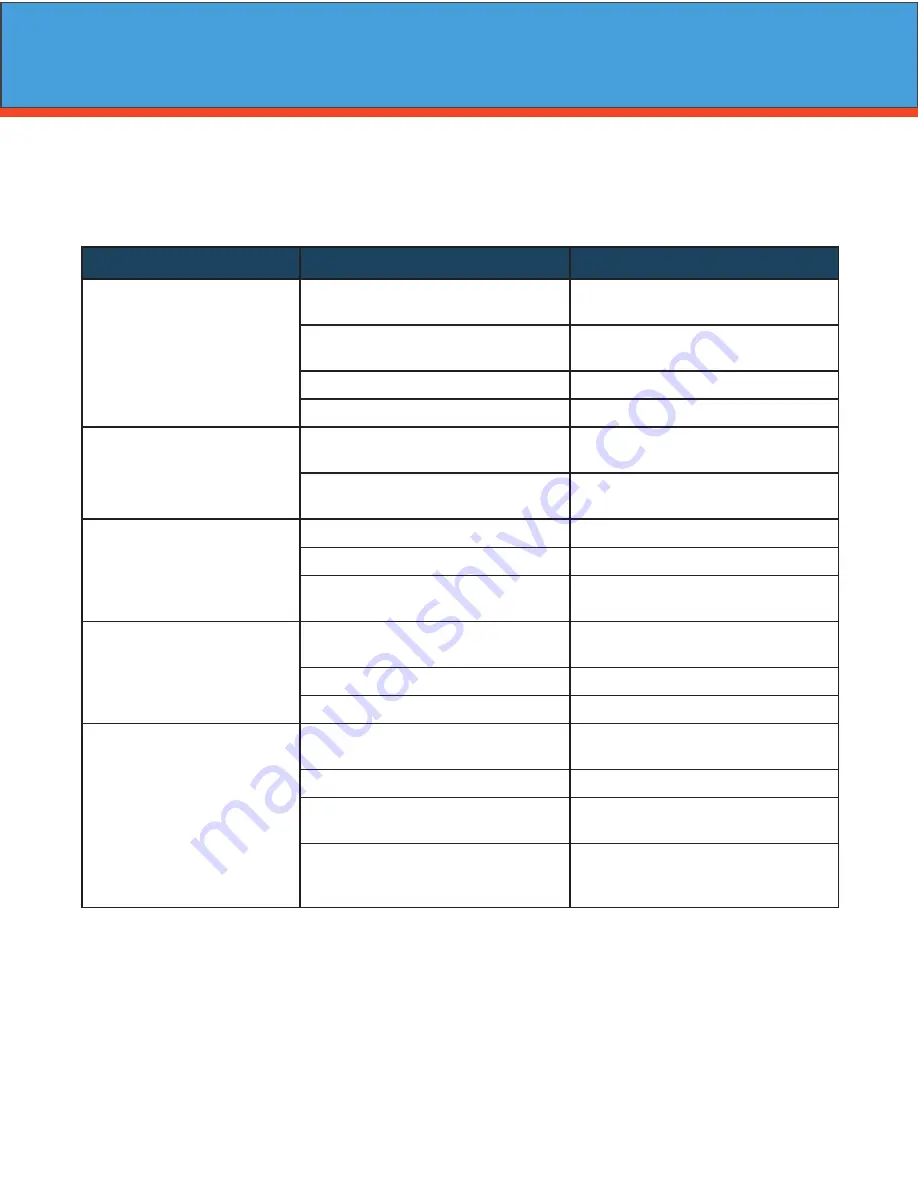
19
Troubleshooting Guide and Error Codes
SYMPTOM
PROBABLE CAUSE
CORRECTION
1. Filter Fails to
Regenerate
Automatically
Power supply plugged into
intermittent or dead power source
Connect to constant power source
Improper control valve
programming
Reset program settings
Defective power supply
Replace power supply
Defective Drive motor
Replace motor
2. Regeneration at
Wrong Time
Time of day improperly set, due to
power failure
Reset time of day programming and
install 9-volt battery.
Regeneration time set improperly
Reset regeneration time program-
ming
4. Poor Water
Quality
Check items listed in #1 and #2
Bypass valve open
Close bypass valve.
Channeling
Check for too slow or high service
flow. Check for media fouling.
6. Loss of Water
Pressure
Scaling / fouling of inlet pipe
Clean or replace pipeline. Pretreat
to prevent.
Fouled media
Clean media. Pretreat to prevent.
Improper backwash setting
Backwa
s
h more frequently
7. Continuous Flow
to Drain
Foreign material in control
Call dealer. Clean valve and replace
piston and seals
Internal control leak
Same as above.
Valve jammed in backwash, brine or
rapid rinse position
Same as above.
Motor stopped or jammed
Check for jammed piston. Replace
piston and seals. Replace motor if
motor is unresponsive.
F.
To Replace Meter
1. Follow steps
A1 - A3
2. Unplug meter cable from front of circuit board.
3. Unscrew meter assembly nut from valve body.
4. Remove meter from valve body and clean or replace as necessary.
5. Reinstall meter, nut and cable.
Control Valve Error Code Diagnosis
Under normal operating conditions, when your control valve is in the “in service” position, the display
should alternate between the current time of day and the number of days remaining (for filters and time
clock softeners) or gallons remaining (for metered softeners) until the next regeneration. This is the “home
display.” If the valve is currently going through a regeneration cycle, the display will show the cycle step
on the left side of the display and the number of minutes remaining in that step on the right side of the
display. If any other information is being displayed, then the valve is informing you of an issue. There are
five error codes which could indicate an issue with the control valve. When an error is being displayed, the
valve will be in a stopped position, and the buttons will not respond to being pressed. Even if the cause of
the error code is corrected, the error code will not clear until the power supply has been disconnected and
reconnected (this will be referred to as “cycling” the power). All error codes are displayed as the letters “Err”
followed by a flashing number 2-6: