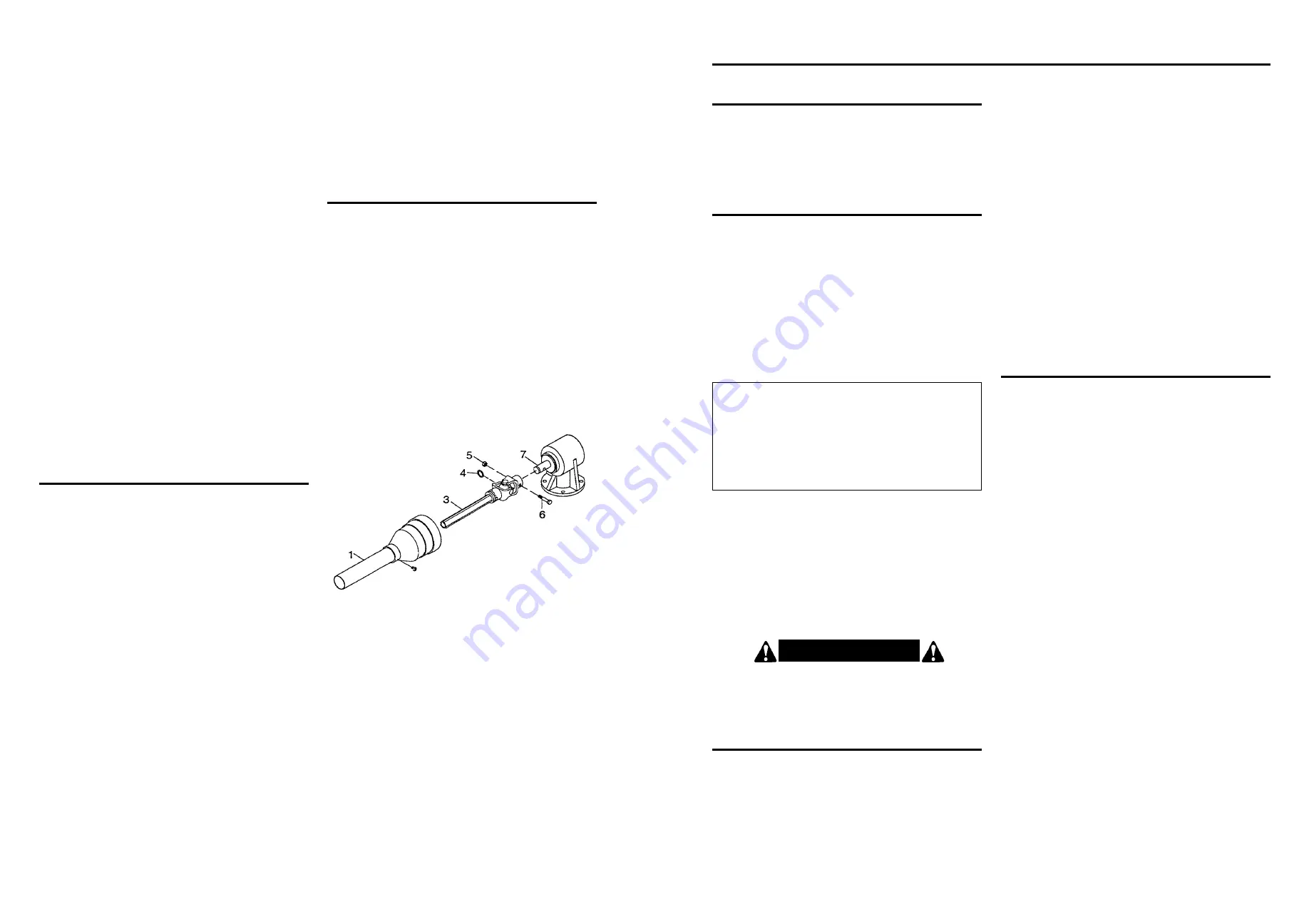
19
20
A T TA C H M E N T
The cutter is shipped partially assembled. Assembly will
be easier if components are aligned and loosely assem-
bled before tightening hardware. Recommended torque
values for hardware are located on page 26.
Select a suitable working area. Refer to illustrations,
accompanying text, parts lists and exploded view
drawings.
Complete check lists on page 20 when assembly is
complete.
Position cutter flat and cut the nylon straps that are
holding all loose parts to the cutter.
Rotate the “A” frame hitch forward and connect lift arms
and toplink.
Attach the two linkage lift straps to the cutter deck
(behind the gearbox) and to the end of the slack link on
the “A” frame. These bolted connections are moveable
joints – so tighten nylock nuts only until excess loose-
ness is gone.
Most swinging drawbars will have to be moved to a
forward position or removed. Check the tractor swing-
ing drawbar for interference with the front of the cutter
before attempting to lift the cutter with the 3-pt. hitch.
Tractor lift arm stabilizer bars or sway blocks must be
used to control side movement of the cutter. DO NOT
CONNECT THE PTO DRIVELINE AT THIS TIME.
Check your lift arm hydraulic controls. Be sure the
hydraulic 3-pt. hitch control is in the float position and the
draft control is turned off.
Adjust lower lift arm(s) to level cutter right to left. Refer
to tractor operator’s manual for instructions.
Cutting height is controlled with tractor 3-point arms,
and rear tailwheel adjustment.
PTO DRIVELINE INSTA L L AT I O N
Spray WD-40 into the yoke and wipe. This should
remove some of the paint and make it easier to slide the
yoke onto the input shaft of the gearbox.
Remove shearbolt and retaining ring (4) from gearbox
input shaft (3).
