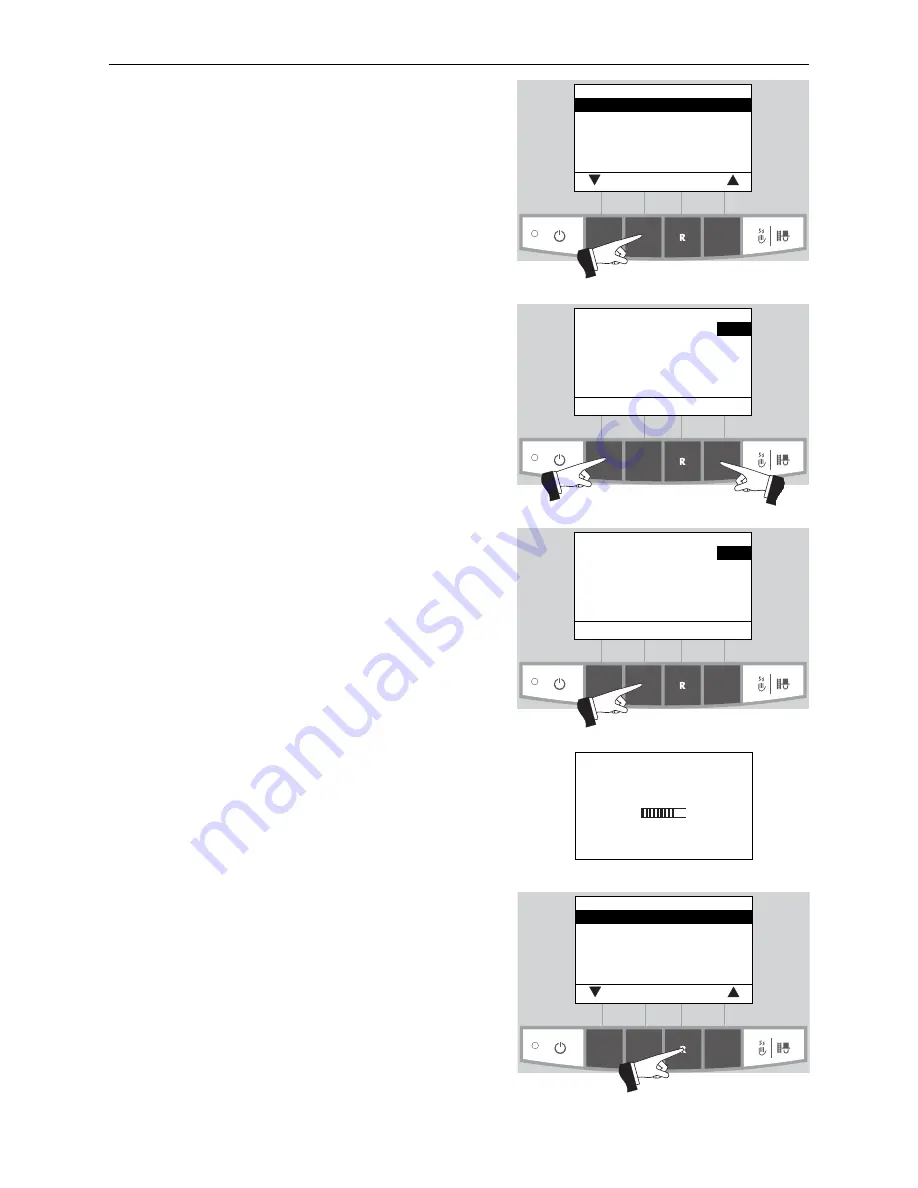
34
2.
Operation
Fig. 61
Boiler cleaning
Time
Feed operating mode
Time profile feed
Probe switching
choose
back
Confirm the selected sub-menu “Time” by pressing the
choose
button – Fig. 61.
Fig. 62
Time
13:50
–
save
back
+
Use the
+
or
–
button to set the required time – Fig. 62.
Exit the menu or sub-menu by pressing the
back
button
(Fig. 65) or by waiting 10 minutes.
Fig. 63
Time
13:50
–
save
back
+
Confirm the changed time by pressing the
save
button –
Fig. 63.
The display will show “Parameter is saved” for a few
seconds (Fig. 64) and then return to the previous screen –
Fig. 65.
Fig. 64
Parameter is saved
(Animated symbol)
Fig. 65
Boiler cleaning
Time
Feed operating mode
Time profile feed
Probe switching
choose
back