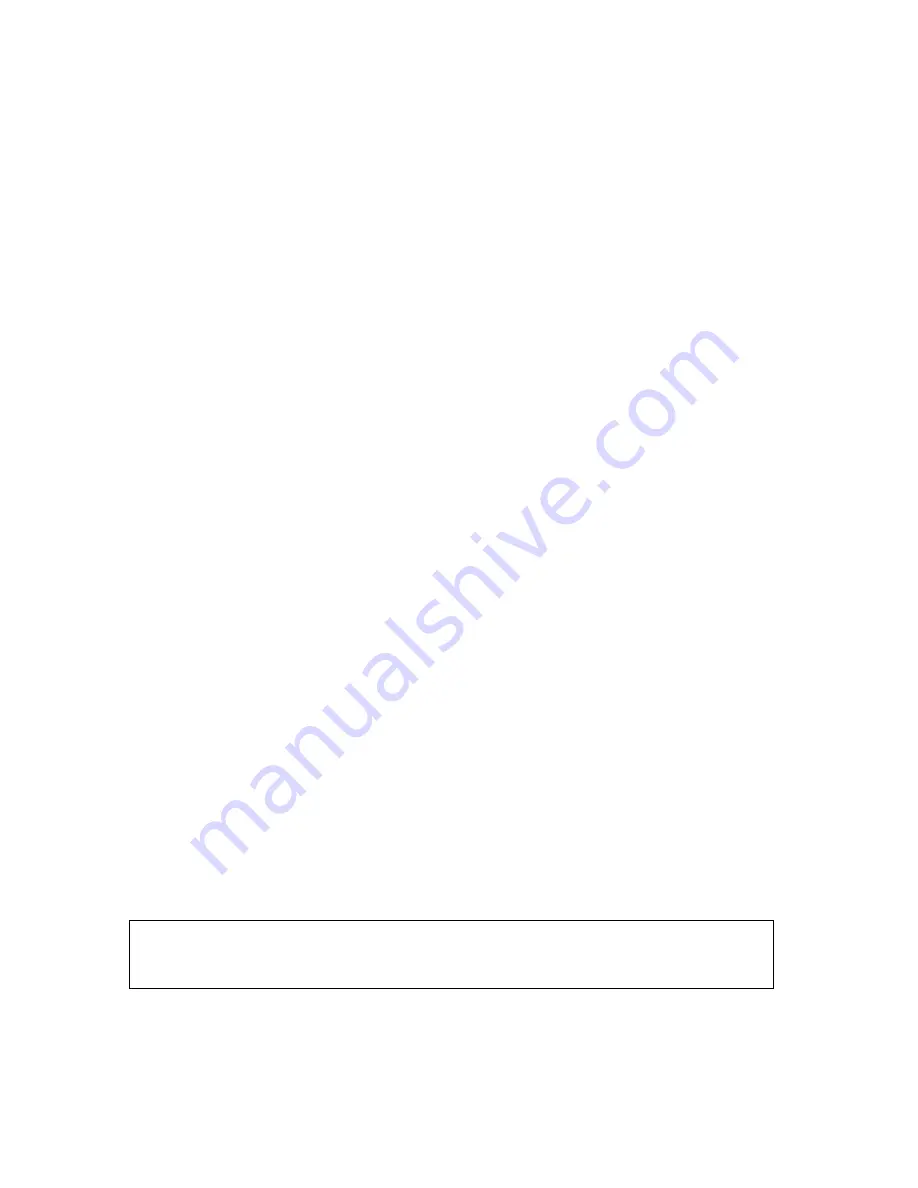
- ii -
WHIRLPOOL CORPORATION assumes no responsibility for any repairs made
on our products by anyone other than Authorized Service Technicians.
FORWARD
This Whirlpool Job Aid, “Polara
™
Refrigerated Range,” (Part No. 8178194), provides the technician
with information on the installation, operation, and service of the Polara
™
Refrigerated Range. It
is to be used as a training Job Aid and Service Manual. For specific information on the model being
serviced, refer to the “Use and Care Guide,” or “Tech Sheet” provided with the refrigerated range.
The Wiring Diagram and Strip Circuits used in this Job Aid are typical and should be used for
training purposes only. Always use the Wiring Diagram supplied with the product when servicing
the unit.
GOALS AND OBJECTIVES
The goal of this Job Aid is to provide detailed information that will enable the service technician to
properly diagnose malfunctions and repair the Whirlpool Polara
™
Refrigerated Range.
The objectives of this Job Aid are to:
• Understand and follow proper safety precautions.
• Successfully troubleshoot and diagnose malfunctions.
• Successfully perform necessary repairs.
• Successfully return the refrigerated range to its proper operational status.
Copyright © 2002, Whirlpool Corporation, Benton Harbor, MI 49022
Summary of Contents for Polara GR556LRK
Page 12: ...1 8 NOTES ...
Page 20: ...2 8 NOTES ...
Page 24: ...3 4 NOTES ...
Page 72: ...5 12 NOTES ...
Page 76: ...6 4 NOTES ...
Page 78: ...7 2 STRIP CIRCUITS CONTROL PANEL CLOCK ON CONTROL PANEL COOLING FAN MOTOR OVEN LIGHT BROIL ...
Page 79: ...7 3 BAKE CONVECTION BAKE ACCUSIMMER ...
Page 85: ...8 5 NOTES ...
Page 86: ...8 6 NOTES ...
Page 88: ...CORPORATION ...