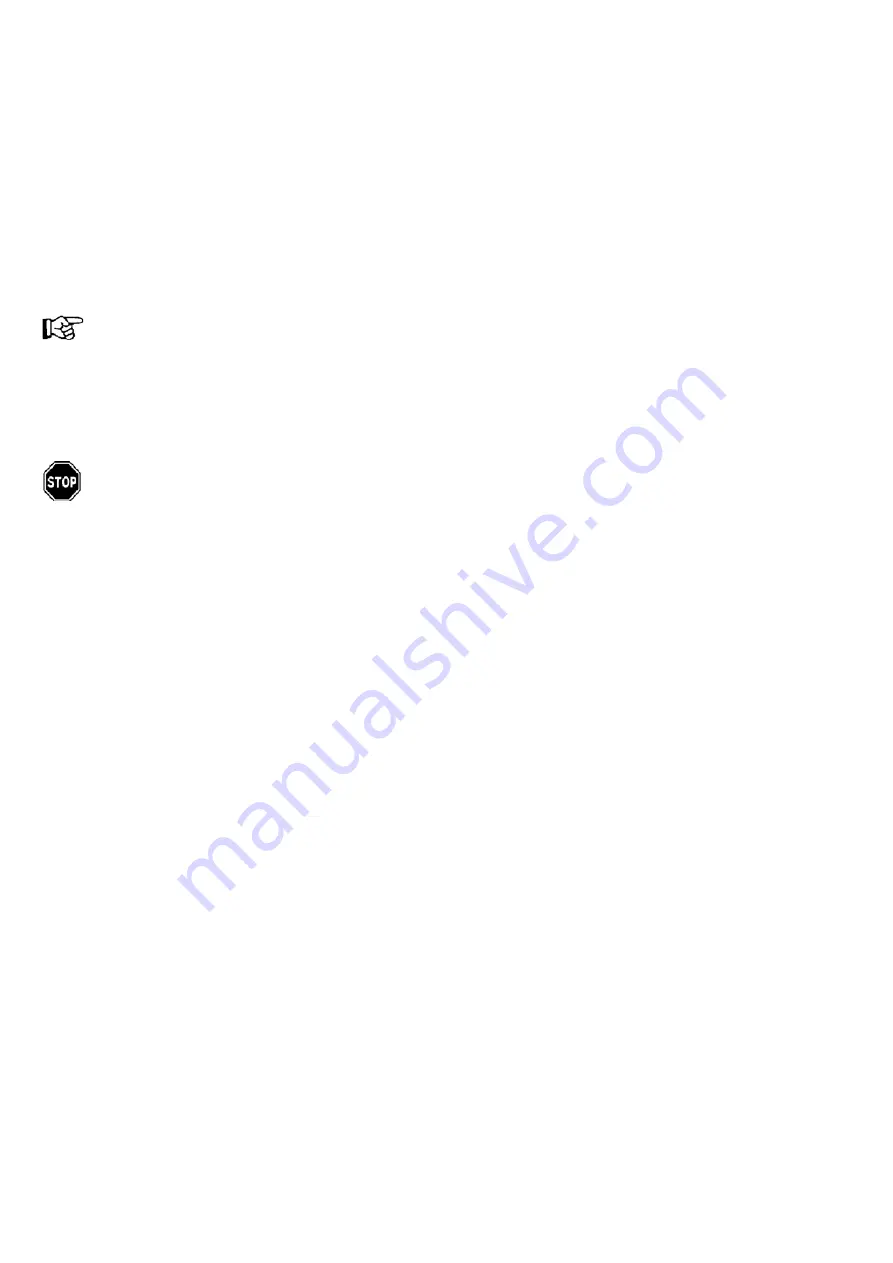
TRC66-86 *** 44
4 Malfunctions During Operation
4.1 General
If a malfunction occurs on the trench compactor, proceed as follows:
- Put the trench compactor out of operation as described in paragraph 2.9.
- Determine the source of the malfunction (refer to paragraph 4.2 - Trouble Shooting).
- Eliminate the malfunction (refer to paragraph 4.3 (Maintenance and Repair Work).
Important!
Please refer to the manual of the engine manufacturer with regard to the repair of engine malfunctions.
The detailed description of the maintenance and repair work in paragraph 4.3 allows a quick failure elimination
on condition that the given order is precisely kept to when service work is carried out.
Danger!
Any service work has to be made with appropriate tools and in accordance with the safety regulations
set out in this operating and maintenance manual.
If a problem persists although a component or assembly group has been replaced, repair work has to be continued
with the work described next.
If a failure cannot be rectified although the described service work has been carried out or if a defect is not described
in the operating and maintenance instructions, the failure must be repaired by authorized service personnel.
Summary of Contents for TRC 66
Page 2: ...TRC66 86 2...
Page 51: ...TRC66 86 51 5 Diagrams 5 1 Electric Diagram...
Page 53: ...TRC66 86 53 5 2 Hydraulic Diagram...
Page 57: ...TRC66 86 57...
Page 59: ...TRC66 86 59...