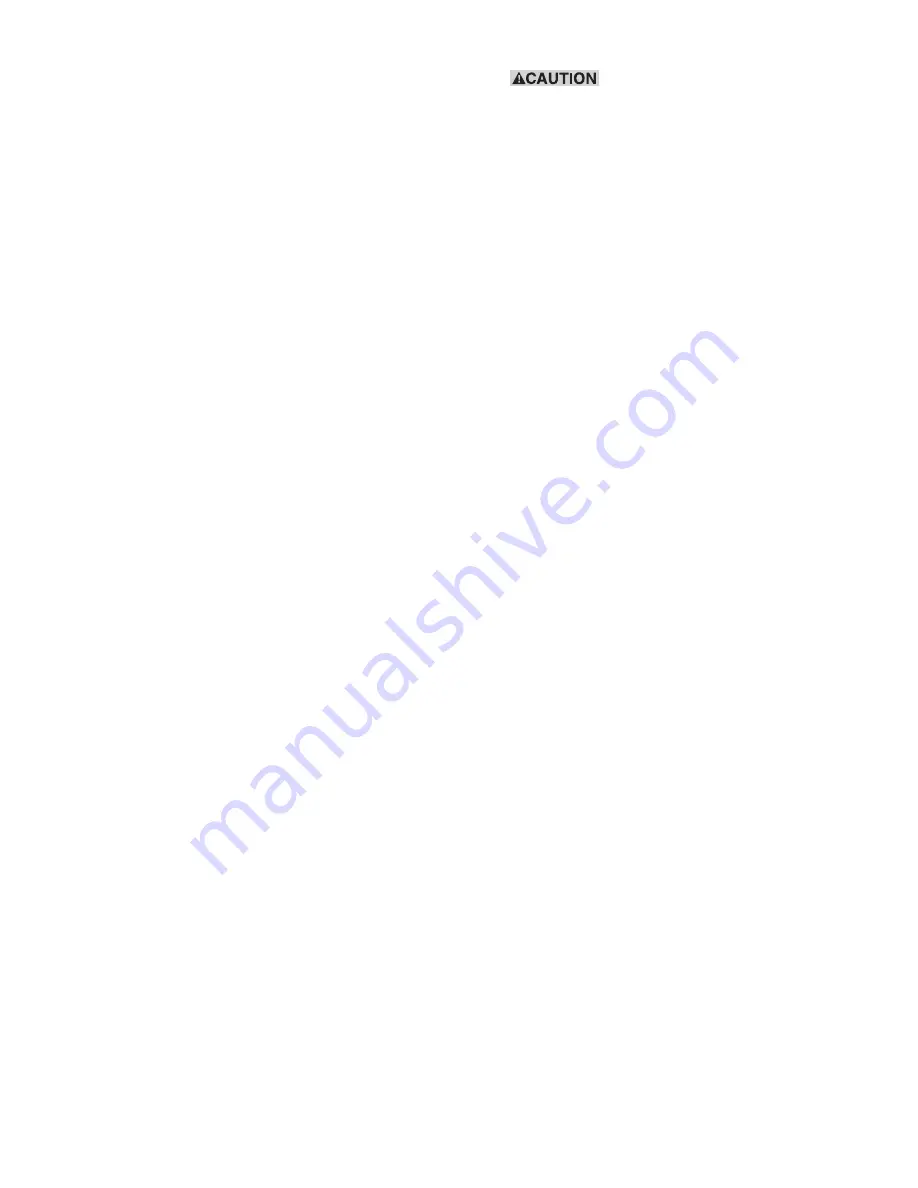
4
Warner Electric • 800-825-9050
P-2003-2 • 819-0420
Auxiliary Inputs
• Brake Stop – Applies full voltage to the
connected brakes . Active high input .
• Brake Run – Voltage to the brake is controlled by
any of the sensor inputs and/or the front panel
tension adjust . Active high input .
• Brake Off – Removes output current to the brake .
Puts the brake at zero current level . Active high
input .
Note 1:
The remote input signal for these functions
requires a minimum contact rating of 20 VDC at .01
amps and a maximum of state leakage current less
than 100 micro-amps .
Note 2:
The remote switch input overrides the front
panel switch .
Front Panel
• Tension Adjust – Provides current adjust to the
brake from 0 to 100% . In the remote and
analog input mode, provides for maximum output
level set to the brake .
• Brake Mode Switch –
Modes: “stop”-brake full on
“run” -normal operation
“off” -brake off
Indicators
(Front Panel)
• Green LED indicates AC power has been applied
to the control .
• Red LED indicates there is a short on the output .
Turn the front panel switch “off” to reset the short
circuit .
General
The control chassis must be considered NEMA 1
and should be kept clear of areas where foreign
material, dust, grease, or oil might affect control
operation .
Potentiometers
(supplied by the customer)
• Remote Torque Adjust
1,000 ohms, 10% tolerance, .5% linearity,
.5 watts, linear taper
• Roll Follower – 1,000 ohms, 10% tolerance, .5%
linearity, .5 watts, linear taper
o
1 .
If you are using a PLC or an
external power supply with this control, you must
enable the isolation of the control .
o
2 . The TCS-200-1 cannot operate a single brake
or brakes that require more than 4 .25 amps
continuous .
o
3 . The TCS-200-1H cannot operate a single
brake or brakes that require more than 5 .8 amps
continuous .
This Installation and Operation Manual has been
arranged for the systematic installation and start-up
of your tension control system . To achieve the best
possible results, we recommend checking off each
completed step in the space provided before
proceeding to the next step .
Sample
o
Attach the TCS-200 control chassis to the
mounting surface and secure with mounting
hardware .
Check box after completing each step .
Control Mounting
o
1 . Determine a suitable location for the control to
be mounted . Consideration should be given to
whether the front panel adjustments will require
access by the operator .
o
2 . Using the dimensional data supplied in Figure
1a and Figure 1b, drill four mounting holes using
a #16 drill if #8 through-bolts are used . For #8
capscrew mounting, use a #29 drill and tap holes
for #8 screws . Templates for hole drilling are
found on page 21 .
o
3 . Attach the TCS-200-1 or TCS-200-1H control
chassis to the mounting surface and secure with
mounting hardware .
Note:
The control chassis has been designed to
accommodate two half-inch conduits for wiring when
the control is mounted to the machine frame .