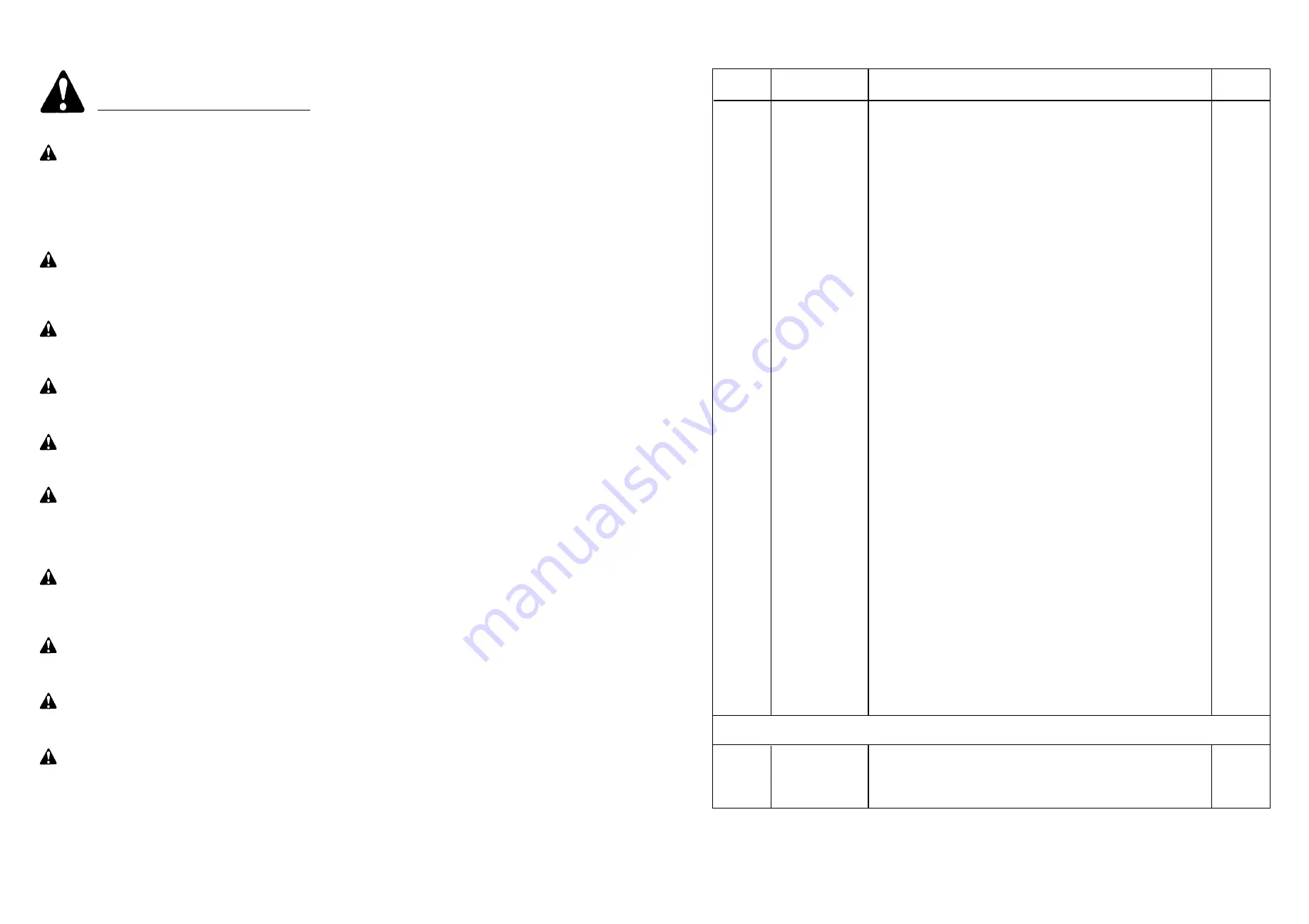
5
34
S A F E T Y I N S T R U C T I O N S
(continued)
Safety of the operator is one of the main concerns in designing and developing a new piece of equipment.
Designers and manufacturers build in as many safety features as possible. However, every year many
accidents occur which could have been avoided by a few seconds of thought and a more careful approach to
handling equipment. You, the operator, can avoid many accidents by observing the following precautions in
this section. To avoid personal injury, study the following precautions and insist those working with you, or for
you, follow them.
In order to provide a better view, certain photographs or illustrations in this manual may show an assembly
with a safety shield removed. However, equipment should never be operated in this condition. Keep all shields
in place. If shield removal becomes necessary for repairs, replace the shield prior to use.
To prevent injury or death, use a tractor equipped with a Roll-Over Protective System (ROPS). Do not paint
over, remove or deface any safety signs or warning signs on your equipment. Observe all safety signs and
practice the instruction on them.
Never exceed the limits of a piece of machinery. If its ability to do a job, or to do so safely, is in question –
DON’T TRY IT.
