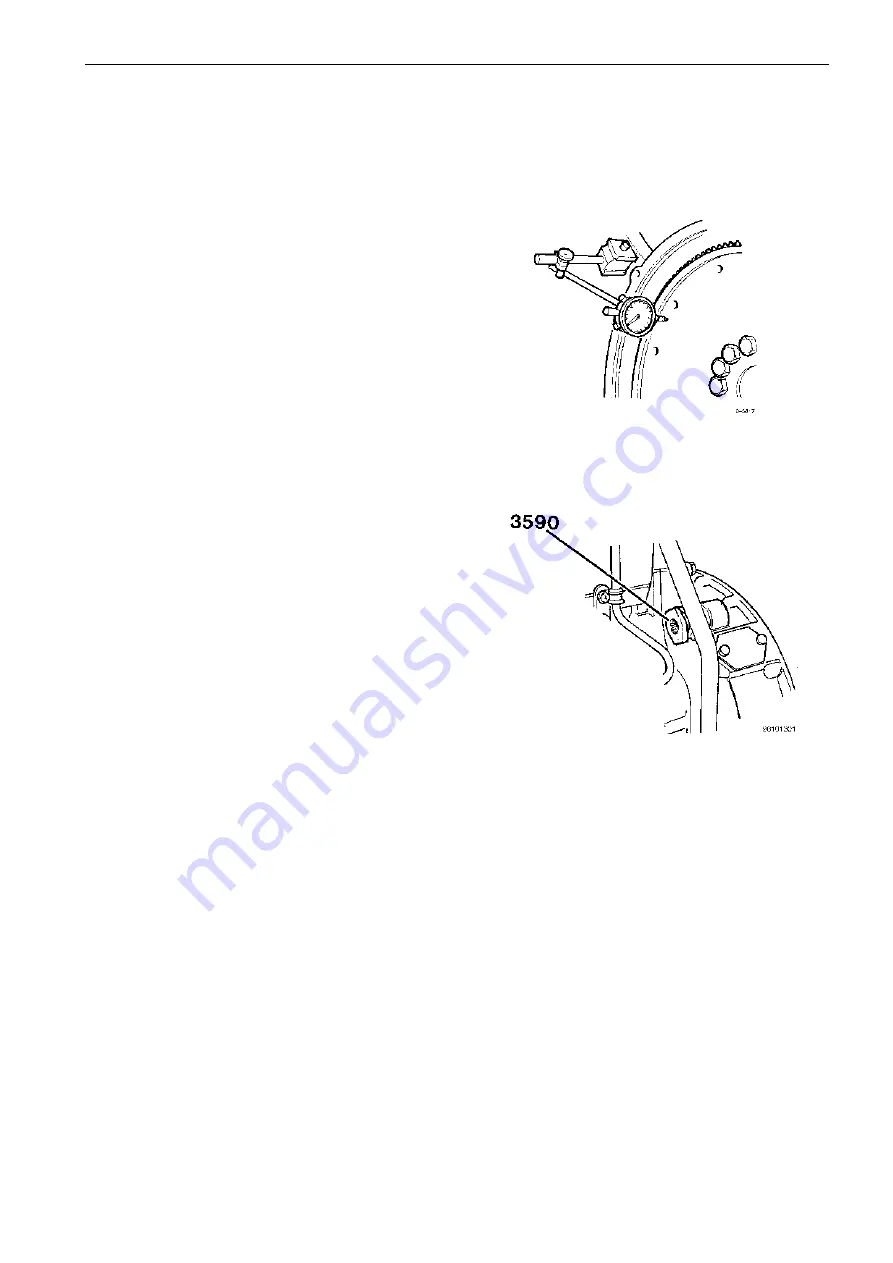
Group 21
Service procedures - engine
71
Reconditioning
When reconditioning, keep to the following routines:
1
Alignment (only as required).
2
Check for cracks.
3
Measure the bearing pins. See ”Workshop manual, Tech-
nical Data”.
4
Grind to undersize as specified in ”Workshop manual,
Technical Data”.
5
Check for cracks.
6
If you are going to re-nitro-carburize (after grinding to under-
size more than 0.5 mm (0.020"), please note: Nitro-carburiz-
ing can be performed using the gas or salt method based on
the operator’s experience in carrying out the treatment.
7
Check for throw after nitro-carburizing.
8
Align if necessary (throw between 0.2–0.7 mm (0.0079–
0.0276")).
9
Carry out a magnetic powder test.
10
The crankshaft must be carefully lapped and cleaned after
nitro-carburizing. The crankshaft must always be thoroughly
cleaned after reconditioning. In order that all oil channels are
cleaned efficiently, late production crankshafts are fitted with
threaded plugs in each piston rod. These plugs should be re-
moved during the cleaning procedure.
Flywheel, checking for warp
Special tools: 998 9876, 999 9696, 999 3590
1
Mount the dial indicator in a magnetic stand and set the dial
indicator to zero with the probe against the flywheel.
2
Crank the flywheel with tool 999 3590, noting the max and
min. values.
3
The difference must not exceed 0.15 mm (0.0060") at a
measuring radius of 150 mm (6"). In the case of excessive
warp, remove the flywheel. Check for dirt or unevenness be-
tween the flywheel and the crankshaft contact face.
4
Remove the rotating tool.
Summary of Contents for TAD1630G
Page 1: ...Workshop manual TAD1630G GE P V TAD1631G GE TID162AP TWD1620G GH TWD1630G GE P V TD164KAE ...
Page 2: ......
Page 18: ...Design and Function Group 21 16 Engine Design and Function ...
Page 80: ...Service procedures engine Group 21 78 Application of sealant to cylinder block ...
Page 162: ...160 ...
Page 164: ...7742302 English 10 2002 ...