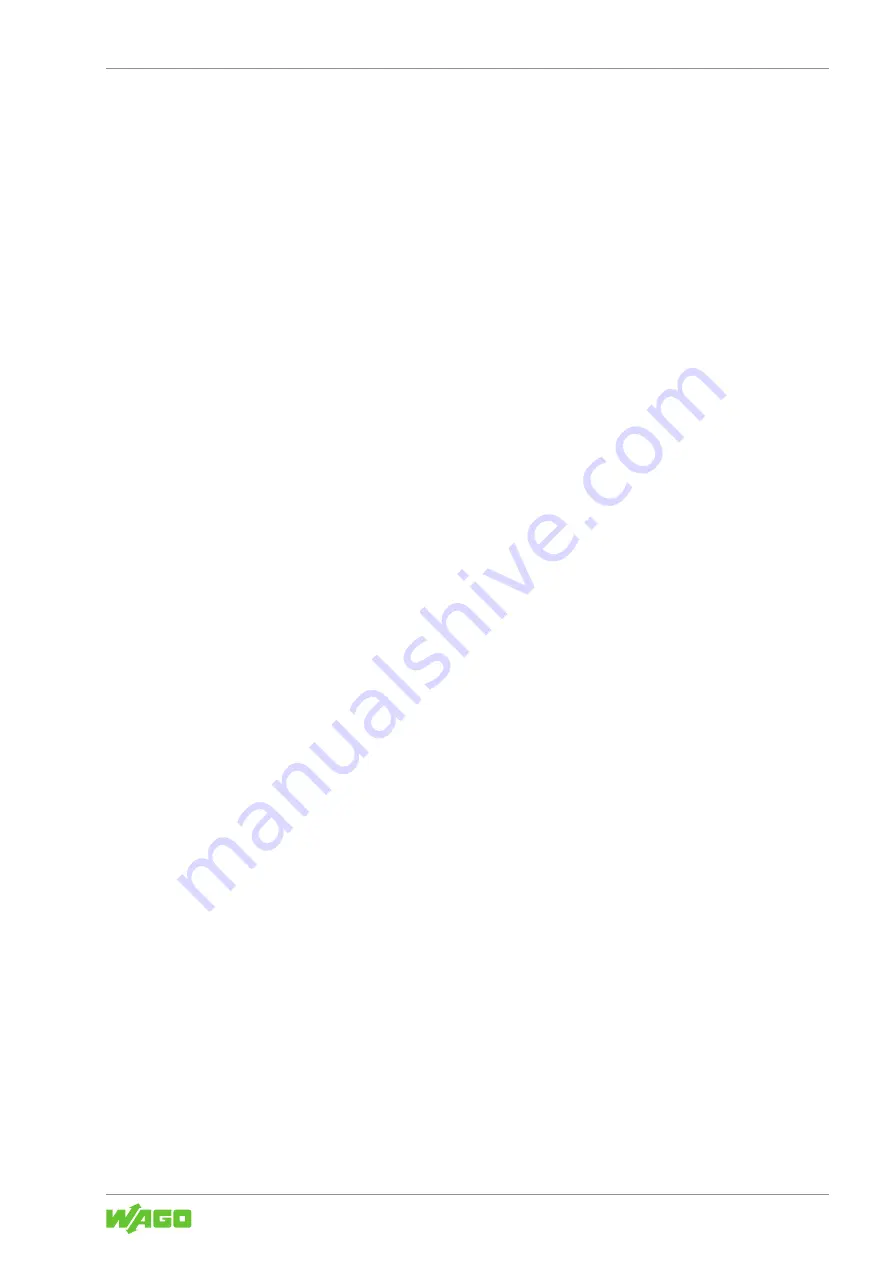
765-4102/0100-0000
Commissioning
Product manual | Version: 2.1.0
119
8PORT IOL-B FLD PN DC 24V 2.0A
Displays the XML source text
With navigation to the main elements of the IODD
With text search within the IODD
10.2.3.4 Parameterizing the Product with WAGO IO-Link Configurator
WAGO IO-Link masters can be used in various system environments. They can be either
gateways that link IO-Link to higher-level fieldbus or ETHERNET systems, modules in
modular remote I/O Systems or a fixed component of devices like controllers.
In most cases, a higher-level engineering tool is used in the relevant system environment.
Unfortunately, there is often no integration option in this case, or no consistent one.
Therefore, we have endeavored to find easy-to-use solutions for the relevant cases. For
this reason, various options are implemented for the IO-Link device tool.
WAGO IO-Link Configurator can be operated as a standalone program or via TCI.
10.2.3.4.1 Operate via TCI (Tool Calling Interface)
TCI is a very simple software interface for integrating device software into engineering
tools. TCI is specified by PNO (PROFIBUS Nutzerorganisation e.V.) and is now available
as an open interface for PROFIBUS and PROFINET. Unfortunately, only a few manufac-
turers support this interface. They include Siemens, with STEP 7 and the TIA Portal, and
Phoenix Contact with PC Worx.
TCI is launched from the network configurator of the engineering tool. With Siemens
STEP7, this is “Hardware Config.” Right-clicking on the desired device and selecting the
“Launch Device Tool” function launches the IO-Link device tool. In the process, the engi-
neering tool passes all the devices supported by the tool. They then appear in the topol-
ogy. Under “Extras,” you can choose whether only the device selected in STEP 7, the
network line with the selected device or all network lines are shown in the topology.
The topology cannot be changed by the tool. Although the supported masters appear in
the device catalog, they can only be added, configured and deleted by the higher-level
engineering tool.
When called via TCI, the tool handles the following functions:
• Diagnostics, identification, parameterization and display of process data of WAGO IO-
Link devices
• The output process data can sometimes be written if the PLC has a connection to the
WAGO IO-Link master. With some masters, write access to the process data is also
possible if the PLC does not have a connection. This can be helpful in the installation
phase in order to test functions at this stage already, even without a PLC. You can find
information on the exact function with the corresponding WAGO IO-Link master in the
latter’s documentation.
• The master is configured by the calling engineering tool.
The data is passed regardless of whether or not a communication connection exists.
• Reading the master’s configuration
The configuration is read from the master and, if applicable, the information from the
TCI is supplemented. However, the data from the TCI call takes precedence. In the
event of inconsistency, an error message appears, and the PLC must write the config-
uration anew with the current data.