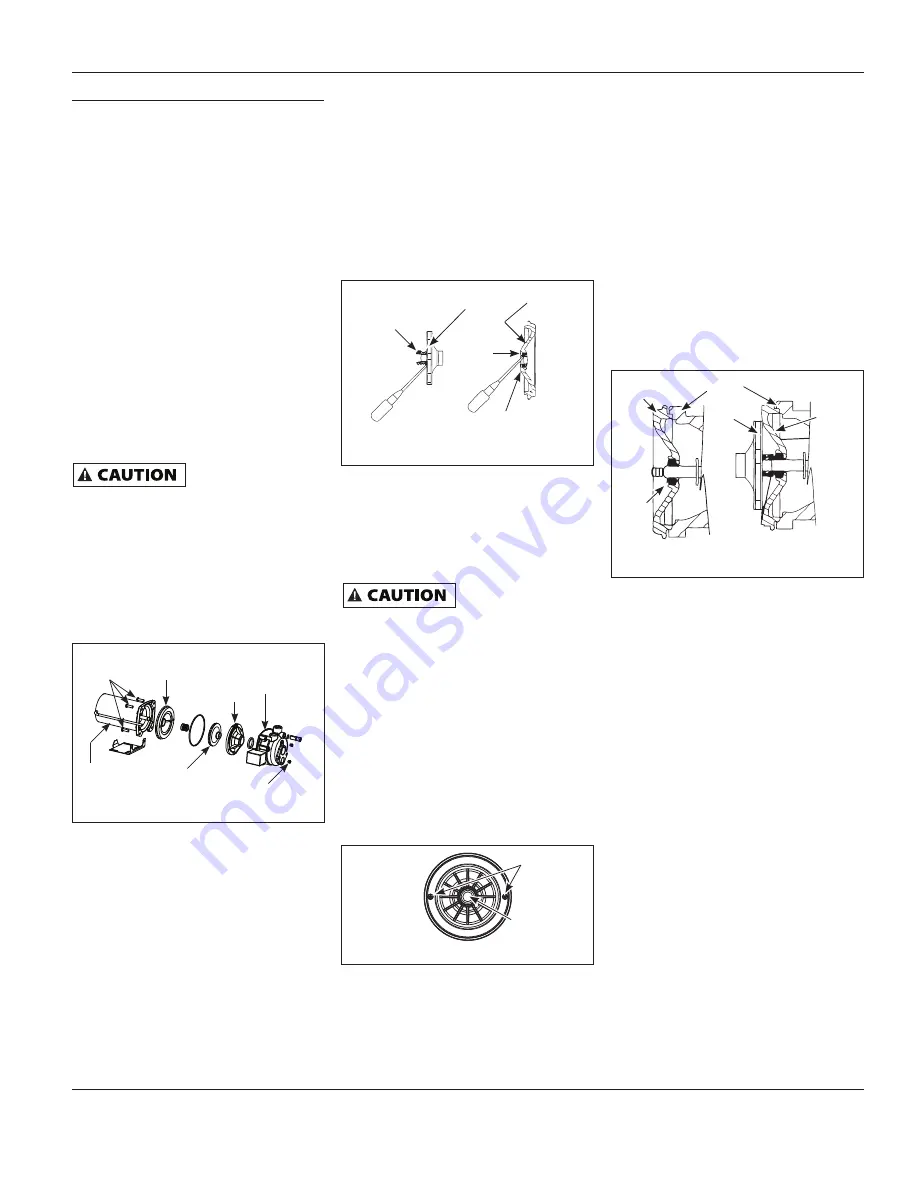
7
www.waynepumps.com
Maintenance
(Continued)
PRE-CHARGED TANK
Some air is lost through the bladder in
any tank. To prevent tank failure, check
the tank pre-charge on a yearly basis.
1. Disconnect power to the pump
2. Open a faucet nearest the tank and
allow all water to drain from the
tank.
3. Measure the tank pre-charge at the
valve stem using a tire gauge.
4. If necessary, adjust the pre-charge
with an air pump 28 - 30 psi on 1/2,
3/4 and 1 HP pumps.
LUBRICATION
The bearing used in the pumps are
lifetime lubricated at the factory and
require no additional lubrication.
REMOVING OLD SHAFT SEAL
Turn
disconnect
switch to “off”
position.
1. Disconnect power to the pump
2. Open a faucet nearest the tank and
allow all water to drain from the
tank.
3. Remove the four cap screws holding
the pump housing (volute) to the
motor (Figure 13).
4. Separate the pump housing (volute)
from the motor to expose the
diffuser and the seal plate.
5. Remove the two cap screws and
diffuser from the seal plate to
expose the impeller.
6. Remove the small end cap on the
end of the motor opposite the
impeller.
7. With a large screwdriver or
adjustable wrench, keep the shaft
from rotating and remove the
impeller with hand (standard right
hand thread). Be sure to hold
onto the cast iron seal plate when
removing the impeller from the
shaft.
8. Remove the seal plate.
9. Pry the rotating shaft seal member
from the impeller (Figure 14).
10. Push or pry the ceramic seat free
from the seal plate (Figure 14).
11.Remove loose particles from impeller
hub and seal plate.
INSTALLING NEW SHAFT SEAL
Before
handling
shaft seal parts wipe
hands clean. Dirt or grease can damage
the seal.
1. Wet the inside of the seal cavity
on seal plate and the rubber cup
enclosing the new ceramic seat
with cooking oil. Be careful not to
scratch the ceramic surface of the
seal seat and push seat enclosed in
rubber into seal cavity on seal plate.
Use a cardboard washer to protect
polished surface when pushing
against ceramic seat with any object.
Be sure to remove cardboard washer.
2. Carefully slip seal plate over shaft
so as not to disturb seal position in
seal plate. The seal plate must be
orientated during assembly so that
the two holes are on a horizontal
line across the motor shaft and the
(4) locating pins on the back of the
seal plate line up with the tabs on
the motor housing (Figure 15). This
placement should be done to ensure
proper draining and priming.
3. Place rotating shaft seal member in
position on impeller and press into
place. Take care not to press against
polished seal surface.
4. Position impeller on shaft and
tighten securely (Figure 16).
5. Secure diffuser to seal plate
using the two cap screws. Be sure
the screws are orientated on a
horizontal line as described in Step
2.
6. Carefully position pump housing
(volute) gasket over the diffuser
onto the seal plate. In all convertible
applications the seal ring must also
be positioned on the diffuser. In all
shallow well applications care must
be taken that the o-ring is clean and
properly positioned on the venturi.
Cleaning and positioning makes a
good seal inside the diffuser when
assembled.
7. Assemble the pump housing
(volute) to the motor using the
four cap screws. Be sure the pump
housing (volute) gasket is positioned
correctly and tighten the screws
securely.
NOTE
: Shaft must rotate freely and
motor end cap should be secured before
operation.
Operating Instructions & Parts Manual
CWS50, CWS75 and CWS100
Figure 13 - Convertible Well Pump
Figure 14 - Removing Shaft Seal and
Ceramic Seat
Figure 16 - Motor Shaft
Figure 15 - Seal Plate Replacement
Cap
Screws
Motor
Seal
Plate
Impeller
Diffuser
Pump
Housing
(Volute)
Drain Plug
Rotating
Shaft Seal
Member
Rubber
Seat
Ring
Impeller
Seal
Plate
Ceramic Seat
Screw
Holes
Motor
Shaft
Seal
Facing
Must
Be Clean For
Proper Seal
Motor
Seal
Plate
Impeller
Seal
Seat
Seal Plate