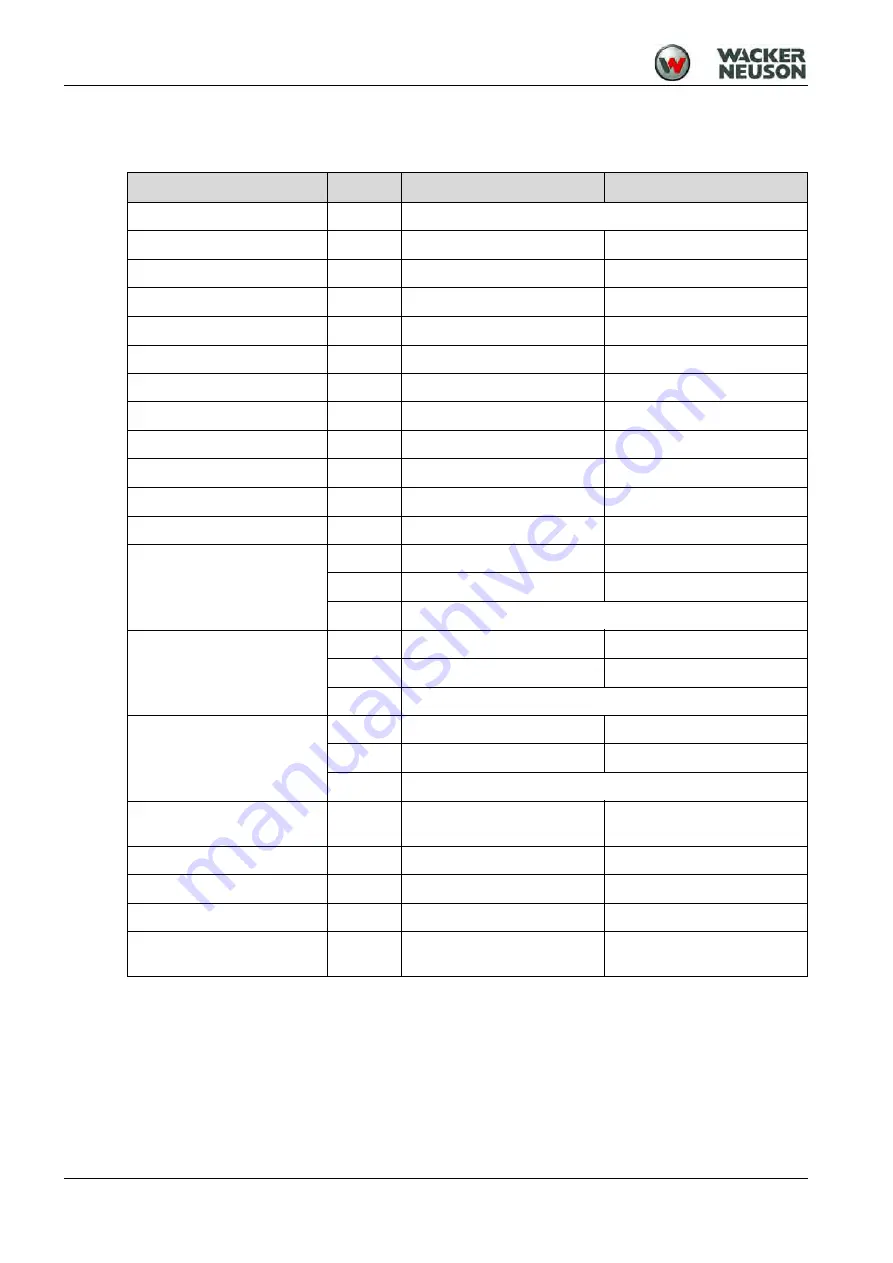
13 Technical data
65
100_0202_td_0018.fm
13.2
Combustion engine
Designation
Unit
DPU 80
DPU 100
Manufacturer
Kohler
Type of engine
KDW 702
KDW 1003
Combustion process
Four-cycle
Four-cycle
Cooling
Water cooling
Water cooling
Cylinders
2
2
Displacement
cm³
686
1,028
Maximum slanting position
°
25.0
25.0
Fuel type
Diesel
Diesel
Fuel consumption
l/h
2.7
3.3
Tank capacity
l
7.2
7.2
Oil specification
SAE 10W40
SAE 10W40
Maximum oil filling
l
1.6
2.4
Max. performance
kW
11.5
18.5
RPM
RPM
3,600
3,600
Standard
DIN ISO 3046 IFN
Rated power
kW
11.0
16.0
Nominal speed
RPM
3,000
2,700
Standard
DIN ISO 3046 IFN
Rated power output
kW
9.6
12.0
Operating speed
RPM
3,000
2,700
Standard
DIN ISO 3046 IFN
Upper engine speed without
load
RPM
3,100
2,800
Air cleaner
Dry-type air cleaner
Dry-type air cleaner
Type of starter
Electric starter
Electric starter
Voltage of starter battery
V
12
12
Battery capacity (nominal
value)
Ah
50
50