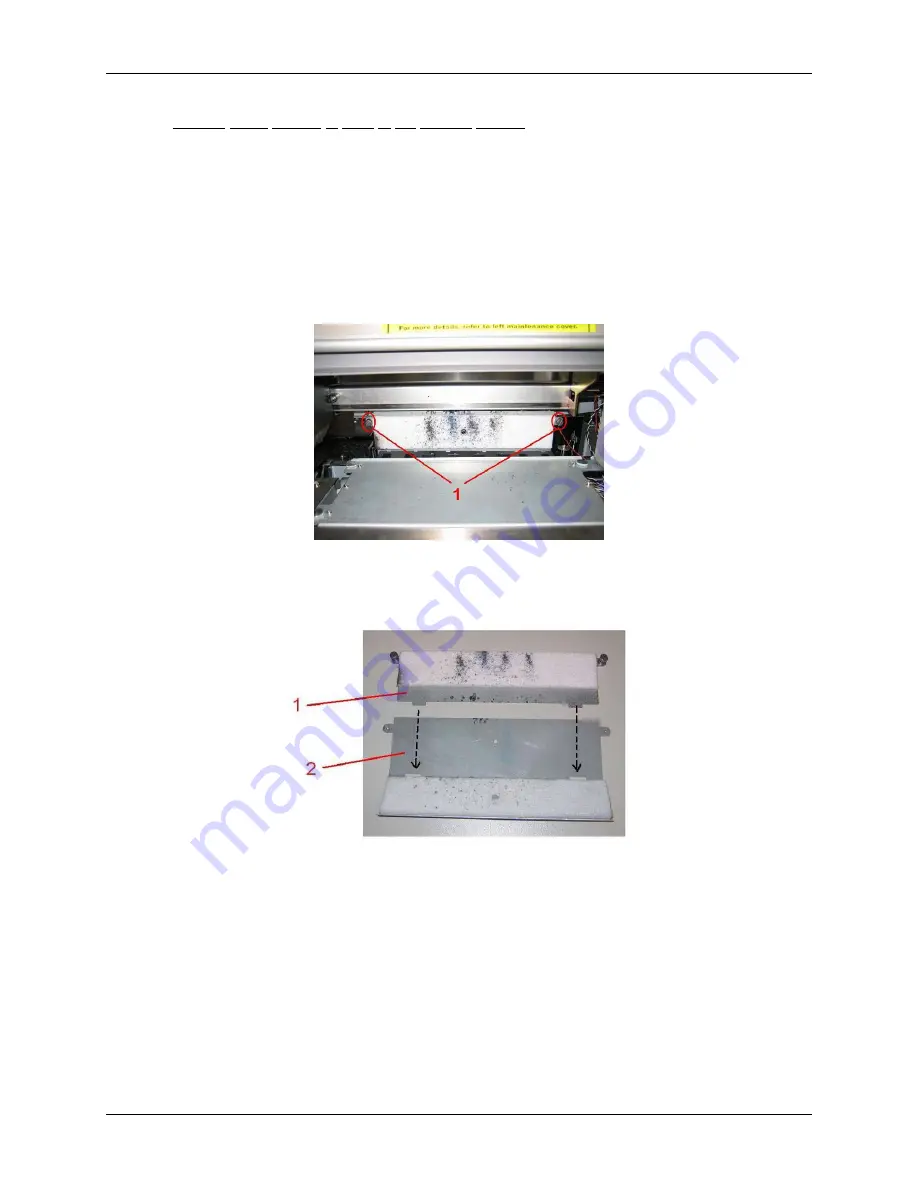
6 Maintenance
8265/8290/8365/8390 User Guide
119
6.3.4.2 Change upper sponge at back of the capping station.
Step 1 :
Power ON the printer.
Step 2 :
Go to the H.Unlock Menu and press F2.
Step 3 :
Open the Front Cover.
Step 4 :
Slide the carriage to the left to access the upper sponge.
Step 5 :
Remove the two screws fixing the sponge (1).
1 = Screws fixing the sponge (1)
Step 6 :
Replace the sponge and tighten it again to the plate with the two screws.
1 = Capping sponge
2 = Plate
Step 7 :
Close the Front Cover.
Step 8 :
Press the [ENTER] key to exit the H.Unlock Menu. The carriage will cap in and be locked.
Summary of Contents for 8290
Page 1: ...May 2008 701P48331 8265 8290 8365 8390 Wide Format Color Printer User Guide ...
Page 2: ......
Page 4: ...This page has been intentionally left blank ...
Page 8: ...iv 8265 8290 8365 8390 User Guide This page has been intentionally left blank ...
Page 13: ...1 Safety Instructions 8265 8290 8365 8390 User Guide 5 No Type 1 2 3 4 5 ...
Page 14: ...1 Safety Instructions 6 8265 8290 8365 8390 User Guide 6 7 8 9 ...
Page 140: ...6 Maintenance 132 8265 8290 8365 8390 User Guide This page has been intentionally left blank ...
Page 148: ...7 Adjustments 140 8265 8290 8365 8390 User Guide This page has been intentionally left blank ...
Page 150: ...8 Appendix 142 8265 8290 8365 8390 User Guide This page has been intentionally left blank ...
Page 151: ......