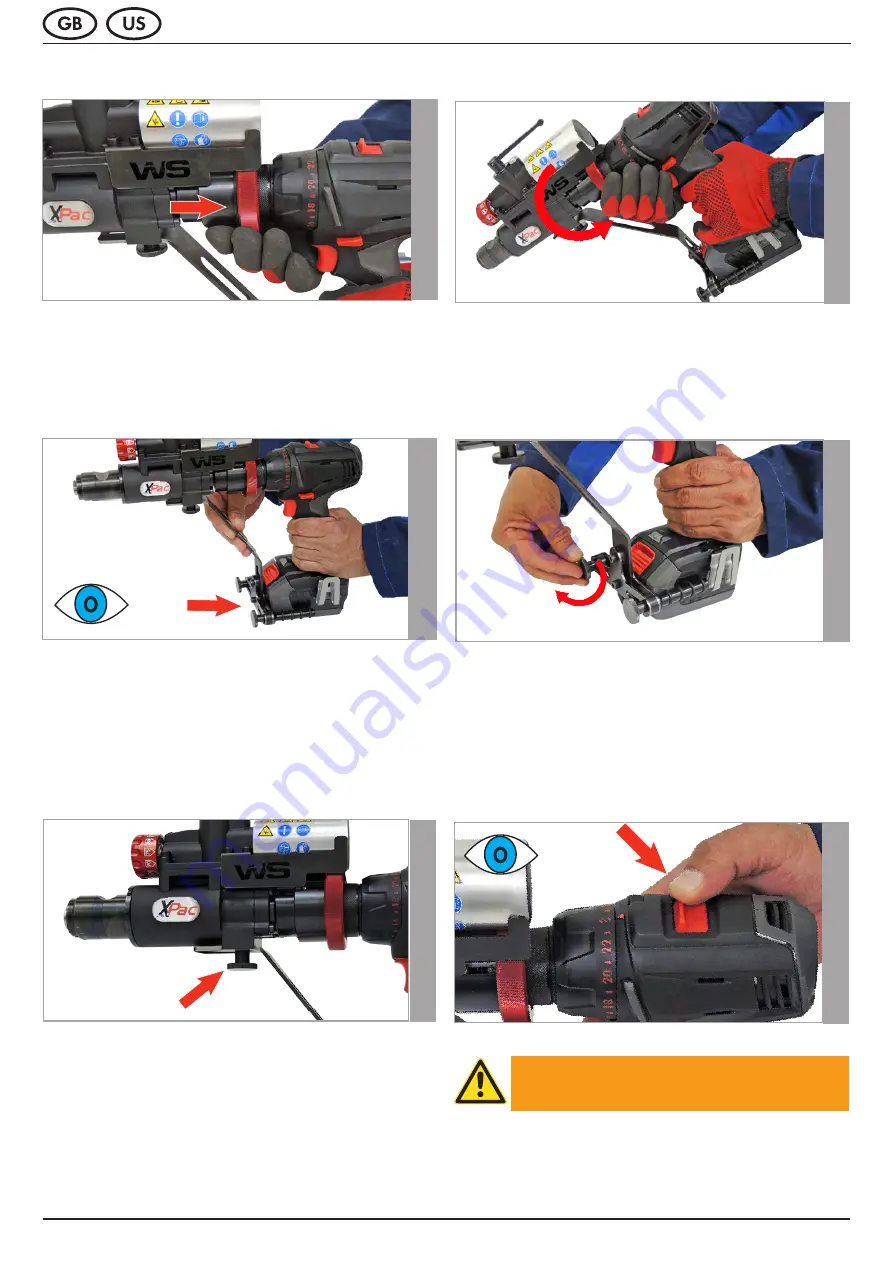
Bild 8
Bild von der XPress mit ausgeklapptem
Verriegelungshebel.
© Wieländer+Schill
10
Position the torque arm of the
XPac
on the cordless
screwdriver.
Position the support elements on the battery wit-
hout play and tighten the knurled screws.
Setting on the cordless screwdriver.
ATTENTION!
No impact function
Select second gear for all applications.
(fast forward)
Torque adjustment to maximum.
Push the locking ring backwards over the drill
chuck.
Tighten the locking ring with
left thread
firmly.
Also tighten the knurled screw of the torque arm at
the top of the
XPac
.
Abb. 3.1.h
Abb. 3.1.g
Abb. 3.1.j
Abb. 3.1.e
Abb. 3.1.f
Abb. 3.1.i