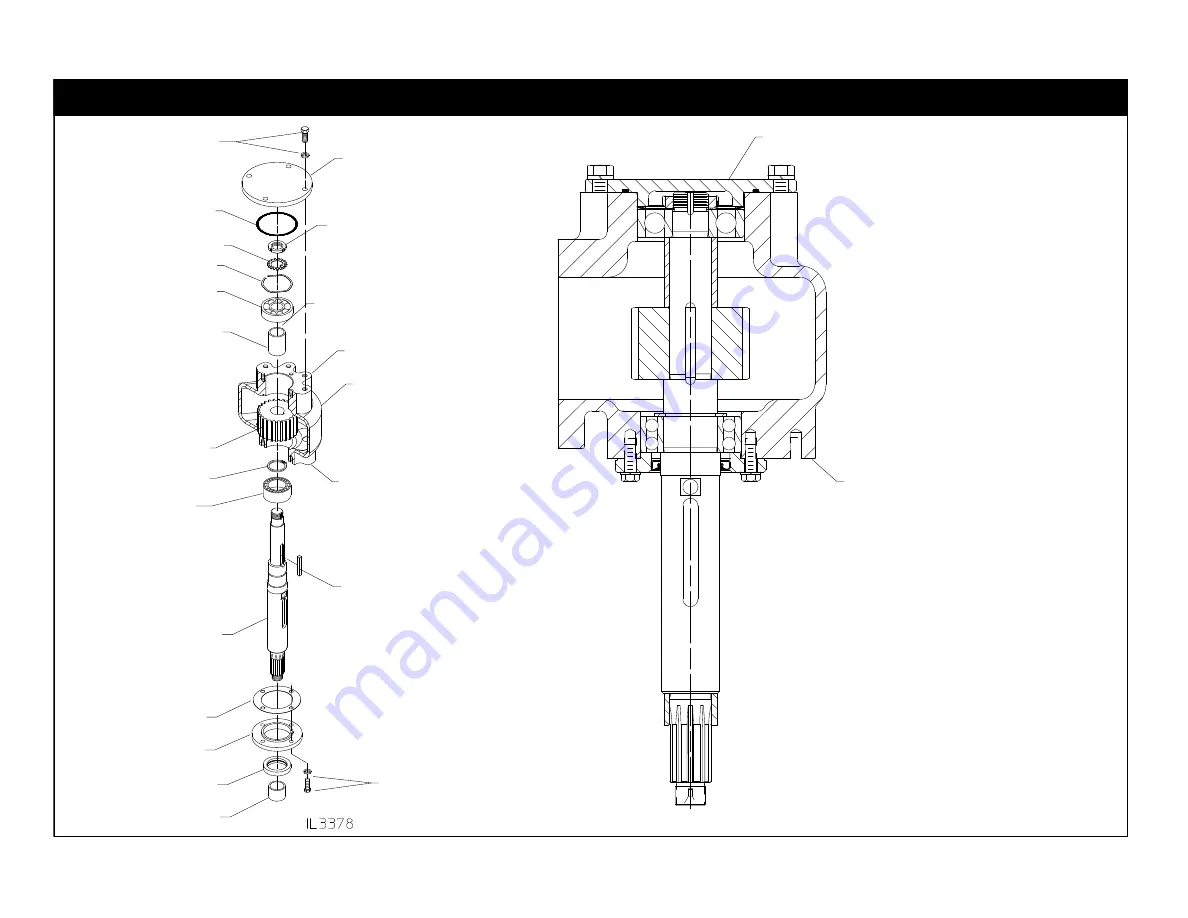
T-365
Page 33 of 75
Disassembly - Disassemble Cap (Continued)
Bearing Cover
Single Row Bearing
Front Cap Flange
Spacer
Double Row
Bearing
Driven Shaft
Shim, .010 in.
Oil Seal Housing
Oil Seal
Yoke Spacer
Four (4) 3/8-16 x 1 in.
Screws and Lockwashers
Rear Cap Flange
Four (4) 3/8-16 x 1 in.
Screws and Lockwashers
Rear
Driven Sprocket
Key
Bearing Locknut
Wave Spring
Bearing Lock nut
Front
Eclipse ES™ CAFS on Rear of PTO
1.
Remove the screws from the bearing cover and
oil seal housing. Remove cover and housing. Dis
card the oil seal.
2.
Straighten tab of the bearing lockwasher from slot
in bearing lock nut and then remove the locknut,
lockwasher and wave spring.
3.
Under a press, support the assembly on the rear
face side of the cap and apply a press load to the
end of the driven shaft to press the shaft out of the
ball bearing, spacer and sprocket. Rear bearing
and retaining ring will come out with the driven
shaft. Remove from shaft.
4.
Remove the ball bearing, spacer and sprocket
from cap.
Cap
Bearing Lockwasher
O-ring
Retaining Ring