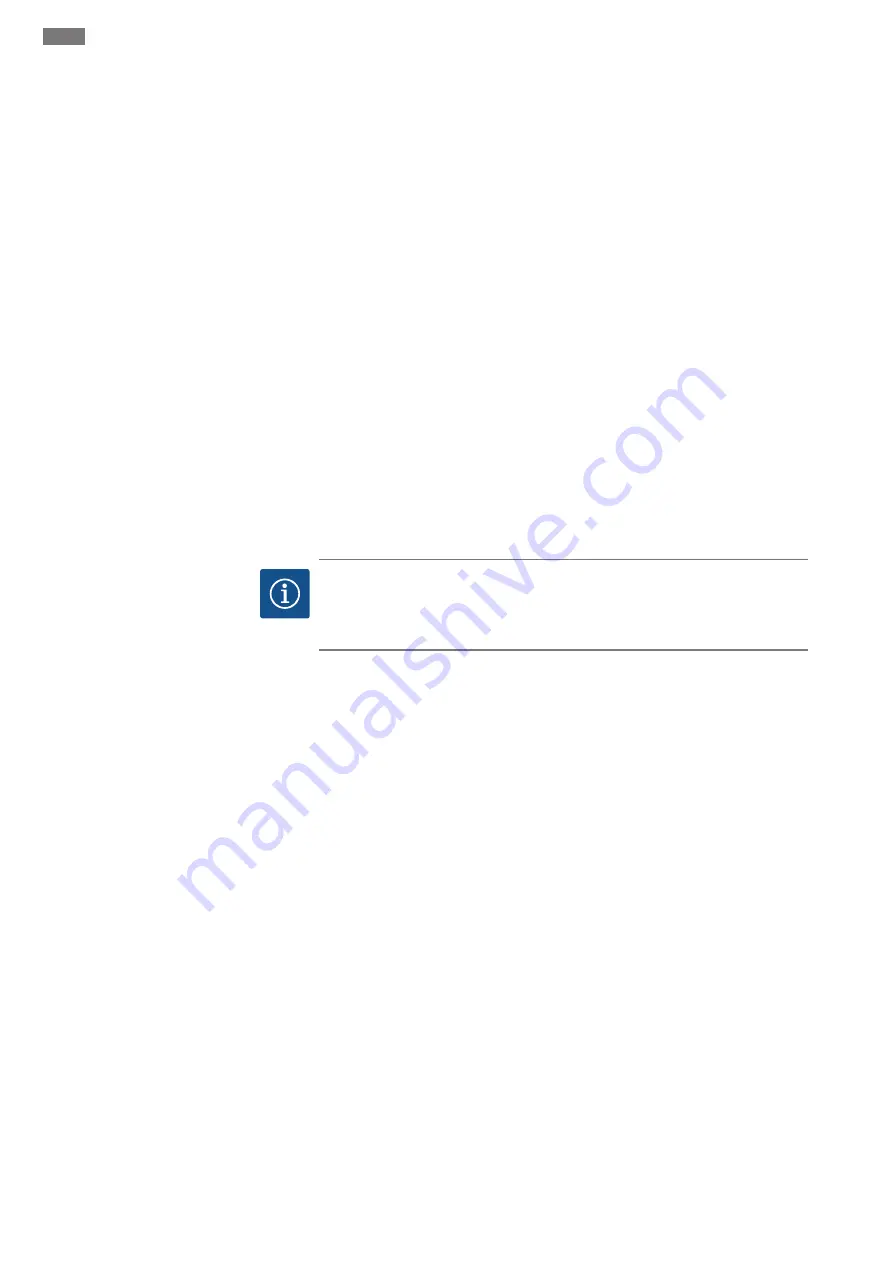
en
Maintenance
60
WILO SE 2022-06
9.
Unscrew the interior hexagonal head screws (locking pins) one after the other until
the head is countersunk half way into the cover collar (Fig. II or Fig. III depending on
the pump type).
10. Unscrew all four cover screws (Fig. IV).
11. Screw in two of the cover screws up to the stop into the press-off drilled holes to
press the cover out of its seat (Fig. IV/V).
12. Unscrew one of the coupling screws and turn it all the way into one of the installa-
tion drilled holes (Fig. VI, item 1). To do this, the coupling half is fixed by the re-
taining washer (Fig. VI, item 3) at the impeller shaft.
13. Unscrew the remaining coupling screws and take off the loose coupling half. If
need be, use the provided press-off drilled holes (Fig. VI, item 4). The impeller shaft
is now held up by the retaining washer (Fig. VII, item 1).
14. Unscrew the hexagon head screw (Fig. VII, item 2) at the motor shaft to lower the
retaining washer (Fig. VII, item 1), thereby lowering the impeller/impeller shaft
(Fig. VII, item 3). When the impeller has been completely lowered (Fig. VIII, after a
travel of about 5 mm), completely take out the hexagon head screw and the re-
taining washer.
15. Unscrew the coupling screw out of the installation drilled hole and remove the re-
maining coupling half (Fig. IX). If need be, use the provided press-off drilled holes.
