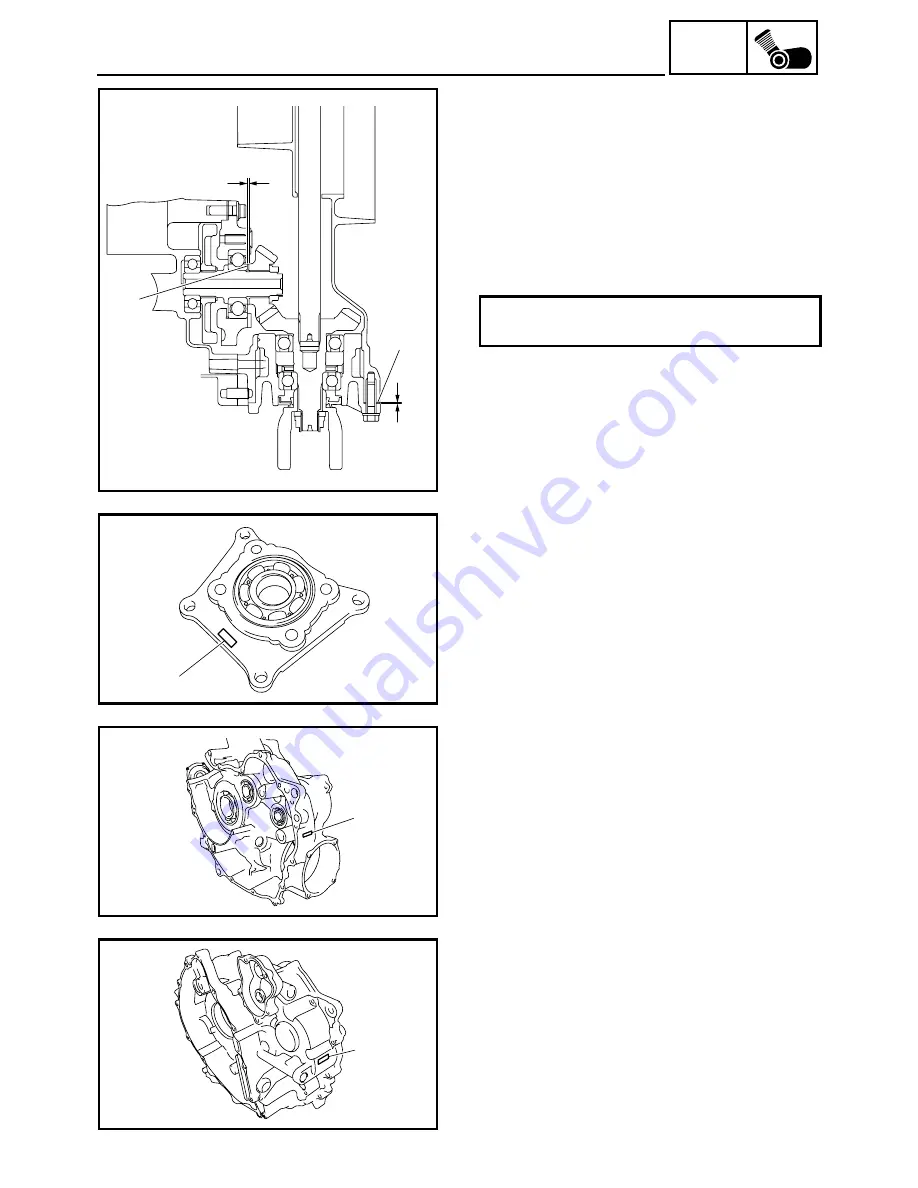
4 - 99
ENG
MIDDLE GEAR
▼▼▼
▼
▼ ▼▼▼
▼
▼ ▼▼▼
▼
▼ ▼▼▼
▼
▼ ▼▼▼
▼
▼ ▼▼▼
▼
▼▼▼
a. Position middle drive and driven gear by
using shims
1
and
2
with their respective
thickness calculated from information
marked on crankcase, bearing housing and
drive gear end.
1
Shim thickness “A”
2
Shim thickness “B”
b. To find shim thickness “A”, use following for-
mula:
Where:
a
= a numeral (usually a decimal number) on
the bearing housing is either added to or
subtracted from “0.9”
b
= 17.0
c
= 55.0
d
= a numeral (usually a decimal number) on
the left crankcase specifies a thickness of
“65.0”
e
= a numeral (usually a decimal number) on
the right crankcase specifies a thickness
of “9.0”
k
= 1.5
Example:
1) If the bearing housing is marked “+01”,
.....
a
is 0.91
2)
b
is 17.0
3)
c
is 55.0
4) If the left crankcase is marked “64.96”,
.....
d
is 64.96
5) If the right crankcase is marked “9.01”,
.....
e
is 9.01
6)
k
is 1.5
7) Therefore, the shim thickness is 1.38 mm.
“A” = 9.01 + 64.96 + 0.91 – 55.0 – 17.0 – 1.5
= 1.38
Middle drive pinion gear shim thickness
“A” =
e
+
d
+
a
–
c
–
b
–
k
1
“A”
“B”
2
a
d
e