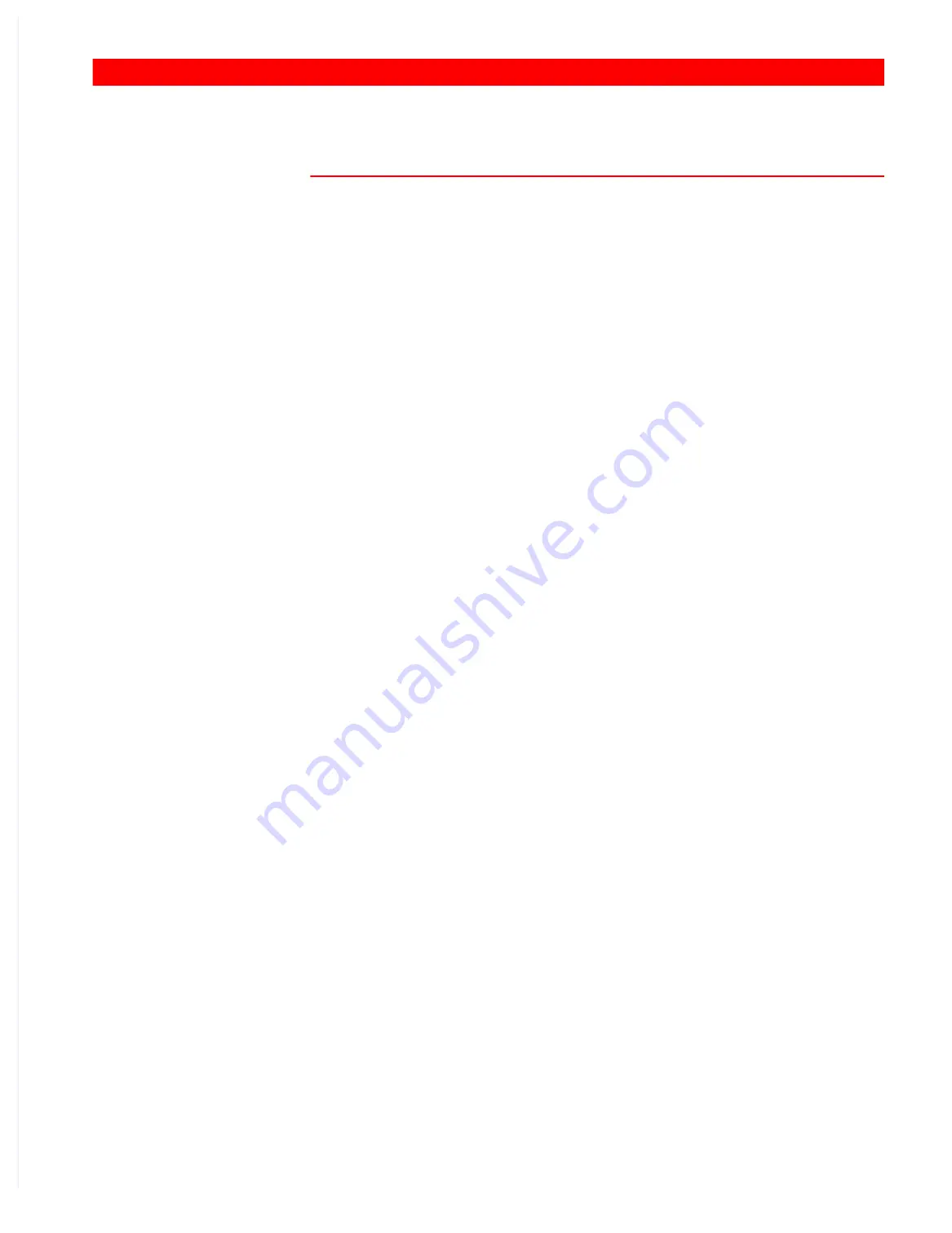
00B.2.5 WECS 7000/8000 checklist
The follow ing preca ut ions mu st be pa id a tt ention to before welding in
th e vicinity of a WE CS 7000 or 8000 cont rol syst em:
•
Deactive the system by disconnecting all external connectors
(X1...X6).
•
If t he w elding point is close to (a pproxima tely w ith in a ra dius of
2 m) an elect ronic module (SS M-701, SS M-558, CC D /P D M, C ense
etc.) disconn ect a ll connectors of th e unit
•
Close th e covers of th e ca binet
•
Disconnect th e interconnections betw een t he ha rnesses an d t he
cabinet.
•
If convenient , protect ha rnesses, ca bles, sensors a nd oth er equip-
ment from sparkles with a proper meta l sheet.
200147
Welding Precautions
Appendix B