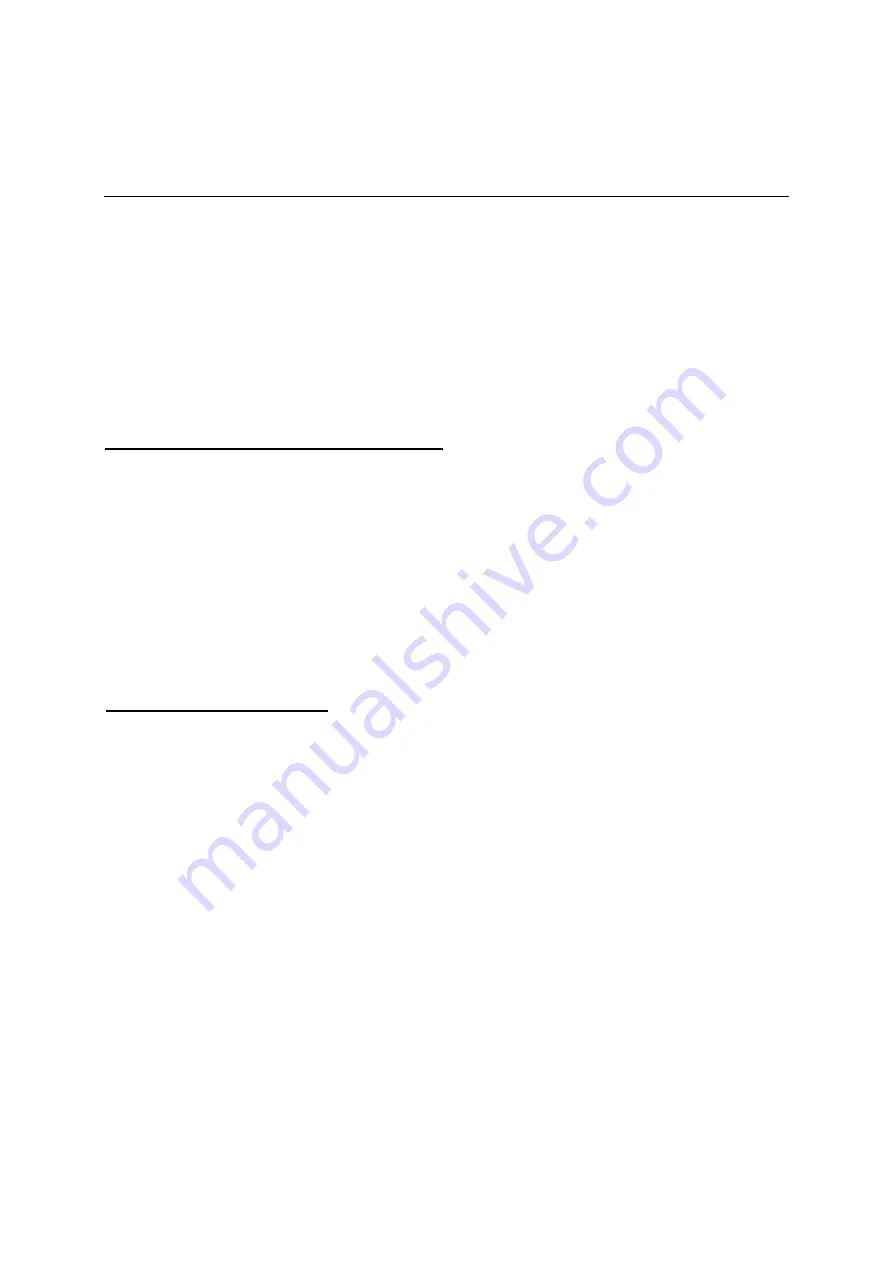
WORKSHOP MANUAL
Winget Mechanically Fed Mixers
Models: 200TM
From 1998
Refer to the Drum Adjustment illustration and check the number of flat washers
required to fill the gap
(G)
between the flange and base block. Remove one washer
from each side. Apply anti-seize compound to the setscrews
(H)
and pass the
setscrews through the flange and flat washers, fully tighten the setscrews into the
trunnion.
Check for free play between the drum bevel gear and bevel pinion
(C)
by gently
rocking the drum (approximately
3
mm is acceptable).
By using a combination of the
varying thickness of washers and shims it is possible to fine tune the backlash.
Remove the lifting equipment.
Tilting Handwheel and Locking Plunger
The tilting handwheel wheel is secured to the tilting pinion via a feather key and M10
grubscrew. With the drum in the vertical position slacken and remove the grub
screw, pull off the handwheel. Note on mixers, which have been in service for some
time it may be necessary to use a suitable puller on the handwheel.
The locking Plunger is held in place in the Tilting Wheel by a small spiral pin. Knock
out this pin and remove the locking plunger.
Re-assemble in the reverse order coating the locking plunger and pinion shaft with
anti-seize compound.
Tilting Bracket and Pinion
With the Drum in the vertical position remove the lower tilting pinion guard. Remove
the four setscrews securing the tilting bracket taking care not to drop the retaining
plate on the inside of the mainframe front leg. Lift the pinion teeth clear of the tilting
chain, remove the inner retaining bracket and lift out the tilting bracket assembly.