Grease the input shaft of the gearbox before installing
the PTO shaft. This reduces the chance of the PTO shaft
yoke from galling to the input shaft if the shear pin should
break.
Remove rear drive shield (1) from driveline. To remove,
turn each plastic clip
1
/
4
turn and then lift out. Then slide
rear shield so entire joint assembly is exposed. (Refer to
figure 5.)
To prevent seal damage, carefully push driveline onto
gearbox input shaft until it contacts gearbox housing.
Install retaining ring (4) and then pull driveline ahead.
NOTE: A grade 2 bolt must be used for the shear bolt
to provide gearbox protection.
Align the holes in the driveline yoke and gearbox input
shaft and install and tighten shear bolt (6) and nut (5).
Install rear drive shield to driveline.
Lubricate rear driveline half and install front driveline
half.
I N S T R U C T I O N S
(continued)
1. Drive shield
3. Input driveline shaft half
4. Retaining ring
5. Nut
6. Shearbolt grade 2
1
/
2
– 13 NC x 3” long
7. Gearbox
Figure 5. Shear Bolt Driveline Installation
Adjust the tailwheel and lift arms so the cutter is level.
Then raise the tractor lift very slowly, making sure that
the front drive shaft shield does not hit the front of the
cutter. If it does, damage will be done to the drive shaft
shield and, if interference is bad enough, it WILL also
damage the drive shaft itself.
NOTE: This type of damage is NOT covered under
warranty, as it is totally under the control and the
responsibility of the operator.
Use the lift control limiting stop on the tractor control
lever to limit the upward travel of the lever so the lift can-
not be raised high enough to cause contact between the
drive shaft shield and front shielding.
7. Check the swinging drawbar of the tractor and make
sure the PTO driveline assembly will not contact. The
swinging drawbar can be moved forward on some
tractors or it can be removed.
If the PTO driveline assembly contacts the swinging
drawbar, damage will occur to the driveshaft shield and
possibly the driveshaft itself. (NOT covered under
warranty.)
O P E R AT I N G I N S T R U C T I O N S
Safety is a primary concern in the design and
manufacture of our products. Unfortunately, our efforts
to provide safe equipment can be wiped out by a
single careless act of an operator.
It has been said, “The best safety device is an
informed, careful operator”. We ask you to be that
kind of an operator.
The designed and tested safety of this machine
depends on it being operated within the limitations as
explained in this manual. Be familiar with and follow all
safety rules in the manual, on the cutter and on the
tractor.
The safe operation of this machine is the responsibility of
the owner/operator. The operator should be familiar with
the cutter and tractor and all safety practices before start-
ing operation. Read the safety rules on pages 4 thru 14.
always tilt the cutter slightly lower in the front. This tilt
decreases horsepower requirements. When fine shred-
ding is desired, adjust cutter deck level or slightly lower.
This will keep the foliage under cutter until thoroughly
shredded. More power is required for shredding.
The cutting height is adjustable from 1 - 5 inches. To
adjust, proceed as follows:
A. Raise cutter off ground using tractor 3-point lift. Turn
off tractor engine, disengage PTO, set parking brake,
and remove key from ignition.
B. SECURELY BLOCK CUTTER.
C. Remove bolt securing tailwheel to adjusting strap.
D. Adjust tailwheel to desired position. Secure with bolt,
lockwasher and nut.
E. Lower cutter to work position.
F. Adjust tractor 3-point hitch top link so linkage lift straps
have a small amount of slack to allow cutter deck to
float during operation.
GEARBOX OIL FILL
NOTE: The gearbox is shipped WITHOUT lubricant, so it
will be necessary to fill is before use. With the gearbox in
a level position, fill to the side inspection hole with a good
90 wt. gear lubricant. Check often and add lubricant if
necessary.
A D J U S T I N G F O R W O R K
The cutter should be operated at the highest position
which will give desired cutting results. This will help pre-
vent the blades from striking the ground, reducing blade
wear and undue strain on the machine. For best results
G E N E R A L S A F E T Y
Only qualified people familiar with this manual should
operate this machine. Operator should wear hard hat,
safety glasses, and safety shoes. It is recommended
that tractor be equipped with Roll-Over Protective
System (ROPS) and a seat belt be used. Before begin-
ning operation, clear work area of objects that may be
picked up and thrown. Check for ditches, stumps, holes,
or other obstacles that could upset tractor or damage
cutter. Always turn off tractor engine, set parking brake,
lower cutter to ground and allow cutter blades to come to
a complete stop before dismounting tractor.
P R E - O P E R AT I O N C H E C K L I S T
(OWNER RESPONSIBILITY)
____ Review and follow safety rules and safety signs on
pages 4 through 16.
____ Check that cutter is properly and securely attached
to tractor.
____ Make sure driveline spring-activated locking pin or
locking balls operate freely and are seated firmly in
tractor PTO spline groove.
____ Lubricate all grease fitting locations. Make sure
PTO shaft slip joint is lubricated.
____ Check to be sure gear lube runs out the small
check plug on side of gearbox.
____ Check that all hardware is properly installed.
____ Check to ensure blades are sharp and secure and
cutting edge is positioned to lead in a counter-
clockwise rotation.
____ Check that all shields and guards are properly
installed and in good condition.
____ Check cutting height, front to rear attitude and top
link adjustment.
____ Place tractor PTO and transmission in neutral
before starting engine.
____ Set tractor PTO gear select lever for 540 rpm
operation.
____ Inspect area to be cut and remove stones,
branches or other hard objects that might be
thrown, causing injury or damage.
C A U T I O N !
Do not operate the PTO at other than the rated 540
RPM. Excessive speeds can cause breakage, thrown
objects, and potential injury.