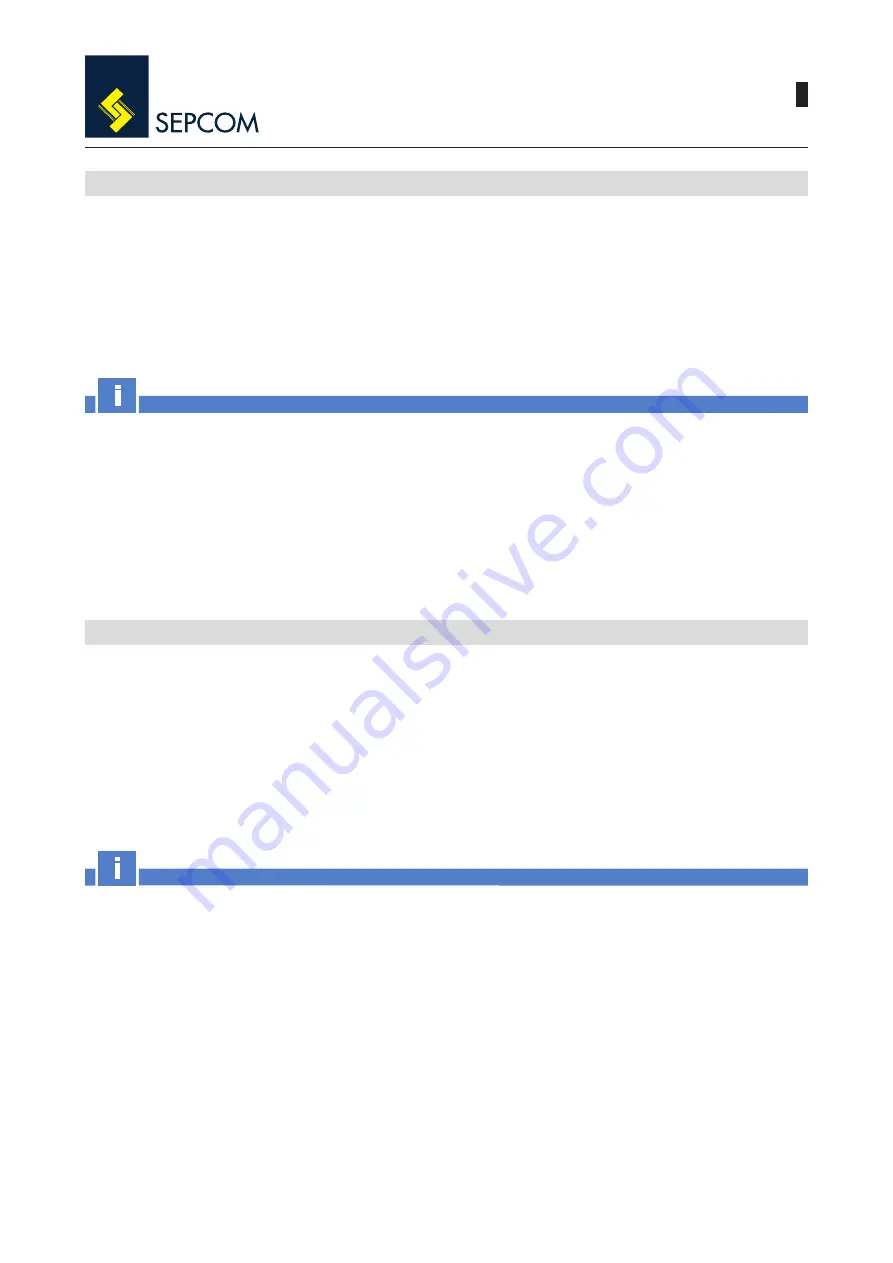
3
2
SEP.QE_SEPCOM_SIP-BED-EASY--.M.A3.0722.EN Issue: A3
07.22
1.0 INTRODUCTION
QE SEPCOM SIP BED EASY
The SEPCOM
®
SIP BED Easy control panel manages the operating logics of the system consisting of a screw
press separator and a pneumatic presser, in coordination with other users part of a conventional separation
system, such as feeding pump, agitator and level sensors.
The SEPCOM
®
SIP BED Easy control panel allows keeping constant drying degree of the separated solids to
be by modulating the thrust of the pneumatic presser on the solids outlet, depending on the current absorption
set for the separator motor: the higher the absorption setpoint, the higher the drying degree of the separated
solids.
Important
The SEPCOM
®
SIP BED Easy of the control panel version controls directly only the pneumatic presser
and the absorption of the separator. The 24 Vdc power supply of the control panel, as well as the
power supply of all electric motors, must be provided from a main electrical panel previously installed
or already fitted on the plant. The levels as well as the other users connected to a separation system
(pump and agitator) can only be managed from the main control panel interfaced with the SEPCOM
®
SIP BED Easy.
1.4 Operating principle
Avoid shocks and tilting the equipment.
Observe safety distances from the lifting mean.
Prevent the presence of persons under suspended loads or within the operation area of the lifting equipment
used.
Keep the load as low as possible to ensure stability and greater visibility for the operator.
On using the lifting means (hooks, ropes, bands etc.) ensure they are in good condition and suit the safety
regulations in force.
Important
The terms “equipment”, “control panel” used in this manual refer to the same machine.
The separator, control panel and air compressor (that feeds the pneumatic presser) are to be consid-
ered as a machine and must, therefore, bear the CE marking.
It is forbidden to start the control panel unless the machine/plant in which it is to be installed has been
declared compliant with the Directive 2006/42/EC and further modifications.
1.5 Lifting and shipment