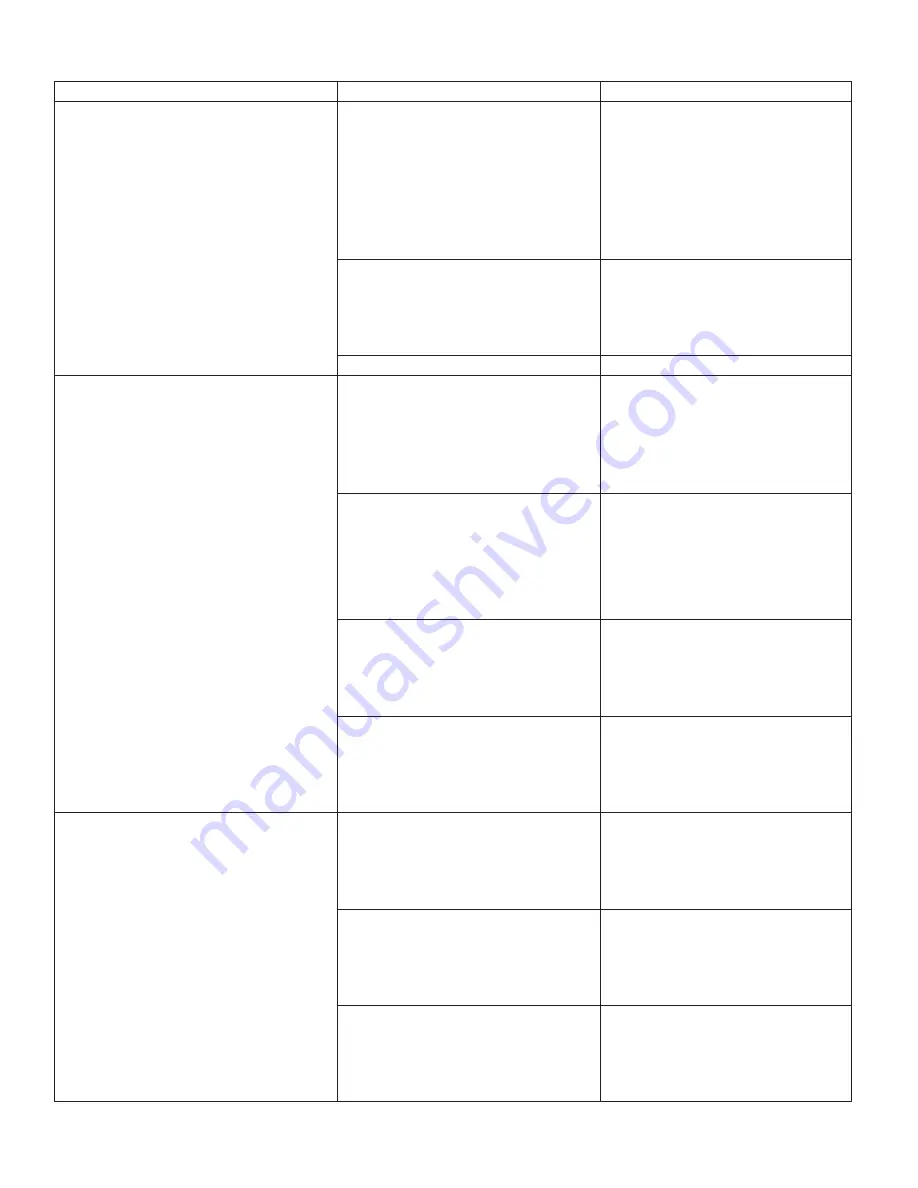
Page 32
WS1TT Drawings and Service Manual
Problem
Possible Cause
Solution
14. E1, Err – 1001, Err – 101 = Control unable to
sense motor movement
a. Motor not inserted full to engage pinion,
motor wires broken or disconnected
a. Disconnect power, make sure motor is
fully engaged, check for broken wires,
make sure two pin connector on motor
is connected to the two pin connection
on the PC Board labeled MOTOR. Press
NEXT and REGEN buttons for 3 seconds
to resynchronize software with piston
position or disconnect power supply
from PC Board for 5 seconds and then
reconnect.
b. PC Board not properly snapped into drive
bracket
b. Properly snap PC Board into drive bracket
and then Press NEXT and REGEN buttons
for 3 seconds to resynchronize software
with piston position or disconnect power
supply from PC Board for 5 seconds and
then reconnect.
c. Missing reduction gears
c. Replace missing gears
15. E2, Err – 1002, Err – 102 = Control valve motor
ran too short and was unable to
fi
nd the next cycle
position and stalled
a. Foreign material is lodged in control valve
a. Open up control valve and pull out piston
assembly and seal/ stack assembly for
inspection. Press NEXT and REGEN
buttons for 3 seconds to resynchronize
software with piston position or disconnect
power supply from PC Board for 5 seconds
and then reconnect.
b. Mechanical binding
b. Check piston and seal/ stack assembly,
check reduction gears, check drive
bracket and main drive gear interface.
Press NEXT and REGEN buttons for 3
seconds to resynchronize software with
piston position or disconnect power supply
from PC Board for 5 seconds and then
reconnect.
c. Main drive gear too tight
c. Loosen main drive gear. Press NEXT
and REGEN buttons for 3 seconds to
resynchronize software with piston
position or disconnect power supply
from PC Board for 5 seconds and then
reconnect.
d. Improper voltage being delivered to PC Board d. Verify that proper voltage is being supplied.
Press NEXT and REGEN buttons for 3
seconds to resynchronize software with
piston position or disconnect power supply
from PC Board for 5 seconds and then
reconnect.
16. E3, Err – 1003, Err – 103 = Control valve motor
ran too long and was unable to
fi
nd the next cycle
position
a. Motor failure during a regeneration
a. Check motor connections then Press
NEXT and REGEN buttons for 3 seconds
to resynchronize software with piston
position or disconnect power supply
from PC Board for 5 seconds and then
reconnect.
b. Foreign matter built up on piston and stack
assemblies creating friction and drag enough
to time out motor
b. Replace piston and stack assemblies. Press
NEXT and REGEN buttons for 3 seconds
to resynchronize software with piston
position or disconnect power supply
from PC Board for 5 seconds and then
reconnect.
c. Drive bracket not snapped in properly and out
enough that reduction gears and drive gear
do not interface
c. Snap drive bracket in properly then Press
NEXT and REGEN buttons for 3 seconds
to resynchronize software with piston
position or disconnect power supply
from PC Board for 5 seconds and then
reconnect.