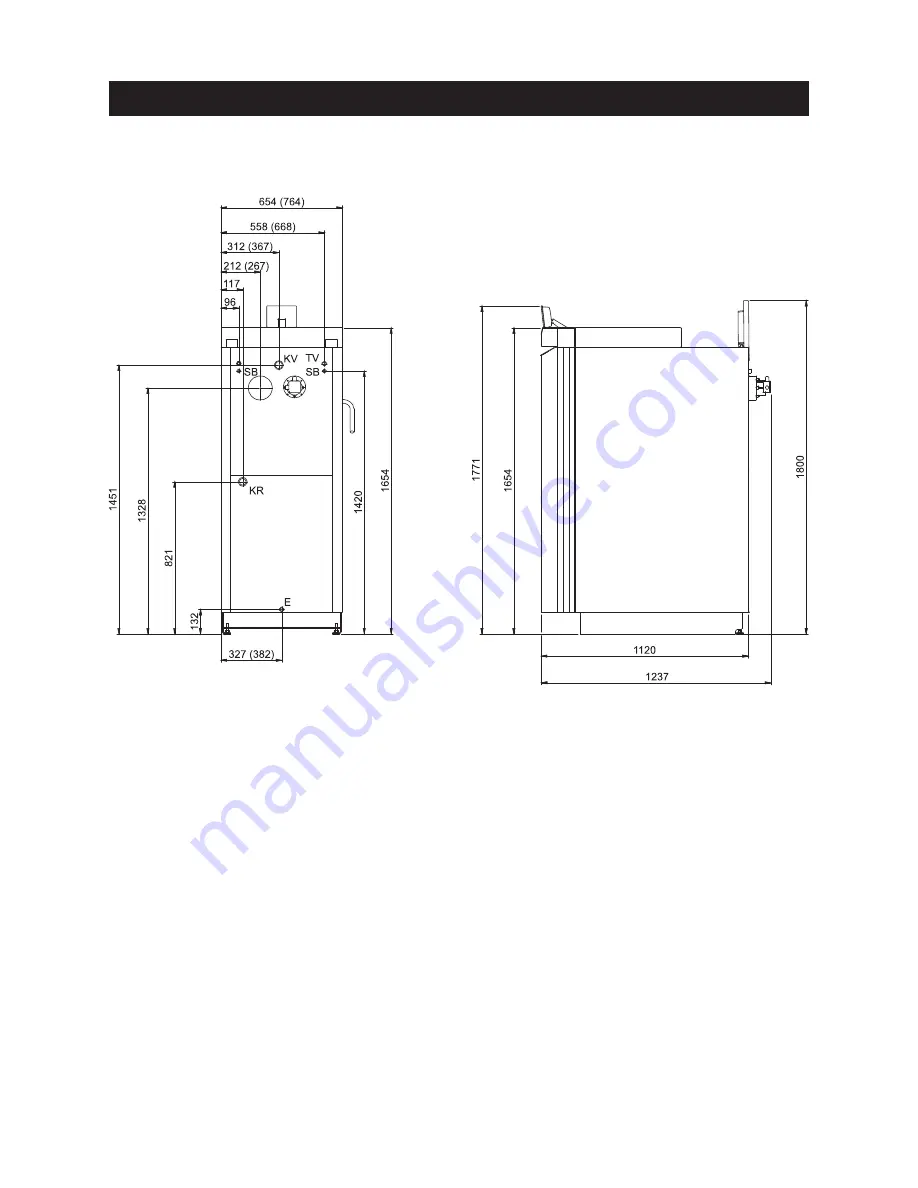
7
2.3 Dimensional sketches
Fig. 5
Rear view
Fig. 6
Left view
KV . . . . .Boiler feed (5/4” pipe)
KR . . . . .Boiler return (5/4” pipe)
TV . . . . .Thermal valve sensor (1/2” sleeve)
SB . . . . .Thermal safety device (1/2” tube)
E . . . . .Discharge
For the Installer
2)
All dimensions in mm:
Details provided in brackets apply to
LPW 360 and 500.
2) with cleaning cover open