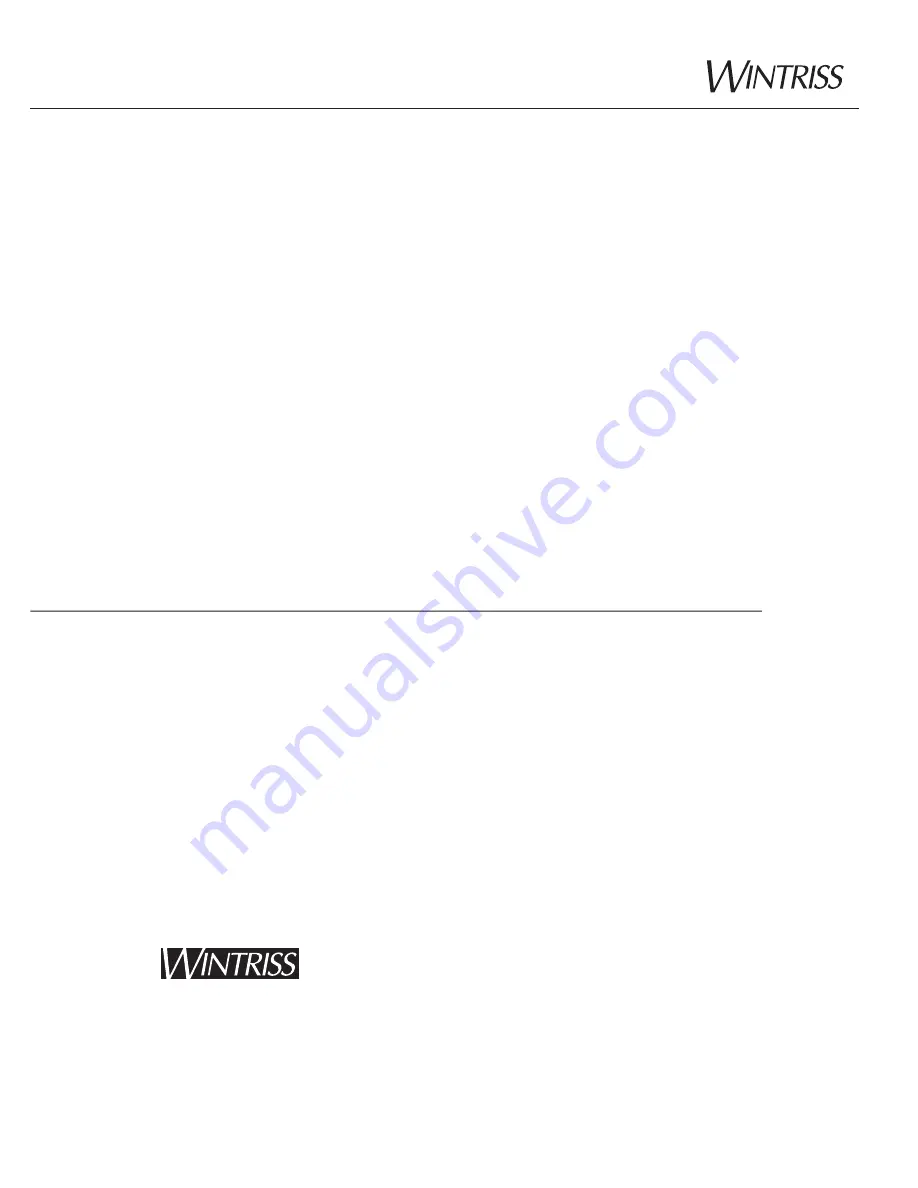
WPC 1000
®
Wintriss Clutch/Brake Control
1125100
Rev. R August 2015
UserUser
User
ManualManualManual
User
Manual
Tech Support Hotline 800-586-8324 8-5 EST
www.wintriss.com
®
®
Wintriss Controls Group, LLC
100 Discovery Way
Unit 110
Acton MA 01720 USA
Phone (800) 586-8324
Fax (978) 263-2048
PRINTED IN USA DA69447
Summary of Contents for WPC 1000
Page 17: ...1125100 WPC 1000 User Manual xii Table of Contents ...
Page 99: ...1125100 WPC 1000 User Manual 2 72 Installation ...
Page 207: ...1125100 WPC 1000 User Manual A 18 Extracts from OSHA and ANSI ...
Page 217: ...1125100 WPC 1000 User Manual G 6 Glossary ...
Page 223: ......
Page 224: ......
Page 225: ......
Page 226: ......
Page 227: ......
Page 228: ......
Page 229: ......
Page 230: ......
Page 231: ......
Page 232: ......
Page 233: ......
Page 234: ......
Page 235: ......