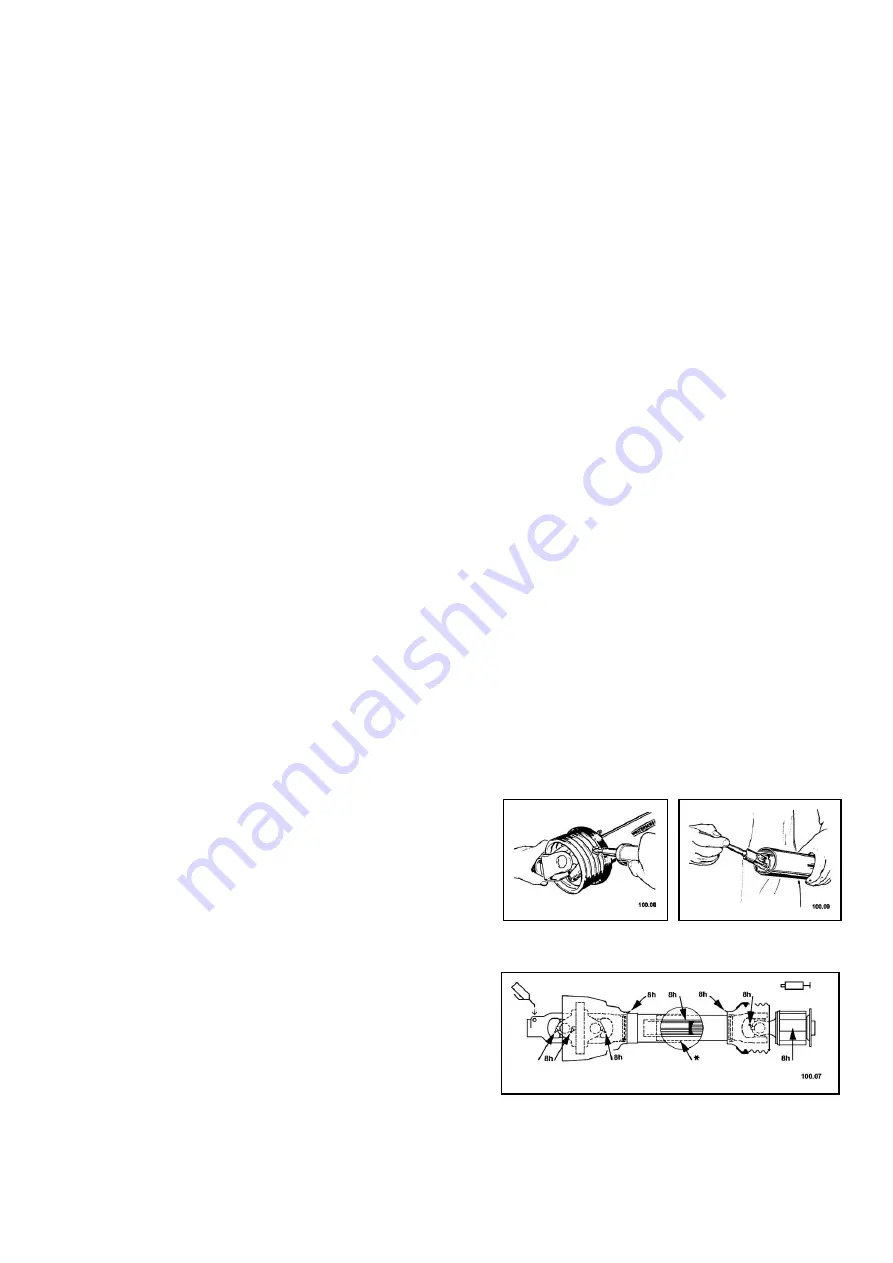
All information, illustrations and specifications in these operating instructions are based on the latest information available at the time of
publication. We reserve the right to make design changes at any time without prior notification
59
8.0. Maintenance
8.8. Lubrication
– General Information
The engine must be shut off
and the ignition key must be
removed for all lubrication
work.
Where required, lubricate
more often than specified.
Always keep all exposed
machine parts, threaded
spindles and guides lightly
lubricated.
Clean grease nipple before
lubrication.
Clean up leaking grease.
Before starting the machine
after a longer standstill,
lubricate and maintain the
entire machine.
8.8.1. Lubrication (daily)
Clean the profile pipes and
protective pipes if they are
contaminated.
Grease the inside of the
outer sliding profile.
The points indicated in the
figure by the arrows must be
lubricated daily.
Clean and lubricate the
universal-joint shaft before
any long shutdown period.