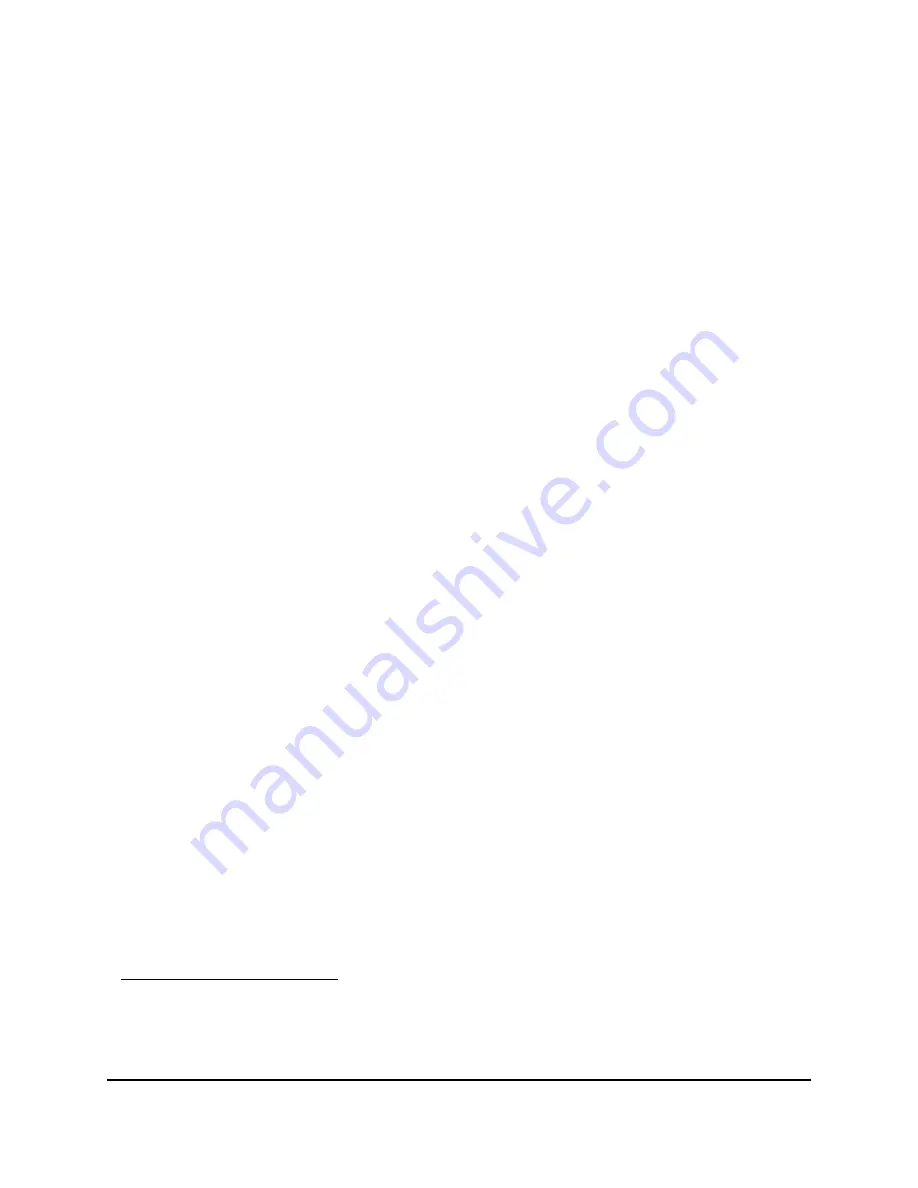
9
February 1997
Part No. 920160 Rev A
2.4.
THE BLENDING PROCESS
A blender has two grades of fuel (product) input to the dispenser. These two grades are the
LO and HI product inputs referred to as “feedstocks.”
The
proportional blending dispenser
uses the feedstock input grades to deliver three to
five grades (depending on model) outputs to the “nozzle.” Two of these grades are feed-
stock
*
and the other one to three (depending on model) are a blend mixture of some propor-
tion of the feedstock inputs. All grades are dispensed through the
same
hose and nozzle,
see Figure 2-3.
The
fixed ratio blending dispenser
uses the feedstock products to deliver three grade
outputs to the “nozzles.” Again, two of these three grades are the feedstock products
*
, but
unlike the proportional blender, the third grade or blended grade is delivered through a
separate
hose and nozzle. Also, the feedstock grades are each individually delivered
through separate hoses and nozzles, see Figure 2-4.
In all blending dispensers, there are two separate sets of hydraulics. One for controlling the
LO octane product input and one for controlling the HI octane product input. In all
enhanced Vista blending dispensers (1/V models), whether it’s a proportional or fixed ratio
blender, the LO and HI product hydraulic systems each contain a
proportional flow
control valve.
When any grade (LO, HI or blend) is selected, the blend ratio programmed into the
dispensers computer determines the percentage or proportion of HI product to be
dispensed. When the LO grade product is selected, the proportion or percentage of HI
product is 0%. When the HI grade product is selected, the percentage of HI product is
100%. When a blended grade is selected, a percentage of HI product (less than 100%) is
mixed with the remaining percentage of LO product, and the combined total (100%) deter-
mines the octane rating of the blended grade.
Knowing the percentage or proportion of HI, and thus LO, product to dispense and by
calculating the volume dispensed based on input signals from the pulsers, the computer
signals the solenoid drive board which in turn controls the proportional flow control valves.
Each proportional flow control valve continuously opens or closes, as directed by the sole-
noid drive board, to maintain the desired blend ratio and the maximum allowable flow
rate.
**
*
Some customer specific models may not dispense feedstocks. For example, one feedstock and four
blended grades may be dispensed.
** The maximum allowable flow rate in the United States is 10 gallons per minute.
Summary of Contents for Dresser Vista 1 Series
Page 1: ...1 Vista Series Blending and Non Blending Remote Dispensers SERVICE ...
Page 4: ...Part No 920160 Rev A February 1997 ...
Page 10: ...viii Part No 920160 Rev A February 1997 ...
Page 12: ...2 Part No 920160 Rev A February 1997 ...
Page 22: ...12 Part No 920160 Rev A February 1997 ...
Page 38: ...28 Part No 920160 Rev A February 1997 ...
Page 62: ...52 Part No 920160 Rev A February 1997 ...
Page 76: ...66 Part No 920160 Rev A February 1997 FIGURE 7 8 NOZZLE BOOT ASSEMBLY LIFT TO START ...
Page 77: ...67 February 1997 Part No 920160 Rev A FIGURE 7 9 NOZZLE BOOT ASSEMBLY PUSH TO START ...
Page 83: ...73 February 1997 Part No 920160 Rev A APPENDIX A TROUBLESHOOTING FLOWCHARTS ...
Page 110: ...100 Part No 920160 Rev A February 1997 ...
Page 111: ...101 February 1997 Part No 920160 Rev A APPENDIX B SERVICE INFORMATION AND CONNECTOR PIN OUTS ...
Page 134: ...124 Part No 920160 Rev A February 1997 ...
Page 136: ......
Page 137: ......
Page 138: ......
Page 139: ......
Page 140: ......
Page 141: ......
Page 142: ......
Page 143: ......
Page 144: ......
Page 145: ......
Page 146: ......