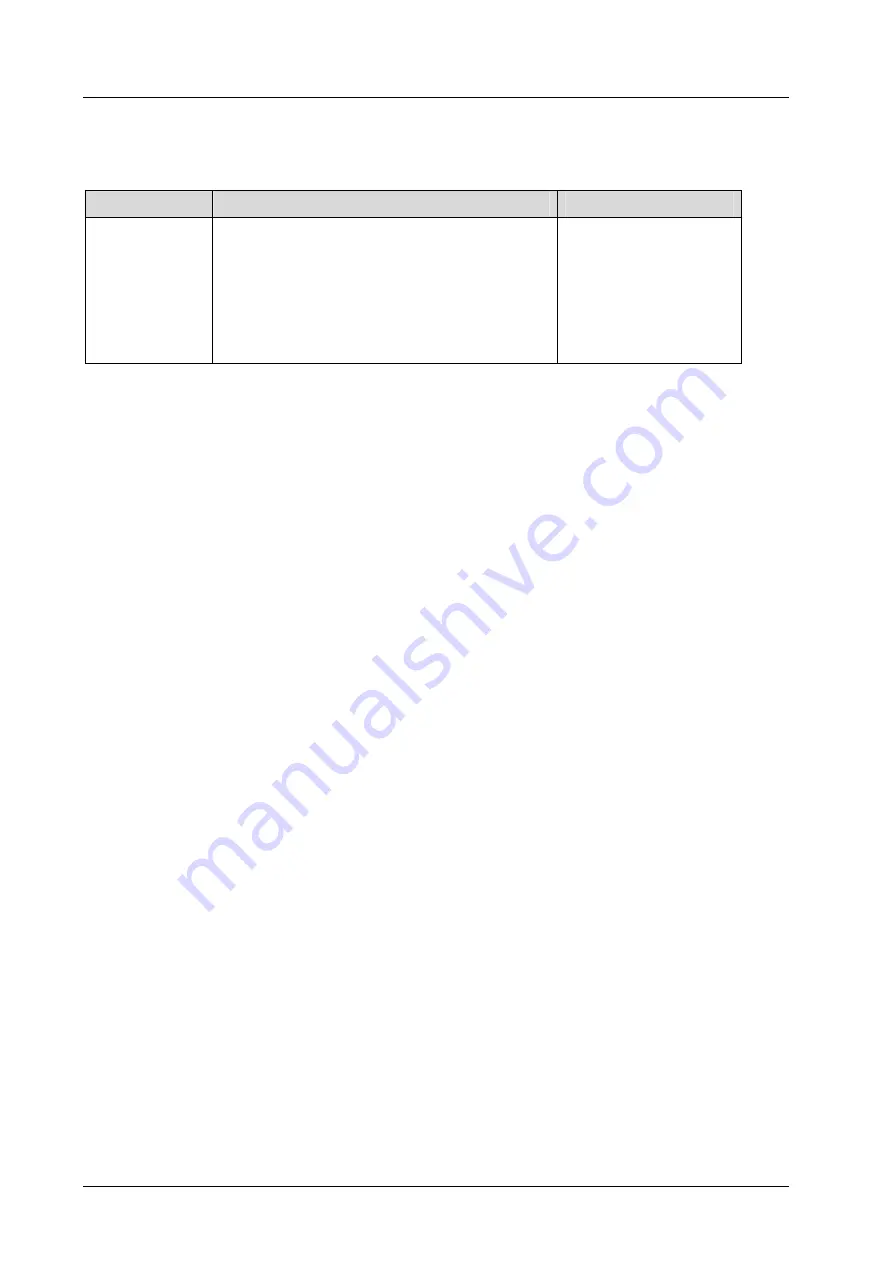
W
.
E
.
ST
.
Elektronik GmbH
Page 34 of 45
POS-124-*-PDP-1121
13.02.2013
5.2.33
PROCESS DATA (Monitoring)
Command
Parameters
Unit
WA1/WA2
W1/W2
X1/X2
XD1/XD2
XK2
V1/V2
U1/U2
Actual command position axis 1 / 2
External command position axis 1 / 2
Feedback positon axis 1 / 2
Control error axis 1 / 2
Synchronisation error at axis 2
Speed set point 1 / 2
Control signal axis 1 / 2
0,01 mm
0,01 mm
0,01 mm
0,01 mm
0,01 mm
0,01 %
0,01 %
The process data are the variables which can be continuously observed on the monitor or on the oscillo-
scope.