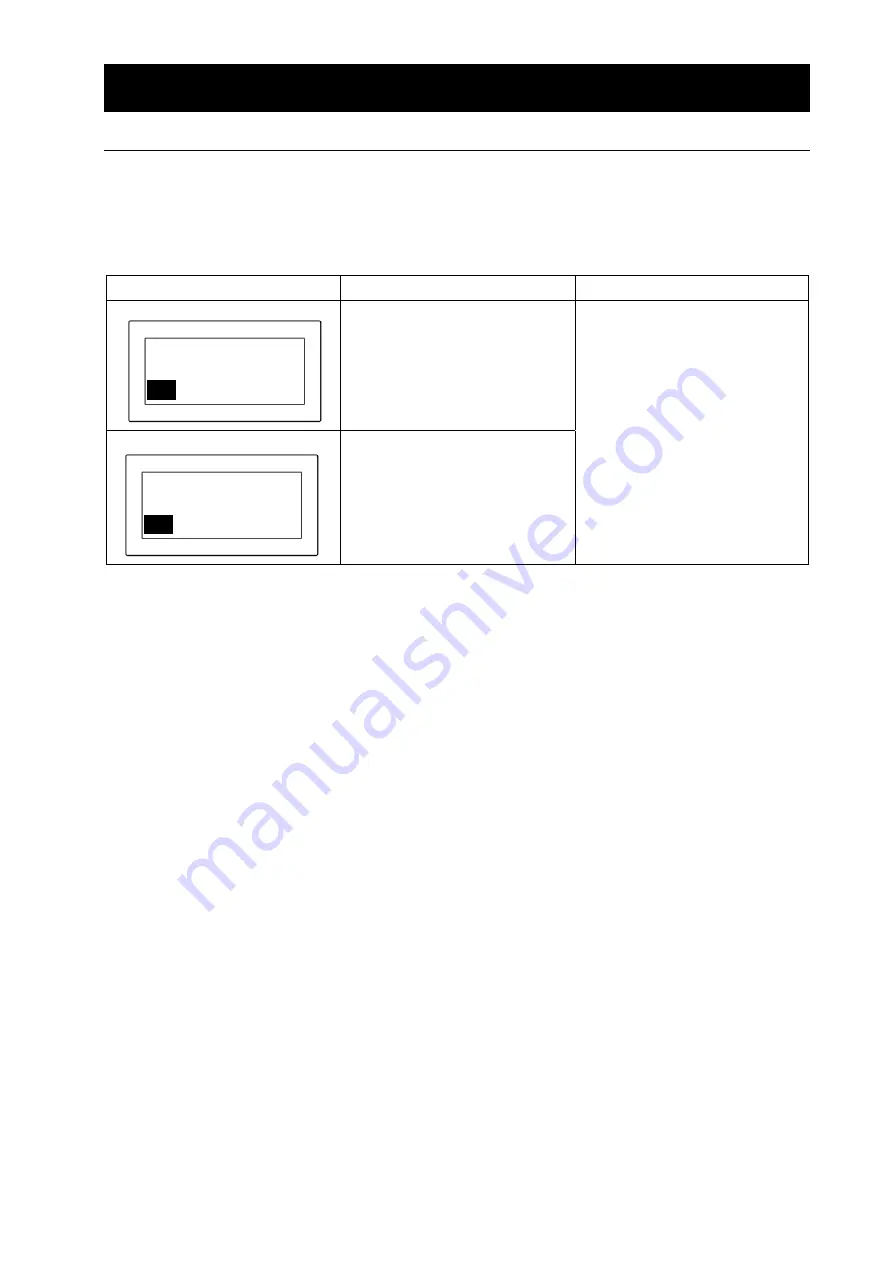
27
8. When a trouble occurs
Safety unit and error indications
The table shows possible causes of activation of the safety unit and solutions.
[Error indication]
When an abnormality occurs to the inlet temperature controller or the outlet temperature controller,
the touch panel at the operation panel displays the error screen. When an abnormality occurred,
confirm description of the error and implement appropriate solutions.
Display Possible
causes Solutions
①
Disconnection of the
thermocouple sensor
②
When the displayed inlet
temperature is at 320
°
C or
over
③
Malfunction of the blower
①
Disconnection of the
thermocouple sensor
②
When the displayed outlet
temperature is at 110
°
C or
over
③
Malfunction of the blower
①
Replacement of the
thermocouple sensor
②
Lower the set temperature
or adjust air amount.
③
Replacement of the blower
* When the measured temperature exceeds the set upper limit (upper limit of inlet temperature:
320
°
C; upper limit of outlet temperature: 110
°
C), "Over Heat" will appear, the heater output will stop
and when that status continues for one minute, the temperature error above will be displayed. The
safety unit will perform automatic REV operation for five seconds when a temperature error
occurred while the blower is ON, the heater is OFF, or the liquid sending pump was in operation
and then shift to the stop mode.
The same process as shown above will take place when the disconnection of the temperature
sensor occurred. The temperature controller will indicate "-----".
Pressing "ESC" key will release the error screen and the status will return to the "BLOWER ON"
and "HEATER OFF" status.
Spray Inlet
Temperature Overheat
ESC
ESC
outlet
Temperature Overheat