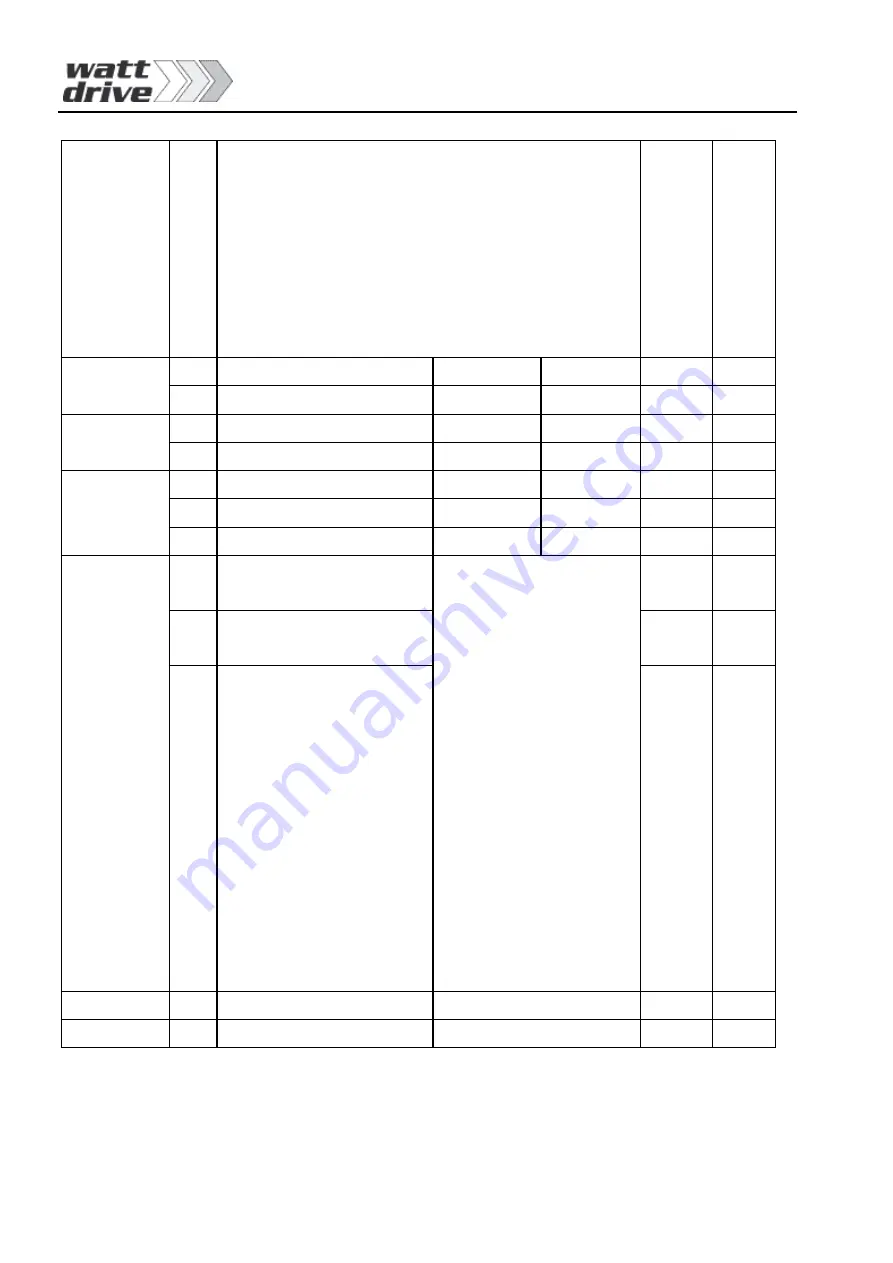
12
Dynamic
braking &
Priority of
Stopping &
Speed search &
AVR control
48
xxx0 : Enhanced braking capacity
xxx1 : Standard braking capacity
xx0x : STOP key effective in remote control mode
xx1x : STOP key ineffective in remote control mode
x0xx : Speed search controlled by terminals on TM2
x1xx : Speed search effective when inverter start
0xxx : AVR function effective
1xxx : AVR function ineffective
0000
Accel./Decel.
49
Accel. time 2
0.1 sec
0.1-3600 sec
10.0 sec
*1
time 2
50
Decel. time 2
0.1 sec
0.1-3600 sec
10.0 sec
*1
Display mode
51
Display mode selection
1
0-5
0
*1
52
Line speed display
1
0-9999
1800
*1
DC Braking
53
DC Braking time
0.1 sec
0-25.5 sec
0.5 sec
54
DC Braking injection freq.
0.1 Hz
0.1-10 Hz
1.5 Hz
55
DC Braking level
0.1 %
0-20 %
8 %
Multi function
input
56
Multi-input 1 (terminal 6)
00 : SP1 02 : SP2
02 : SP3 03 : Jog
00
57
Multi-input 2 (terminal 7)
04 : Accel / Decel time selection
05 : External emergency stop
01
58
Multi-input 3 (terminal 8)
06 : External coast stop
07 : Speed search
08 : Energy saving
09 : control signal selection
10 : Communication selection
11 : Accel. / Decel. Prohibit
12 : Up command
13 : Down command
14 : Sequence Control
15 : Master / Auxiliary speed
16-31 : Change 00-15 from
Normal open to normal close
02
59
Reserved
60
Reserved