16. Unscrew the central screw (Fig. X, item 2) of the impeller shaft and remove it with
the retaining washer (Fig. X, item 3).
17. Take out both impeller shaft keys (Fig. X, item 1).
18. Carefully pull off and remove the mechanical seal (Fig. XI) from the impeller shaft.
Installation
NOTICE
Thoroughly clean the sliding/seat surfaces of the impeller shaft and the lantern. If
the shaft is damaged, it must be replaced. Always use new screws for the twist
guard. Replace the O-rings in the cover groove and in the shaft sleeve groove.
1.
Completely screw in a cover screw (Fig. XII, item 1) into each of the two press-off
drilled holes of the cover.
2.
Be sure that all interior hexagonal head screws (locking pins) are countersunk half
way into the cover collar (Fig. XII).
3.
Put the mechanical seal onto the impeller shaft in such a way that the four drilled
holes for the cover screws are opposite the threads (Fig. XIII). Attention: If the
drilled holes of the locking pins are not arranged at 90° to each other, pay attention
to the installation position. The drilled holes must point towards the lantern win-
dow to facilitate accessibility of the grub screws (Fig. II or Fig. III, depending on the
pump type). Push the mechanical seal on until the forcing screws are on the hous-
ing. A commercially available dishwashing liquid can be used as a lubricant.
4.
Check the keys in the motor shaft for correct seating.
5.
Push the motor shaft retaining washer on and fix with central screw (Fig. XIV). En-
sure that the motor shaft retaining washer is well seated when the central screw is
completely screwed in and that the central screw thread bears at least 12 mm in
the motor shaft thread in this position. In case necessary, use the supplied washers.
6.
By unscrewing the central screw, lower the retaining washer of the motor shaft by
about 5 mm (Fig. XIV).
7.
Put the first key (Fig. XV, item 1) in the impeller shaft, put on the retaining washer
(Fig. XV, item 2) of the impeller shaft and screw in the hexagon head screw (Fig. XV,
item 3)
by hand
.
8.
Rotate the motor shaft so that the motor shaft key and impeller shaft key are op-
posite each other.
9.
Put the first coupling half on the two keys and the retaining washers (Fig. XVI).
10. Align the threaded hole in the impeller shaft retaining washer to the installation
drilled hole of the coupling half.
11. Insert one of the coupling screws into the installation drilled hole and screw in half
way (Fig. XVII).
Summary of Contents for Atmos GIGA-B
Page 2: ......
Page 3: ...Unmounting the mechanical seal Fig I Fig II 2 1 1 1 Fig III Fig IV 50 Fig V Fig VI 4 4 1 2 3...
Page 4: ...Fig VII Fig VIII 2 1 3 Fig IX Fig X 3 2 1 Fig XI...
Page 5: ...Mounting the mechanical seal Fig XII Fig XIII 1 Fig XIV Fig XV 1 2 3 Fig XVI Fig XVII...
Page 6: ...Fig XVIII Fig XIX 1 2 1 Fig XX Fig XXI Fig XXII Fig XXIII 1 1 2...
Page 7: ...Exchange of Motor Fig XXIV Fig XXV 1 8x Fig XXVI Fig XXVII Fig XXVIII...
Page 10: ......
Page 11: ...11 Chinese simplified 12 English 37...
Page 13: ...zh CHS Wilo Atmos GIGA I B 13 1 1 1 1 2 WILO SE 2022 1 3 Wilo 2 2 1 2 2...
Page 14: ...zh CHS 14 WILO SE 2022 06 2 3 RCD 2 4 2 5 2 6...
Page 15: ...zh CHS Wilo Atmos GIGA I B 15 2 7 2 8 IEC VDE 8 3 3 1 3 2 3 3 Wilo...
Page 16: ...zh CHS 16 WILO SE 2022 06 3 4 30 kg 30 Atmos GIGA B...
Page 17: ...zh CHS Wilo Atmos GIGA I B 17 4 4 1 Atmos GIGA I Atmos GIGA D Atmos GIGA B 4 2...
Page 21: ...zh CHS Wilo Atmos GIGA I B 21 1 Qmin Qmin Qmin 10 x Qmax 7 4 Wilo 200 mm...
Page 24: ...zh CHS 24 WILO SE 2022 06 r 5 x DN d s r 2 5 d 2s Fig 4 3 4 8 5 8...
Page 27: ...zh CHS Wilo Atmos GIGA I B 27 Wilo 9 1 9 2 1 2...
Page 28: ...zh CHS 28 WILO SE 2022 06 2 Fig 7 NPSH NPSH 1 L1 L2 V1 V2 W1 W2 9 3 9 4 9 5...
Page 29: ...zh CHS Wilo Atmos GIGA I B 29 3 Fig 8 10 10 Wilo...
Page 30: ...zh CHS 30 WILO SE 2022 06 10 1 10 2 10 2 1 Wilo 1 2 3 4...
Page 34: ...zh CHS 34 WILO SE 2022 06 Wilo PTC 40 C Wilo 6 12 Wilo...
Page 36: ...zh CHS 36 WILO SE 2022 06 13 2 www wilo recycling com...
Page 67: ......