Remove the handwheel as described above, remove the feather key and using a soft
faced hammer knock the tilting shaft and pinion out of the bracket. Check the
condition of the bushes and replace and/or lubricate as required. Note, very
occasionally new bushes will require reaming to size.
Reassemble the tilting bracket in reverse order lubricating bushes with engine oil.
Coat shafts, pinions and plungers with anti-seize compound.
When refitting the tilting bracket assembly to the mixer engage and lock the plunger
into the lower single hole in the bracket whilst ensuring the drum is still vertical.
Pass the assembly through the front leg of the mainframe, slip the retaining plate
over the bracket before engaging the pinion into the tilting chain.
Align the bracket and inner retaining plate with the slots in the front leg and insert the
setscrews and washers. Finger tighten the setscrews to hold the bracket in place and
slide the assembly in the slots to correctly tension the tilting chain, fully tighten the
four setscrews. Refit the lower tilting pinion guard.
Summary of Contents for 200TM
Page 3: ...WORKSHOP MANUAL 200TM SECTION 1 INTRODUCTION...
Page 6: ...WORKSHOP MANUAL 200TM SECTION 2 REPAIR SERVICE PROCEDURES...
Page 12: ...200TM DRUM ADJUSTMENT...
Page 42: ...WORKSHOP MANUAL 200TM SECTION 3 GENERAL ARRANGEMENT DIMENSIONS...
Page 43: ...GENERAL ARRANGEMENT...
Page 44: ...DIMENSIONS...
Page 45: ...WORKSHOP MANUAL 200TM SECTION 4 SERVICE SCHEDULES LUBRICATION DIAGRAM...
Page 48: ...LUBRICATION POINTS...
Page 49: ...LUBRICANTS...
Page 50: ...WORKSHOP MANUAL 200TM SECTION 5 HYDRAULIC CIRCUIT DIAGRAMS...
Page 51: ...200TM LATER BASIC HYDRAULIC CIRCUIT...
Page 52: ...200TM LATER DRAGLINE BATCHWEIGER HYDRAULIC CIRCUIT...
Page 53: ...WORKSHOP MANUAL 200TM SECTION 6 WIRING DIAGRAMS...
Page 59: ...Hourmeter lamp dwg 04 03 02 12 50 36 Scaled to fit...
Page 60: ...Hourmeter no lamp dwg 04 03 02 12 53 33 Scaled to fit...
Page 62: ...WORKSHOP MANUAL 200TM SECTION 7 NOISE LEVELS...
Page 64: ...WORKSHOP MANUAL 200TM SECTION 8 SPECIAL TOOLS...
Page 65: ...200TM PUNCH VALVE SEAT 200TM SPECIAL TOOL V2003698 CASE HARDEN TO 45 50 ROCKWELL...
Page 66: ...200TM DRUM BLADE DRILLING GUIDE SPECIAL TOOL 200TM 513360100...
Page 67: ...200TM SPECIAL TOOLS...
Page 68: ...1 513204000 CLAMP DRUM CLIP 1 2 V2003698 PUNCH BLEED VALVE SEAT 1 200TM SPECIAL TOOLS...
Page 69: ...WORKSHOP MANUAL 200TM SECTION 9 HYDRAULIC CONTROL VALVE SERVICE MANUAL...
Page 70: ...PAGE INTENTIONALLY BLANK...
Page 71: ...WORKSHOP MANUAL 200TM SECTION 10 PARTS LISTINGS...
Page 73: ...200TM MAINFRAME AXLES AND STABILISERS...
Page 90: ...200TM 415 VOLT START STOP SWITCH STAR DELTA...
Page 92: ...200TM 415 VOLT START STOP SWITCH DIRECT ON LINE...
Page 98: ...200TM HOPPER...
Page 110: ...200TM WATER TANK FIT SPECIAL WASHER V2004220 BETWEEN ITEMS 11 12...
Page 114: ...200TM DYNAMO AND MOUNTING LISTER PETTER TS1 HS...
Page 118: ...200TM DRAGLINE ASSEMBLY...
Page 120: ...200TM DRAGLINE ASSEMBLY...
Page 124: ...200TM DRAGLINE SHOVEL...
Page 126: ...200TM DRAGLINE FEEDAPRON...
Page 130: ...200TM LISTER PETTER TS1 ELECTRIC START...
Page 132: ...200TM DECALS AND LOGOS 1 2 3 4 5 6 7 8 9 10 11 12 13 14 15 16 17 18 19 20 21 22...
Page 134: ...200TM DECALS AND LOGOS 23 24 25 26 27 28 29...
Page 135: ...200TM SPECIAL TOOLS...
Page 136: ...1 513204000 CLAMP DRUM CLIP 1 2 V2003698 PUNCH BLEED VALVE SEAT 1 200TM SPECIAL TOOLS...
Page 137: ...WORKSHOP MANUAL 200TM SECTION 11 BATCHWEIGHER MAINTENANCE INSTRUCTIONS...
Page 138: ...MAINTENANCE INSTRUCTIONS HYDRAULIC WEIGHING UNITS WWW WINGET CO UK...
Page 140: ......
Page 141: ......
Page 142: ......
Page 143: ......
Page 144: ......
Page 145: ......
Page 146: ......
Page 147: ......