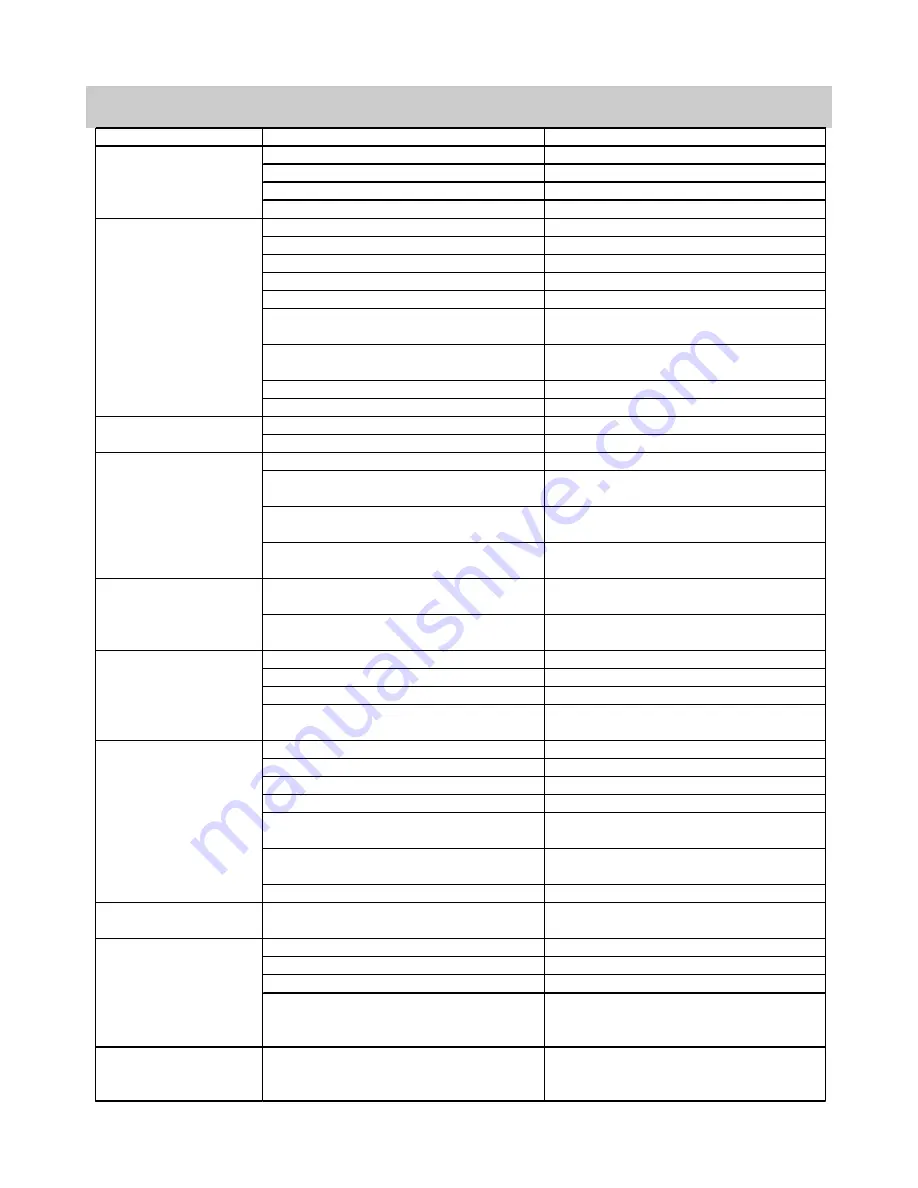
Trouble Shooting
Issue
Possible
Cause
Possible
Solution
1.
No
power
supply.
Check
electrical
service,
fuse,
etc.
2.
Defective
circuit
board.
Replace
faulty
parts.
3.
Power
failure.
Reset
time
of
day.
4.
Defective
meter.
Replace
turbine
meter.
1.
By
‐
pass
valve
open.
Close
by
‐
pass
valve.