Do not modify the equipment in any way. Unauthorized modification may impair the function and/or safety and
could affect the life of the equipment.
In addition to the design and configuration of this implement, including Safety Signs and Safety Equipment,
hazard control and accident prevention are dependent upon the awareness, concern, prudence, and proper
training of personnel involved in the operation, transport, maintenance, and storage of the machine. Refer also
to Safety Messages and Operation Instructions in each of the appropriate sections of the Tractor and Cutter
Manuals. Pay close attention to the Safety Signs affixed to the Tractor and the Cutter.
Replace any CAUTION, WARNING, DANGER or instruction safety sign that is not readable or is missing.
Location of such safety signs is indicated in this booklet.
Never use alcoholic beverages or drugs which can hinder alertness or coordination while operating this
equipment. Consult your doctor about operating this machine while taking prescription medications.
Review the safety instructions with all users annually.
This equipment is dangerous to children and persons unfamiliar with its operation. The operator should be a
responsible adult familiar with farm machinery and trained in this equipment’s operations. Do not allow
persons to operate or assemble this unit until they have read this manual and have developed a
thorough understanding of the safety precautions and of how it works.
EQUIPMENT SAFETY GUIDELINES
REF.
PART
NO.
NO.
NO.
DESCRIPTION
REQ'D.
1
650351
Deck Weldment, SDM40-60
1
2
650440
Gearbox - Comer 135.800
1
3
2503175
Bolt, Hex
5
/
8
” - 11 NC x 1
3
/
4
”
4
4
2500083
Nut, Hex Vibration Proof
5
/
8
” - 11 NC
4
5
650395
Blade Holder Weldment
1
6
650425
Blade, Cutter SDM40-60/MDM70-60
2
7
650426
Blade Bolt, 1
1
/
8
”
2
8
650427
Lock, Washer, 1
1
/
8
” HD
2
9
650428
Nut, Hex Jam, 1
1
/
8
” - 12 UNF Gr. 8
2
10
650378
Sidebar, Toplink “A”
2
11
650379
Crossbar, Toplink “A”
1
12
650382
Linkage Lift Strap
2
13
650383
Tie Link, Toplink “A”
2
14
650384
Spacer
1
15
2503258
Bolt, Hex
3
/
4
” - 10 x 2.25 Gr. 5
2
16
2500037
Nut, Hex Nylock
3
/
4
” - 10 NC
2
17
590108
AK-578 Draw Pin
2
18
2503066
Bolt, Hex Head
5
/
8
” - 11 NC x 4”
1
19
2503154
Bolt, Hex
5
/
8
” - 11 NC x 1
1
/
2
”
6
20
2503152
Bolt, Hex Head
5
/
8
” - 11 NC x 2”
1
21
2500041
Nut, Hex Nylock
5
/
8
” - 11 NC
4
22
650416
A-Frame Weldment Tail Wheel
1
23
650412
Yoke Weldment
1
24
650480
Wheel Assembly - SDM40-60/72 Cutters
1
25
650386
Spindle Tube
1
26
2504179
Roll Pin
1
/
2
” x 2”
1
27
2503256
Bolt,
3
/
4
” - 10 NC x 7
1
/
2
” HH Gr. 5
1
28
2500002
Nut, Hex
3
/
4
” - 10 NC
1
29
2502001
Washer, Springlock
3
/
4
”
1
30
650387
Bar, Tail Wheel Adj.
1
31
2502007
Washer, Springlock
5
/
8
”
4
32
2500013
Nut, Hex
5
/
8
” - 11 NC
4
33
650460
PTO Assembly, SDM40-60
1
34
2503012
Bolt, Hex
1
/
2
” - 13 NC x 3” Grade 2
1
35
2502002
Washer, Springlock
1
/
2
”
1
36
2500003
Nut, Hex
1
/
2
” - 13 NC
1
37
2504201
Snap Ring 1
3
/
8
” Dia. SH-137
1
38
650451
Castle Nut M24 x 2
1
39
650468
Cotter Pin 5 x 50
1
40
650452
Bolt Washer 25 x 44 x 4
1
41
2504049
Drive Zerk
5
/
16
”
1
42
101101
Safety Sign - Warning (540 RPM)
1
43
101100
Safety Sign - Danger (Rotating Blades)
1
44
101103
Safety Sign - Danger (Keep Away) SW101
1
45
101157
Safety Sign - Warning (Prevent Serious Injury) M100
1
SDM40-72 (6’ CUTTER) PA RTS LIST
1
650601
Deck Weldment, SDM40-72
1
6
650430
Blade, Cutter SDM40-72/MDM70-72
2
12
650632
Linkage Lift Strap SDM40-72
2
33
650465
PTO Assembly, SDM40-72
1
SDM40-60 (5’ CUTTER) PA RTS LIST
and parts common to all models