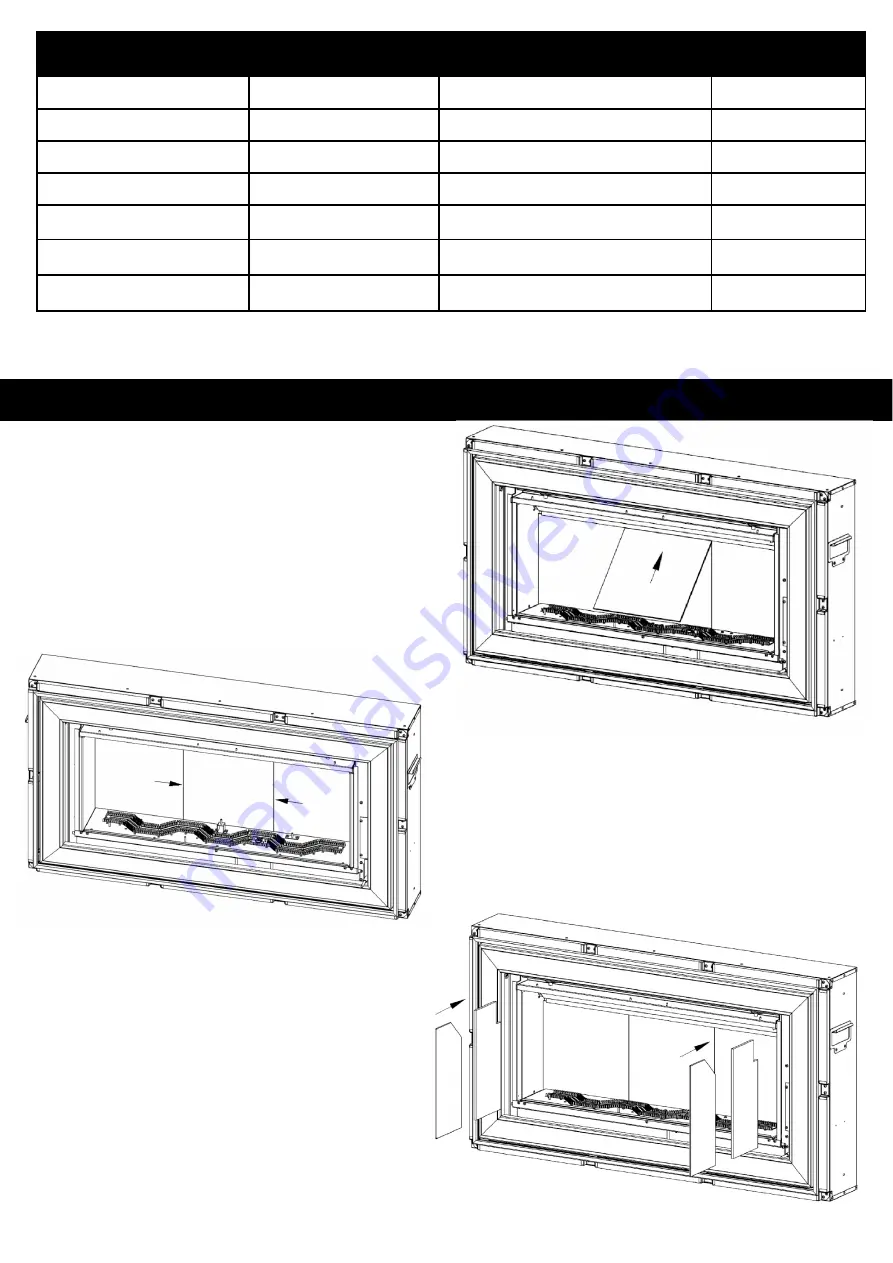
18
* The wall depth is calculated as the distance from the front face of the inside wall (or
from front face of slips if fiMed) to the outside face of the exterior wall.
FIT THE REAR/SIDE GLASS FITTING
1.
The rear and side black glass panels are supplied
in a cardboard pack. Carefully unpack the glass
panels and install as shown in the 3 diagrams.
Ensure the smooth face of the glass pane is
facing outwards when fi8ng them into the
appliance.
Fit the 3 rear panels first by pushing the upper
edge into the rear upper slot and liing unl it
will rotate inwards and sit down on its lower
edge.
3.
Finally, fit the side glass panels and side
liners as shown here. Slide the liner in
first and then slide the glass side panel in
unl it touches the rear glass panels.
2.
Ensure the three panels are pushed together so
there is no gap between the panels. Gaps
between the panels are not covered under
warranty so ensure that these are fiMed
correctly before proceeding.
Appliance Data
Gas Type
Natural Gas
Ba8ery Type (Electronic Igniter)
AA
Inlet Pressure
20mbar
±
1mbar
Wall Depth (Min)*
270 mm
Gas Connec:on
8mm pipe
Wall Depth (Max)*
725 mm
Injector (2 off)
Ø 1.37
Fire Depth
186mm
Pilot
P-XX1317
NOx Class
Class 5
Input High Rate (Gross)
6.0kW (0.57m
3
/hr)
Efficiency Class
Class 1
Input Low Rate (Gross)
2.9kW (0.27m
3
/hr)