2.
Out
of
salt
or
salt
level
below
water
level.
Add
salt
to
tank.
3.
Plugged
injector
/
screen.
Clean
parts.
4.
Flow
of
water
blocked
to
brine
tank.
Check
brine
tank
refill
rate.
5.
Hard
water
in
hot
water
tank.
Repeat
flushing
of
hot
water
tank
required.
6.
Leak
between
valve
and
central
tube.
Check
if
central
tube
is
cracked
or
o
‐
ring
is
damaged.
Replace
faulty
parts.
7.
Internal
valve
leak.
Replace
valve
seals,
spacer,
and
piston
assembly.
8.
Reserve
capacity
setting
too
low.
Increase
reserve
capacity.
9.
Not
enough
capacity.
Increase
salt
dosage.
1.
Refill
time
is
too
high.
Check
refill
time
setting.
2.
Defective
flow
control.
Replace.
1.
Iron
or
scale
build
up
in
line
feeding
unit.
Clean
pipes.
2.
Iron
build
up
inside
valve
or
tank.
Clean
control
and
add
resin
cleaner
to
clean
bed.
Increase
regeneration
frequency.
3.
Inlet
of
control
plugged
due
to
foreign
material.
Remove
piston
and
clean
control
valve.
4.
Deteriorated
resin.
(Maybe
caused
from
high
chlorine
or
chloramines.)
Re
‐
bed
unit.
Consider
adding
carbon
pre
‐
treatment.
1.
Air
in
water
system.
Check
well
system
for
proper
air
eliminator
control.
2.
Incorrect
drain
line
flow
control
(DLFC)
button.
Check
for
proper
flow
rate.
1.
Plugged
injector
or
screen.
Clean
parts.
2.
Valve
not
regenerating.
Replace
circuit
board,
motor,
or
control.
3.
Foreign
material
in
brine
valve.
Clean
parts.
4.
Unit
not
drawing
brine.
Check
for
vacuum
leak
in
brine
line
connections.
1.
Drain
line
flow
control
is
plugged.
Clean
parts.
2.
Injector
or
screen
is
plugged.
Clean
parts.
3.
Inlet
pressure
too
low.
Increase
pressure
to
25
PSI.
4.
Internal
valve
leak.
Replace
seals,
spacers,
and
piston
assembly.
5.
Safety
valve
closed.
Check
for
leak
in
brine
line
connections.
Replace
safety
float
assembly.
6.
Vacuum
leak
in
brine
line.
Check
for
leak
in
brine
line
connections.
Tighten
all
connections.
7.
Drain
line
has
kink
in
it
or
is
blocked.
Check
drain
line.
H.
Valve
continuously
cycles.
1.
Defective
position
sensor
PCB.
Replace
faulty
parts.
1.
Valve
settings
incorrect.
Check
valve
settings.
2.
Foreign
material
in
control
valve.
Clean
control.
3.
Internal
leak.
Replace
seals,
spacers,
and
piston
assembly.
4.
Piston
is
stuck
in
position.
Motor
may
have
failed
or
gears
have
jammed
or
disengaged.
Check
for
power
to
motor.
Check
for
loose
wire.
Check
for
jammed
gears
or
gears
disengaged.
Replace
faulty
parts.
J.
Valve
makes
beeping
sound.
1.
The
piston
has
not
advanced
to
the
next
cycle
position
properly.
Check
for
power
to
motor.
Check
for
loose
wire.
Check
for
jammed
gears
or
gears
disengaged.
I.
Flow
to
drain
continuously.
G.
Unit
fails
to
draw
brine.
A.
Unit
fails
to
initiate
a
regeneration
cycle.
B.
Water
is
hard.
E.
Resin
in
drain
line.
C.
Salt
use
is
high.
D.
Low
water
pressure.
F.
Too
much
water
in
brine
tank.
22
Summary of Contents for HTO-185HEUF
Page 7: ...Installation 7...
Page 20: ...Power Head Exploded View 20...