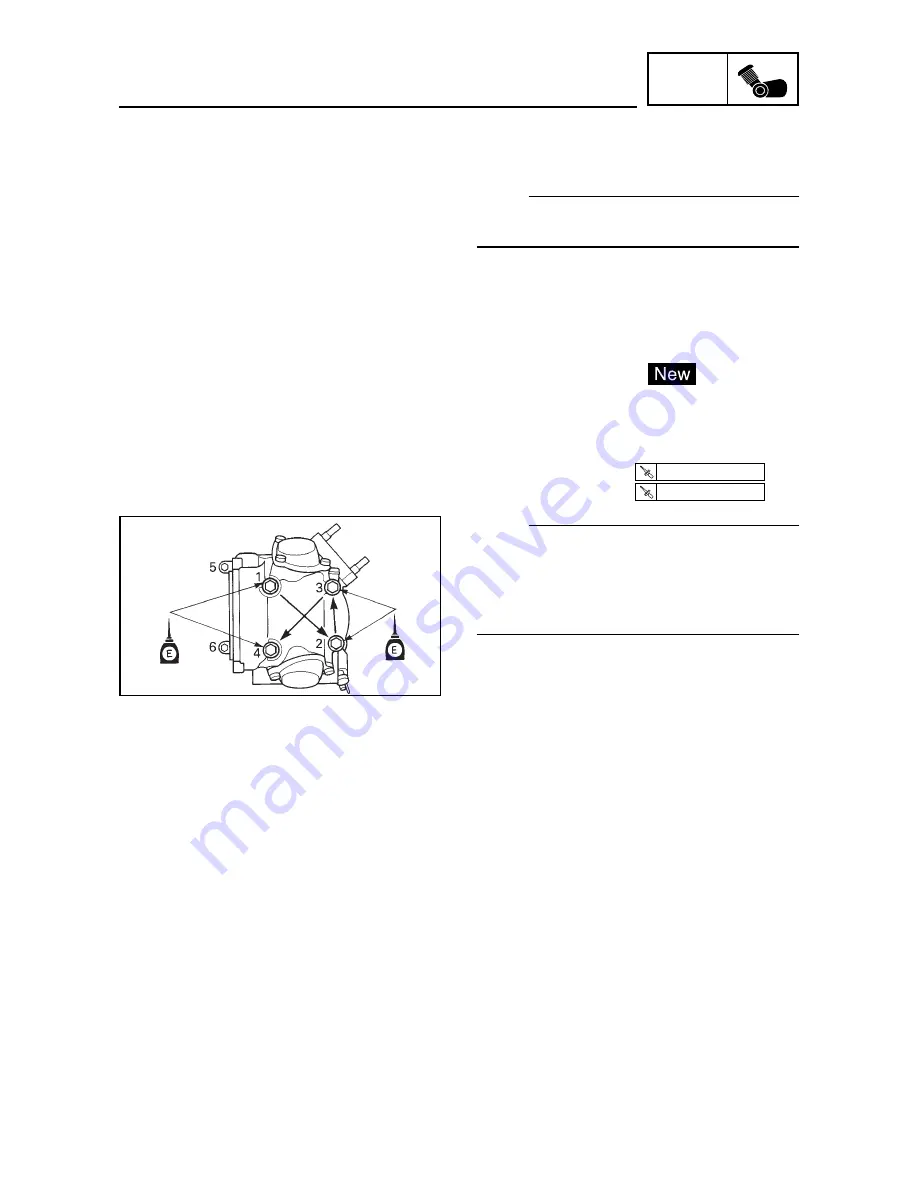
ENG
4-13
EAS00232
INSTALLING THE CYLINDER HEAD
1. Install:
• cylinder head gasket
• dowel pins
2. Install:
• cylinder head
• copper washers
• cylinder head nuts
• cylinder haed bolts
NOTE:
• Lubricate the cylinder head nuts with engine
oil.
• Tighten the cylinder head nuts in the proper
tightening sequence as shown and torque them
in two stages.
3. Install:
• camshaft
• rocker arms
Refer to “INSTALLING THE CAMSHAFTS
AND ROCKER ARMS” section.
d. Place a 400 ~ 600 grit wet sandpaper on the
surface plate and resurface the cylinder head
using a figure-eight sanding pattern.
NOTE:
To ensure an even surface, rotate the cylinder
head several times.
왖 왖 왖 왖 왖 왖 왖 왖 왖 왖 왖 왖 왖 왖 왖 왖 왖 왖 왖 왖 왖 왖 왖 왖 왖 왖 왖 왖 왖
CYLINDER HEAD
T.R
22 Nm (2.2m•kg)
T.R
12 Nm (1.2m•kg)
Summary of Contents for XN125 2000
Page 1: ...XN125 2000 XN150 5MF1 AE2 SERVICE MANUAL ...
Page 7: ...1 GEN INFO ...
Page 18: ...2 SPEC ...
Page 47: ...3 CHK ADJ ...
Page 94: ...4 ENG ...
Page 146: ...5 COOL ...
Page 156: ...6 CARB ...
Page 165: ...7 CHAS ...
Page 206: ...8 ELEC ...
Page 250: ...9 TRBL SHTG ...