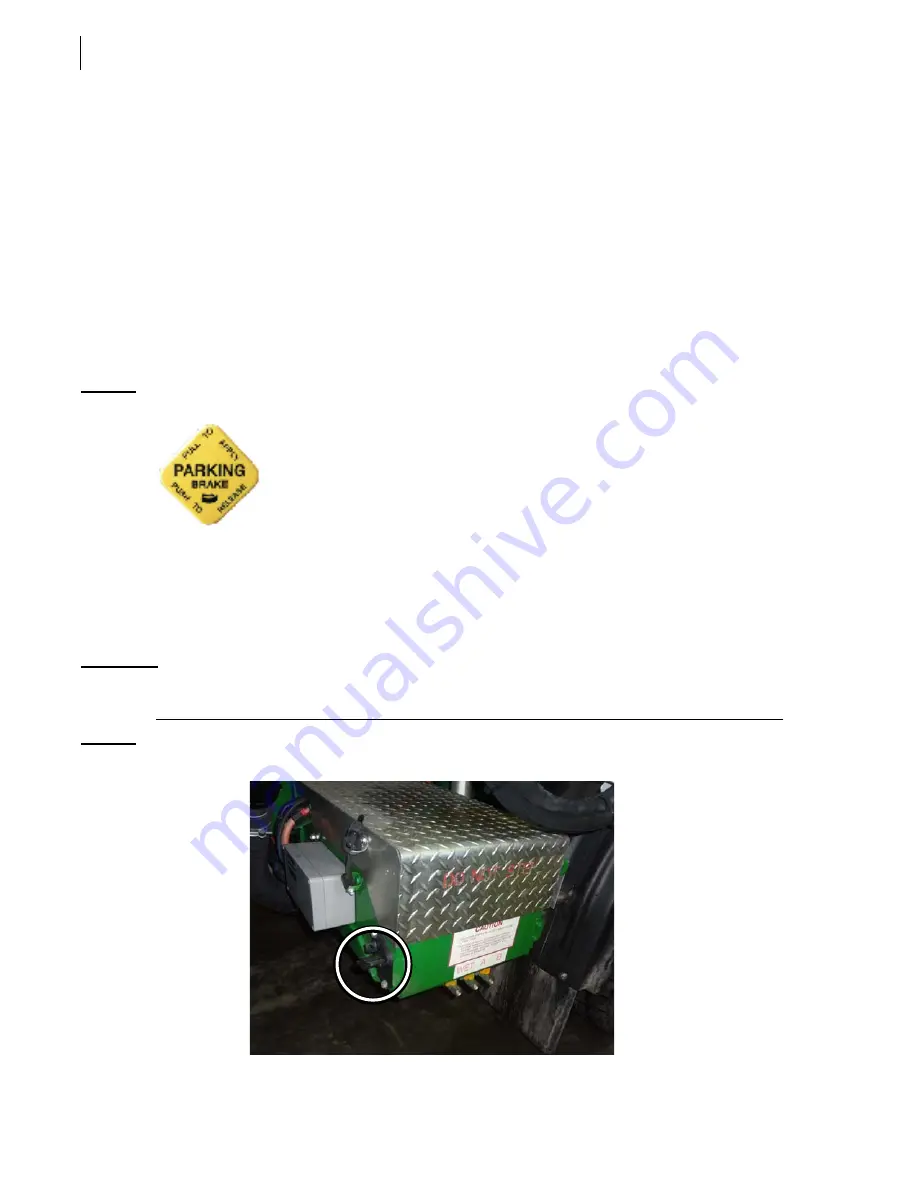
26
Safety
Cleanliness
Cleanliness is part of safety. Clean all the lights and safety decals so you and the surrounding
pedestrians and drivers will be aware of the truck at all times.
Locking Out and Tagging Out the Vehicle
For any inspection, repair or general maintenance being done on the vehicle, whether on the road or
at the shop, it is the employer’s responsibility to establish a proper lockout/tagout procedure and see
to the application of this procedure.
To lock out and tag out your W
ITTKE
T
WIN
A
UGER
™ vehicle:
1.
Park the vehicle on safe level ground, and apply the parking brake (see Figure 2-5).
Figure 2-5 Parking brake button
2.
Make sure the pod is empty.
3.
Switch OFF the hydraulic pump.
4.
Turn OFF the engine, remove the key from the ignition, store it in a safe and controlled area
(preferably on yourself), and tape over the ignition switch.
5.
Turn OFF and lock the master switch.
I
MPORTANT
:
The battery set of the W
ITTKE
T
WIN
A
UGER
™ is equipped with a master switch (see Figure 2-6) that
must be turned OFF.
Figure 2-6 Master switch
Summary of Contents for TWIN AUGER
Page 1: ...TWIN AUGER OPERATOR S MANUAL ...
Page 2: ......
Page 3: ...TWIN AUGER OPERATOR S MANUAL ...
Page 5: ......
Page 6: ......
Page 23: ...Safety 15 84466 190902 182922 120983 79014 ...
Page 24: ...16 Safety 84472 47256 84419 Spanish 32307 190901 Optional Optional ...
Page 25: ...Safety 17 97832 84447 159852 Optional Optional 179015 ...
Page 26: ...18 Safety 120557 121022 Spanish ...
Page 27: ...Safety 19 Decals on Chassis 188649 32411 Optional 190900 ...
Page 29: ...84001 120972 120975 32272 84368 84002 47420 84420 Safety 21 ...
Page 30: ...22 Safety 173657 84303 84327 79891 183198 ...
Page 37: ...Safety 29 Figure 2 10 Hydraulic pump ON OFF switch ...
Page 38: ...30 Safety ...