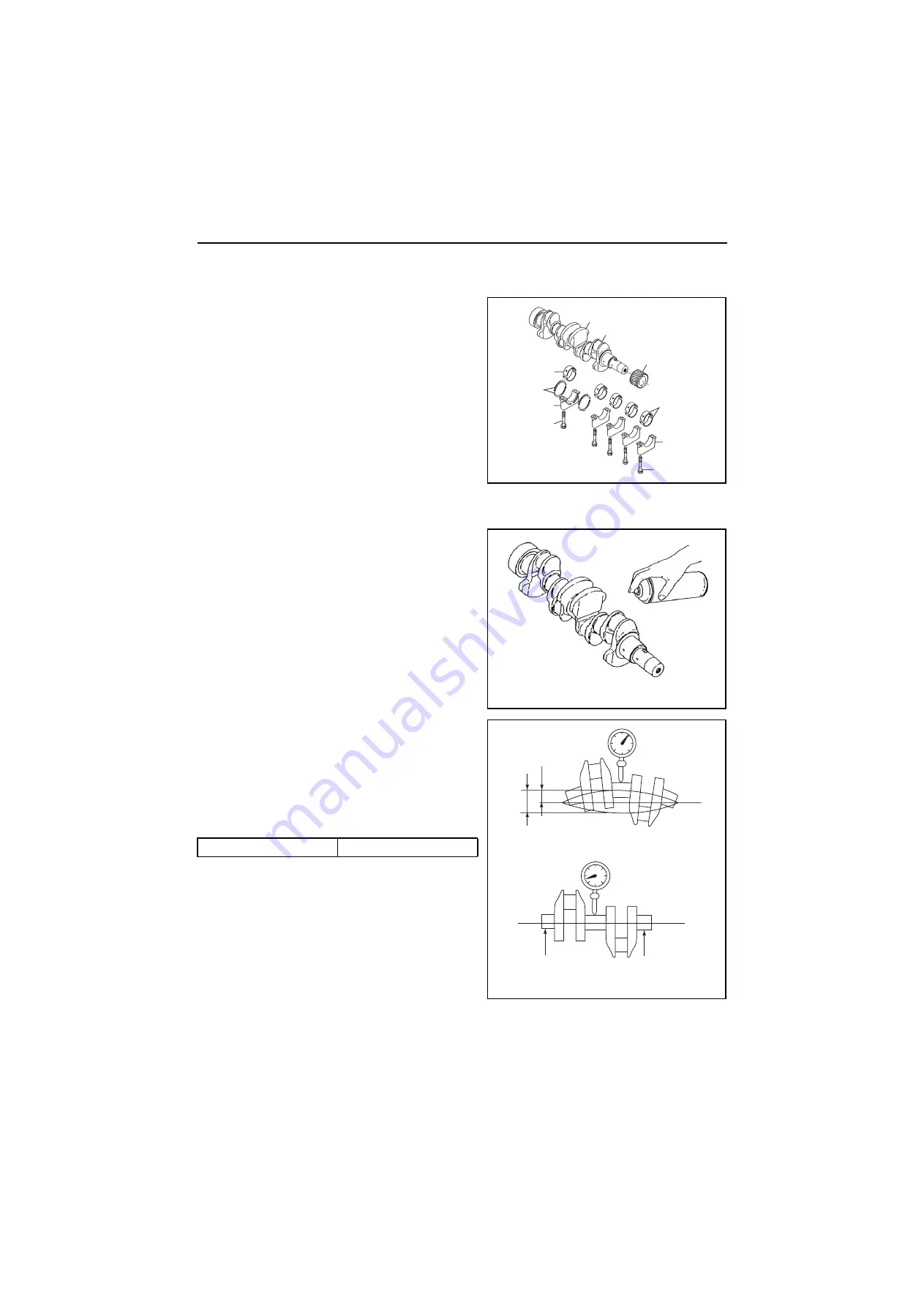
5. Inspection and servicing of basic engine parts
125
5.5 Crankshaft and main bearing
The crank pin and crank journal have been induction
hardened for superior durability, and the crankshaft is
provided with for balance weights for optional balance.
The crankshaft main veering is of the hanger type. The
upper metal (cylinder block side) is provided with an oil
groove. There is no oil groove on the lower metal
(bearing cap side). The veering cap (location cap) of the
flywheel side has a thrust metal which supports the
thrust load.
5.5.1 Crankshaft
(1) Color check after cleaning the crankshaft,
and replace the crank shaft if there is any
cracking or considerable damage.
(2) Bending of the crankshaft
Support the crankshaft with V-blocks at both ends of the
journals. Measure the deflection of the center journal
with a dial gauge while rotating the crankshaft to check
the extent of crankshaft bending. The total indicating
reading on the dial gauge is divided by two to obtain the
crankshaft
bend.
mm
Crankshaft bend limit
0.01
Balance weight
Crank shaft
Crank shaft gear
Main bearing
metal (basic)
Main bearing
cap (basic)
Main bearing bolt
Thrust metal
Main bearing cap
(intermediate)
Main bearing metal
(intermediate)
Main bearing bolt
(Inspection by color check)
Bend
Deflection
Dial gage
V-block
V-block
(Crankshaft bend measurement)
Summary of Contents for 3YM20
Page 1: ...M9961 03E100 ...