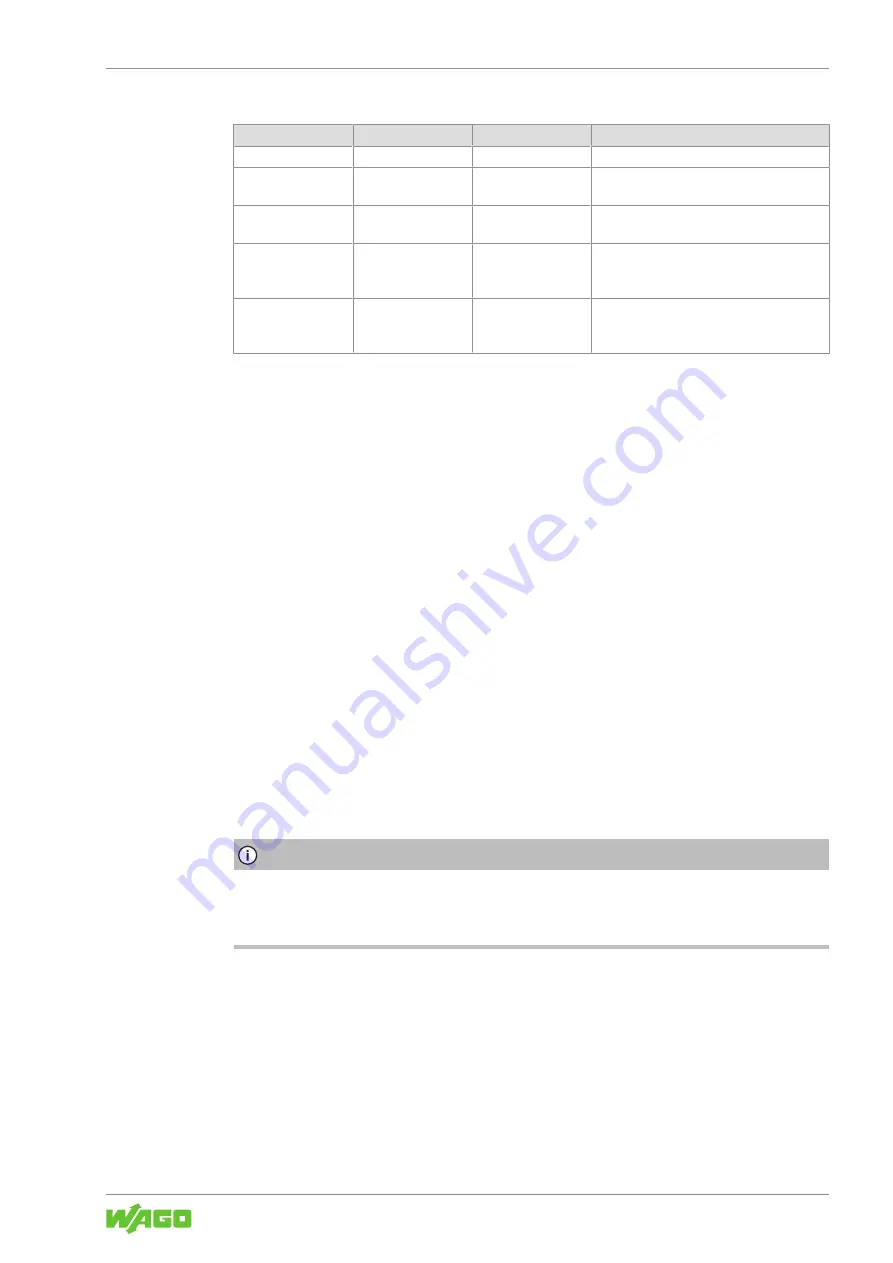
765-4501/0100-0000
Commissioning
Product manual | Version: 1.1.0
95
8PORT IOL-A FLD EI DC 24V 2.0A
Table 63: Setting the
Inspection Levels
and
Backup Levels
for Device Check during Validation and Backup
Selection Option
Inspection Level
Backup Level
Description
No device check
NO_CHECK
Disable
No device check is performed.
Type compatible de-
vice (V1.0)
TYPE_COMP
Disable
Device check for type-compatible device
per IO-Link specification 1.0
Type compatible de-
vice (V1.1)
TYPE_COMP
Disable
Device check for type-compatible device
per IO-Link specification 1.1
Type compatible de-
vice (V1.1) with
restore
TYPE_COMP
Restore
Device check for type-compatible device
per IO-Link specification 1.1 with backup &
restore functionality
Type compatible de-
vice (V1.1) with re-
store
TYPE_COMP
Restore
Device check for type-compatible device
per IO-Link specification 1.1 with restore
functionality
VendorID Input Field
This element contains the expected manufacturer ID (VendorID, 2 bytes) of the con-
nected device. The permissible values range from 1 to 0xFFFF. This information is re-
quired for the device check for type compatibility. It can be omitted if
[No device check]
is selected.
DeviceID Input Field
This element contains the expected device ID (DeviceID, 3 bytes) of the connected de-
vice. The permissible values range from 1 to 0xFFFFFF. This information is required for
the device check for type compatibility. It can be omitted if
[No device check]
is selected.
PortCycleTime Drop-Down Menu
Depending on the selected operating mode, the expected cycle time of the port either can
be selected from the
PortCycleTime
drop-down menu or is merely displayed. The en-
coding corresponds to the one in the port status.
10.3.1.4.2 Accessing a Connected IO-Link Device
The
IOL
tab allows read and write access to the IO-Link device connected to an IO-Link
port via index and subindex. The ISDU message format (ISDU = Indexed Service Data
Unit) is used for this purpose.
Note
You can find the meaning of the index and subindex values in the documentation
of the connected IO-Link device.
You can find a description of the ISDU message format in the IO-Link specification.
Required Rights
Changes to settings require operator or admin rights. If you do not have these, the tab is
grayed out, and the displayed values cannot be edited.
Access to IO-Link Device
To access the data of an IO-Link device connected to the selected IO-Link port via index
and subindex (ISDU message format), proceed as follows: